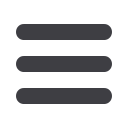
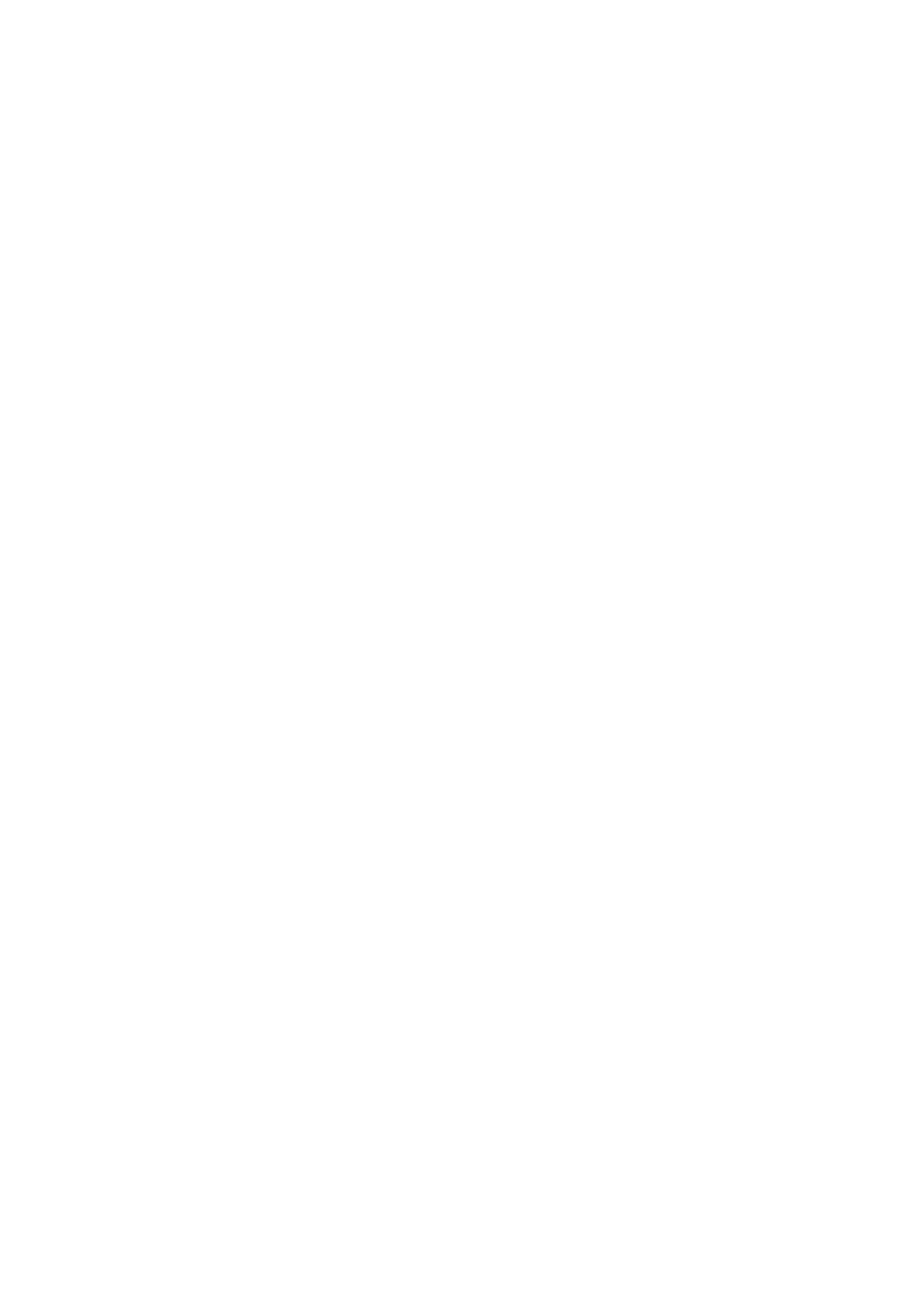
Silicon for the Chemical and Solar Industry XIII
Kristiansand, Norway, June 13 – 16, 2016
Advanced Modeling of Mueller-Rochow Synthesis
Michael Müller
1)
, Stefan Heinrich
2)
1) Wacker Chemie AG,
2) Hamburg University of Technology
Abstract
The Mueller-Rochow synthesis is a key process in the industrial manufacture of silicone
products. Optimizing this process therefore offers high cost-saving potential, with
benefits for a wide range of silicone materials. Modern process design and optimization
are performed with computer simulation tools. For solids-gas processes, such as MCS
synthesis, however, there are no adequate simulation tools available on the market to
describe the complex physical and chemical interactions in a fluidized- bed process.
Improving and optimizing existing MCS reactors as well as designing new reactors that
are optimized as regards selectivity, production and conversion rates, as well as silicon
use, require an integrated and holistic simulation tool covering all the influences that
are relevant to the MCS process. The simulation model presented in this paper
combines the influences of fluid dynamics and design aspects on the chemical reaction,
such as the effects of operational parameters, different grain sizes or fluidized-bed
internals. To validate the simulation tool, extensive experimental investigations were
carried out on different adequate pilot plants in order to adapt the model and to confirm
the reliability of the simulation tool.
Introduction
The Mueller-Rochow reaction, first described in 1940 by Mueller and Rochow, still
forms the basis of industrial-scale silane chemistry [1, 2]. Almost all of the diverse
silicone products known from everyday life are produced via this process. By direct
synthesis, metallurgical silicon, together with chloromethane and copper catalyst, is
converted into chlorosilane monomers at temperatures between 250 and 350°C. The
major silane products from
m
ethyl
c
hloro
s
ilane (MCS) synthesis are shown in
simplified form in Equation 1, in which dichlorodimethylsilane is the most desirable
component and is usually produced in a yield range of 75-94% [3].
(
)
(
)
1.0 ,40
4
3
2
23
3
= −=
+
→ +
−−
n
m
SiCl
H CH SiCl
CH Cl
CH Si
nm
n m
(1)
On a large scale, the reaction is carried out in fluidized-bed reactors, in which silicon
powder mixed with catalyst is fluidized by the second reactant chloromethane (see
157