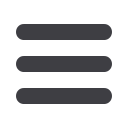
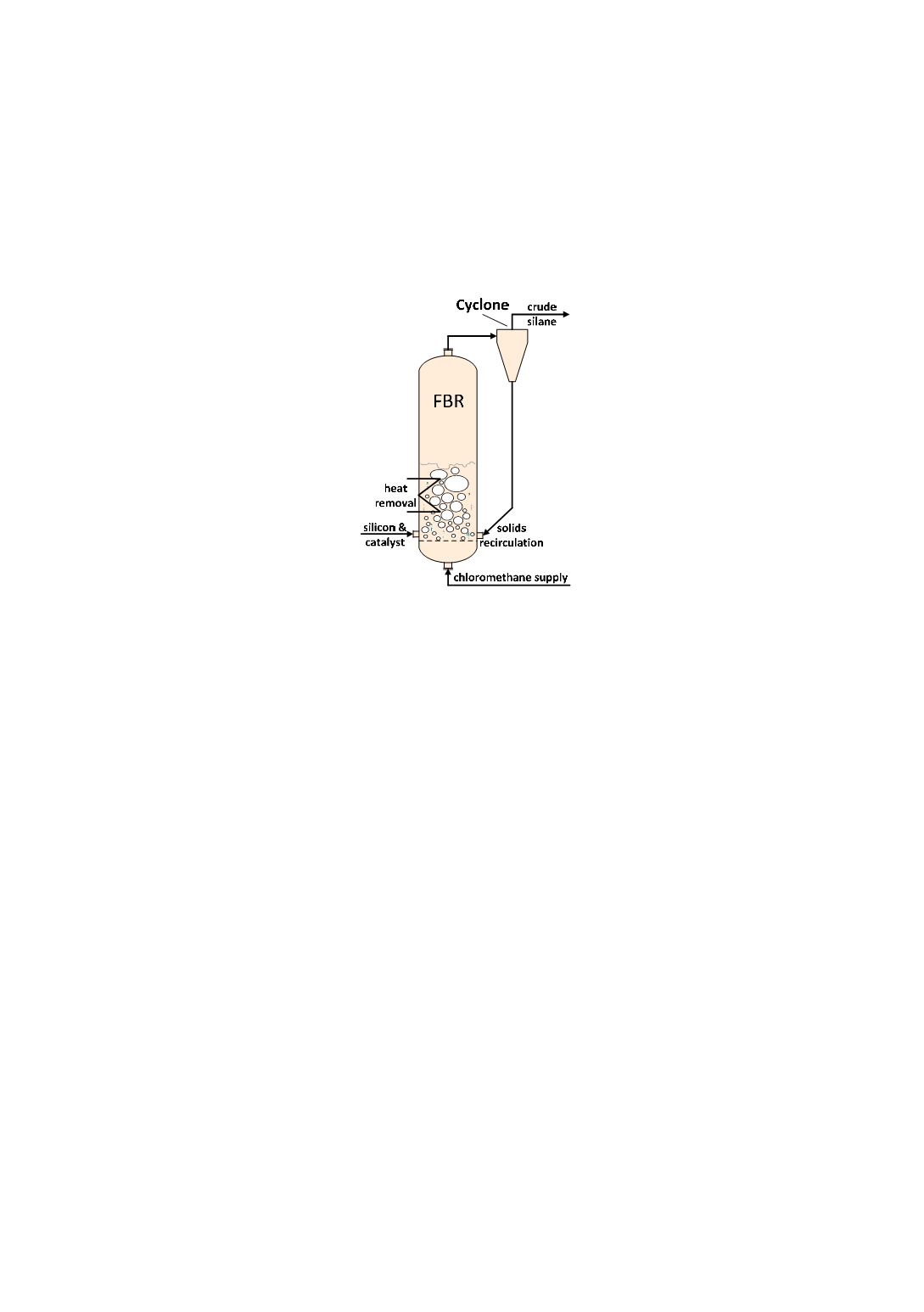
Figure 1). The heat of reaction has to be removed by means of heat-removal internals.
The gaseous product flow at the top of the reactor also entrains solid particles. To
improve raw-material utilization, the particles are separated out in one or more
cyclones, and are returned to the reactor, so that only small amounts of silicon that pass
through the cyclone are lost from the process. Subsequently, the crude silane is
processed in multiple distillation steps.
Figure 1
: Schematic of a Mueller-Rochow fluidized-bed reactor
Since the Mueller-Rochow reaction is a surface-catalyzed gas-solids reaction, the
fluidized-bed apparatus offers optimal conditions for high mass and heat transfer rates.
At the same time, the process as a whole is becoming more and more complex. For
process optimization and equipment design, an integrated and holistic simulation tool
is needed that can cover all the required influences.
Modeling overview
The first step is to identify all the relevant influence parameters to be considered by the
model. Basically, the Mueller-Rochow fluidized-bed process can be split into three
major modeling subgroups that influence each other. First of all there is the fluid-
dynamic behavior of the fluidized bed, which expresses the interaction between the
solid particles and the fluid phase. Fluid dynamics plays a very central role here,
providing information on gas distribution and on the availability of the gaseous reactant
for the chemical reaction, based on gas-bubble behavior.
The chemical reaction is represented in a second modeling subgroup, in which the
influences of reactant concentrations and pressure and temperature dependencies are
considered. Finally, the influence of plant design parameters and their impact on fluid
dynamics, on particle entrainment as well as on the chemical reaction also have to be
taken into account (see Figure 2).
158