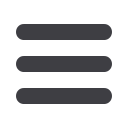
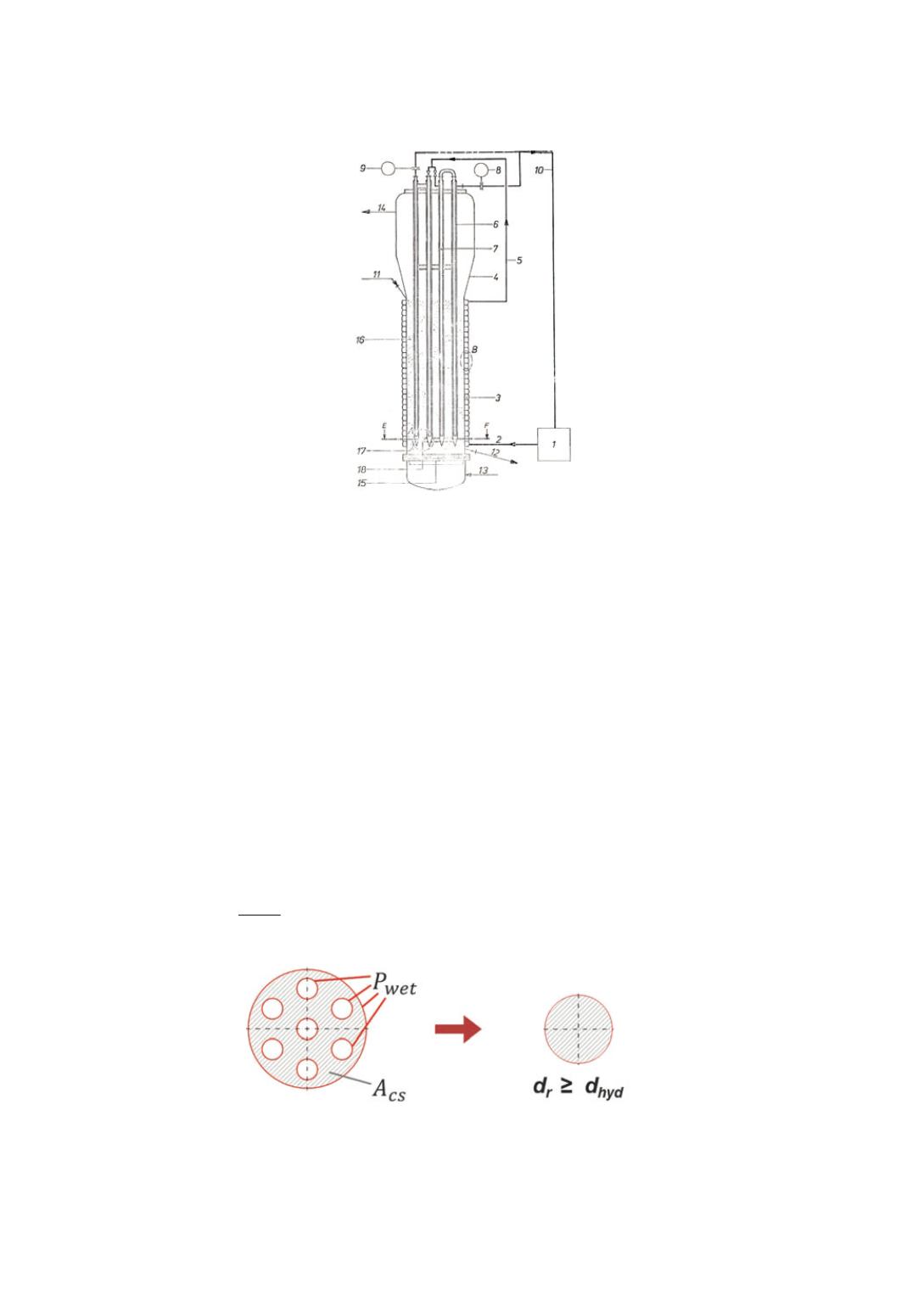
Figure 5
: Example of heat removal internals in fluidized-bed reactors [13]
To follow the goal of developing an integrated and holistic model to simulate and
optimize MCS synthesis, the influence of the heat removal internals on the fluid
dynamics has to be identified and integrated into the simulation tool. Thus the design
of the internals can also be considered for optimization work. At first sight the internals
reduce the volume of reaction and the free cross-sectional area, which influences gas
velocities in the riser. Furthermore, it turned out during the experimental investigations
on the TUHH´s pilot plant that the bubble rise velocity in the dense bed decreased with
an increased total surface area of the immerged internals. That means that the bubbles
are decelerated at the internals surface. At the same time, the lower bubble velocities
lead to a higher gas residence time in the dense bed which means a higher availability
of the gaseous reactant for the MCS reaction. This example underlines how plant
design, fluid dynamics and chemical reaction are closely interconnected. The surface
effects of the internals are characterized by the hydraulic plant diameter
d
hyd
in the
simulation model. As can be seen from Equation 12 and Figure 6, the hydraulic
diameter recalculates an equivalent (reactor) diameter taking all the surfaces of the
internals into account. Here,
A
cs
denotes the free cross-sectional area and
P
wet
depicts
the wetted perimeter.
wet
cs
hyd
P
A
d
⋅
=
4
(12)
Figure 6
: Illustration of the hydraulic diameter
164