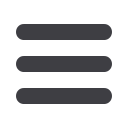
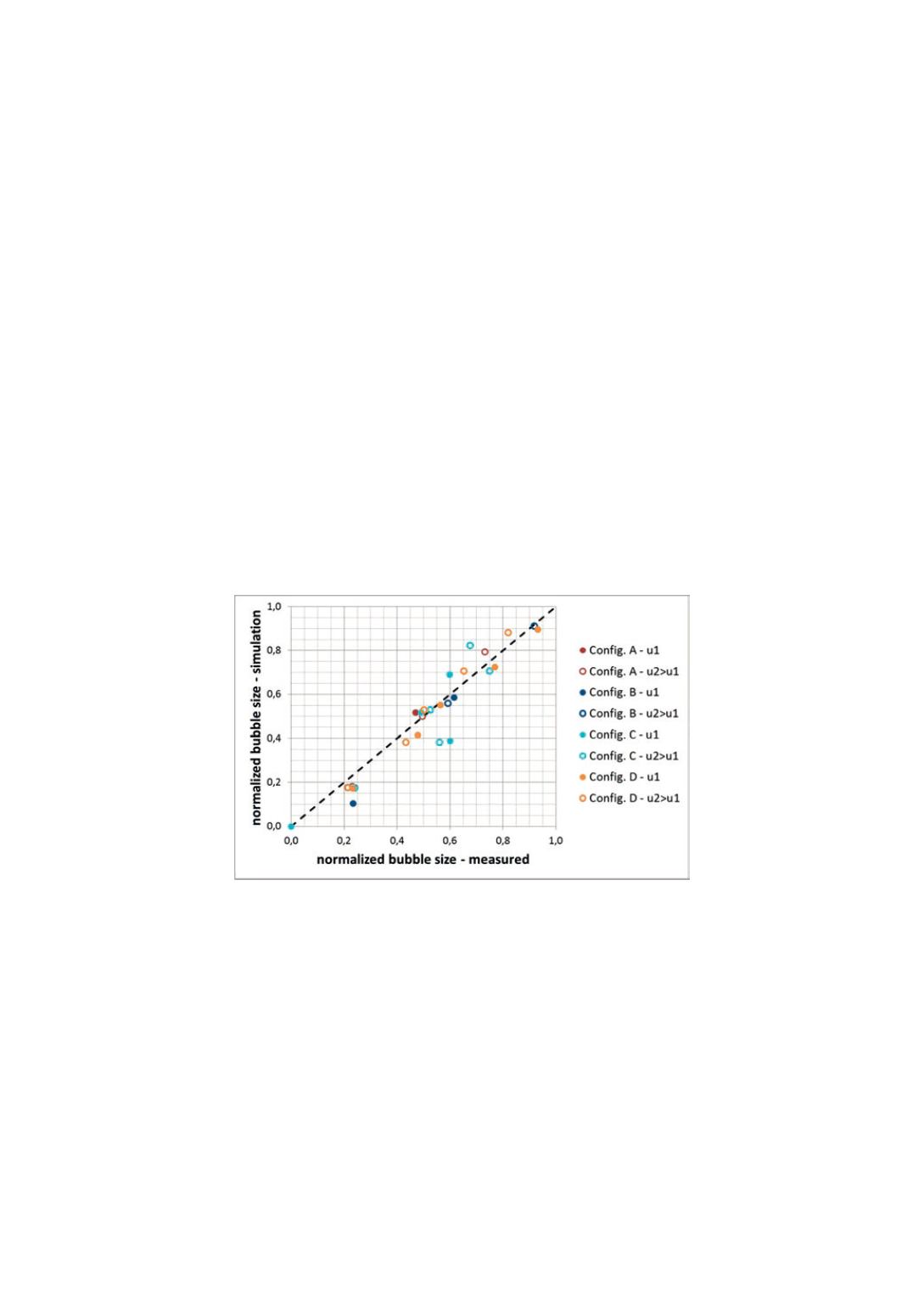
As Equations 9 and 10 from the fluid-dynamic model show, the influence of wall effects
on the bubble rise velocity, relating to the reactors diameter, are already considered. By
replacing the reactor diameter
d
r
with the hydraulic diameter
d
hyd
in Equation 10, the
effect of the internals surfaces can be applied directly to the existing model equations.
In case of a void reactor without internals, the hydraulic diameter corresponds to the
reactors diameter.
Fluid-dynamic model validation results
In order to confirm that the model correctly describes the physical interactions, a model
validation based on experimental data was carried out. For this purpose, fluid-dynamic
data provided from the pilot plant at the TUHH was used. Based on the capacity
measuring probe system the height-dependent validation parameters: bubble fraction
(
İ
b
) bubble size (
d
v
) and bubble rise velocity (
u
b
) are accessible for wide ranges of
operational parameters. Furthermore, discrete pressure-drop measurements along the
dense bed’s height show the axial powder distribution and the fluidized-bed extension.
As an example of the validation results of fluid dynamics, Figure 7 shows a comparison
of the measured and simulated bubble diameters (
d
v
) by means of a parity plot for
different internal configurations (A-D) and for two different superficial velocities (
u
).
Here, the bubble diameters are normalized to the maximum bubble size. As the plot
shows, the fluid-dynamic model corresponds very well to the measured data even for
different internal configurations and gas velocities.
Figure 7
: Model validation results on normalized bubble sizes for different superficial gas velocities
(u1, u2) and internal configurations (A-D)
Modeling particle entrainment
For the Mueller-Rochow reaction and for fluidized-bed reactors in general, the effect
of particle entrainment from the reactor is very significant. The particle entrainment
determines the solid mass flow rate that leaves the reactor with the gaseous product
flow and that has to be separated from the gas flow and recycled to the reactor. Both
the solid separation by means of cyclones and the solids recirculation capacities are
limited by practical considerations. Furthermore, depending on the cyclone’s separation
efficiency, the loss of silicon and therefore the silicon utilization is also affected directly
by the particle entrainment.
165