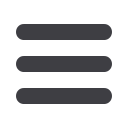

1. If all carbon reacts according to Eq. 7 in the upper zone, then half of the
carbon exits the furnace as CO(g) without ever reaching the hot zone. This
minimizes the amount of CO(g) produced in the hot zone, and hence also
minimizes the amount of SiO(g) that leaves with it since the SiO(g)/CO(g)
ratio in the hot zone is defined by the temperature there and kinetics. Less
carbon in the hot zone therefore implies that less SiO(g) must be captured in
the upper zone, and the silicon yield increases.
2. Eq. 7 captures SiO(g) before it leaves the furnace. This is obviously good for
the silicon yield.
Eq. 7 provides one out of two reactions to capture SiO(g) on its way out. The other is
the so-called condensation reaction (see Eq. 6) which occurs when hot SiO(g) is
cooled as it meets colder raw materials. The reaction product from Eq. 6 is an intimate
mixture of glassy silica and silicon. This substance will gather on particles and in-
between them as a glassy, glue like substance. The reaction is highly exothermic, and
it will therefore heat the charge. Three major problems occur if we have enhanced
SiO(g) concentrations in the upper zone, for example if Eq. 7 fails:
1. The charge may become so hot that the condensation reaction can no longer
continue.
2. The desired even gas distribution is ruined since the glassy condensate forms
a fairly compact lid inside the charge where the gas cannot pass. The gas then
forces its way through narrow channels and we get concentrated welding
torch like flames emerging from small areas at the charge top, often close to
the electrodes. We say that the furnace is blowing when this happens.
Obviously, most of the gas, including the SiO(g), then passes through a very
small fraction of the raw materials. This means that a smaller amount of the
carbon in the raw materials will be exposed to SiO(g). Carbon conversion to
SiC by Eq. 7 then suffers and things get even worse.
3. The condensate lid that prevents even gas distribution also prevents the raw
materials from descending easily in the furnace. We say that the raw materials
are hanging in the furnace. Stoking may then be necessary to help the
materials move downwards. The operator will notice that the charge top
grows higher in areas where this happens if the raw material system continues
to feed the furnace at the normal rate. The area underneath the electrode then
runs out of charge and the cavity wall moves upwards since the material flow
has decreased or even stopped. This continues until the cavity wall has moved
so high up in the furnace that it collapses and large amounts of charge rushes
down to the hot zone. This is usually accompanied with violent outburst of
gas and dust that can rush out of the furnace through the charging gates. This
can be very dangerous in extreme situations.
Large amounts of SiO(g) may arise from various problems. Poor conversion of carbon
to SiC according to Eq. 7 is one. Another is a temperature drop in the hot zone since
the SiO/CO gas ratio in the hot zone increases with falling temperatures. A third is if
we have too little carbon in the raw materials (undercoked furnace), which means that
less quartz molecules will find two carbon atoms to form silicon. Instead they find
only one and therefore ends up as SiO(g) rather than silicon.
A temperature drop in the hot zone can for example occur if raw materials
suddenly rush down to the hot zone as described above. It can also result from too
69