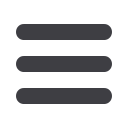
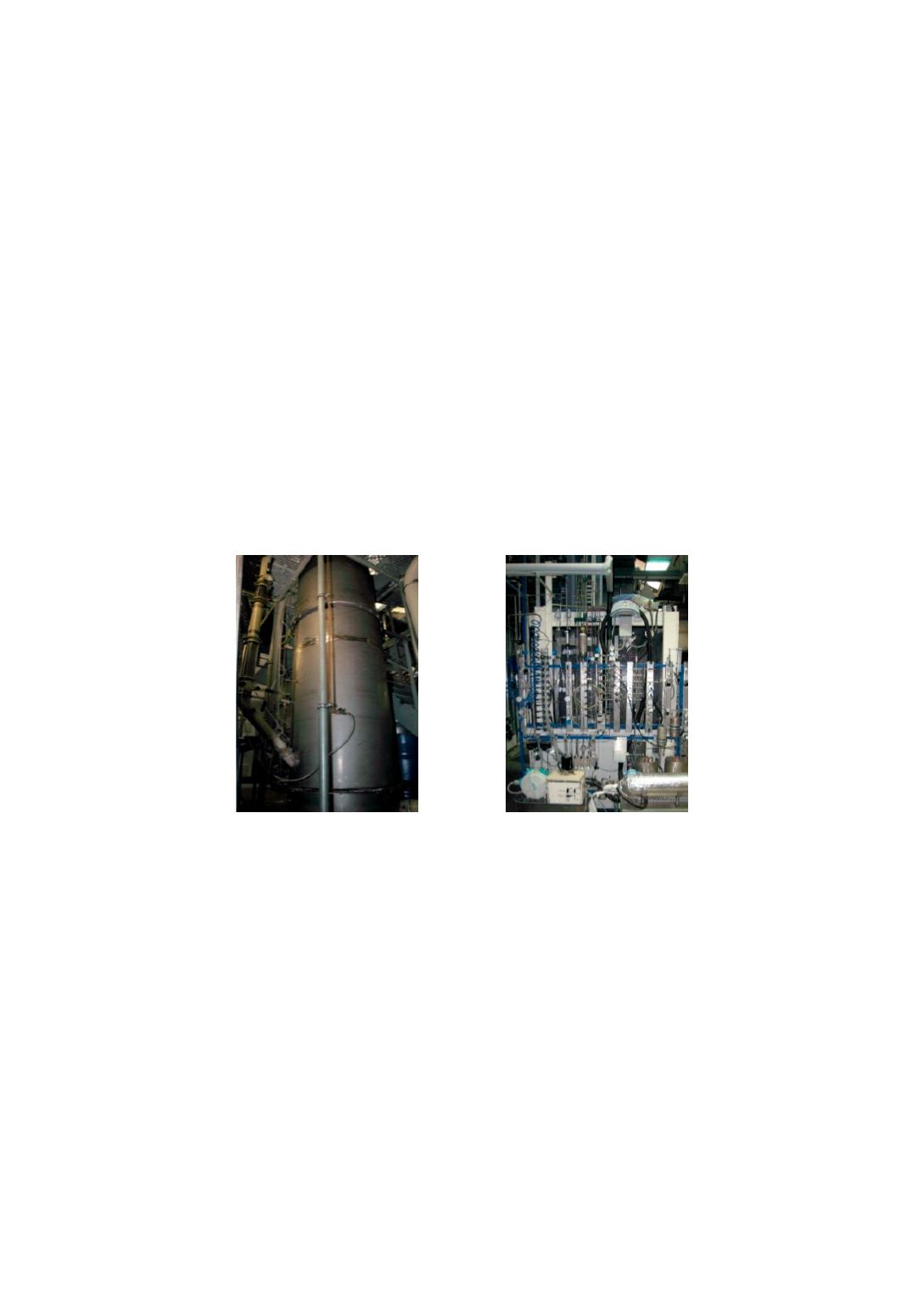
varied within wide ranges. By employing different powders the influence of the grain
size distribution was also examined.
To characterize the fluid dynamics in the fluidized-bed pilot plant the gas bubble
behavior was measured by means of a capacity measuring probe system at different
axial and radial positions throughout the dense bed. This well approved measuring
method [4, 5] provides information on the distribution of gas bubbles in the form of
data on the fractions, velocities, dimensions and frequencies of bubbles, which are
important validation parameters for the fluid-dynamic model.
Beside the bubble behavior, particle entrainment was also measured and investigated
by means of the pilot plant under different operational conditions, by mass flow rate
and particle size distribution.
Continuous MCS pilot plant
To obtain basic data for the validation of the chemical model, a continuous small-scale
Mueller-Rochow pilot plant is used. The mini plant allows operating conditions such
as gas flow rate, operating pressure and temperature to be varied. Furthermore, the
influence of different particle size distributions and catalyst mixtures, on yield,
selectivities and conversion rates can also be observed. From the data gained, the model
parameters “reaction constant” and the “order of reaction” were determined.
Figure 3
: Pilot plants used for the experimental investigations of the fluid dynamics (left) and the
chemical reaction (right)
Using the experimental data provided by these two pilot plants, the simulation model
was gradually and continuously developed, improved and validated.
Mueller-Rochow fluidized-bed modeling approach
For modeling the Mueller-Rochow fluidized-bed reactor, a well approved and
established two phase model approach is used [8, 9]. As shown in Figure 4, the
fluidized-bed riser is axially discretized. Each element consists of a well-mixed solid-
gas phase, called the “suspension phase” and a solid-free “gas bubble phase”. The solids
particle distribution in the dense bed is considered to be ideally mixed, whereas the gas
phase rises as plug flow within the fluidized bed. The gas fraction within the
“suspension phase” is determined by the minimum fluidization velocity, while the
excess gas forms bubbles (“bubble phase”). In the “suspension phase”, where gas and
particles are mixed very intensively, the MCS-reaction takes place at the surface of the
particles. The gaseous reactant held within the bubbles bypasses the fluidized bed and
160