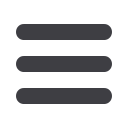
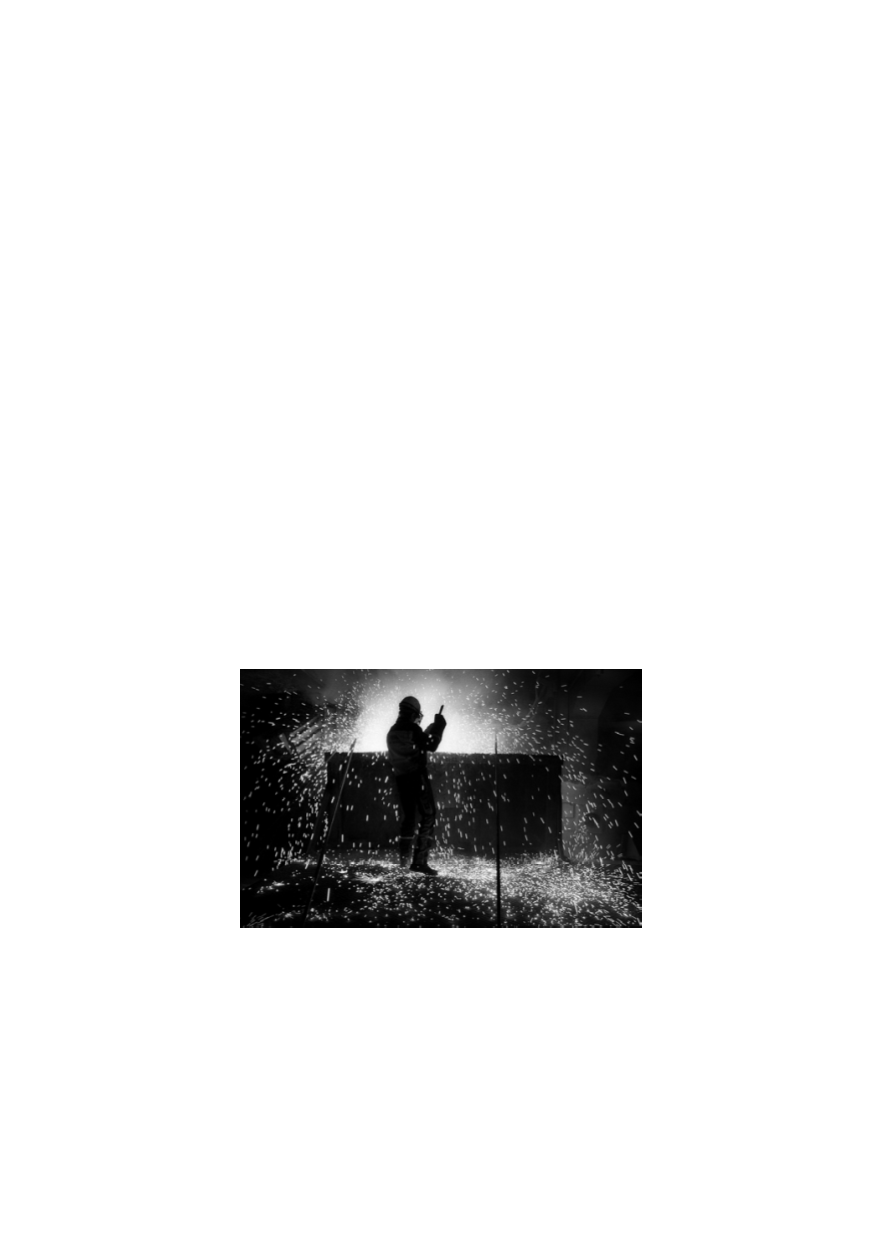
moving raw materials around and removing large blocks from broken electrodes.
Feeding only by truck is not suited for large furnaces.
Charge tubes give the possibility to feed much of the materials automatically. It is
then possible to feed little material quite often rather than large batches less often by
truck. This is referred to as semi-continuous feeding, which has proven to be
favourable both for the process as such, for reducing the wear on the furnace hood and
for reducing emission of for example NO
X
in the off-gas. The main reason is that the
variations in gas production are reduced and the gas distribution becomes more even
so that the temperature peaks are smaller and shorter. The combustion of CO(g),
SiO(g) and volatiles above the charge then becomes more steady and favourable for
low production of NO
X
. The details are complex and not fully understood yet.
Tapping and refining
Liquid silicon is tapped into ladles or moulds through one out of several tap holes in
the side close to the bottom of the furnace. These are repaired on a semi-regular basis.
A lot of hard work in very warm, dusty and tough conditions including splashing of
liquid silicon and intense welding torch like gas flames is required in this area to keep
the tap hole open. Otherwise slag will clog the channel or freezing silicon may cause
problems. The operators use rods of wood, oxygen through hollow rods of aluminium
or iron (beware of iron contamination) or shoots with coarse calibre zink bullets to
keep the tap hole open.
A poorly drained furnace will not perform well. It is essential that a new tap hole is
opened in the correct height and with the correct angel so it meets the silicon inside
the furnace at the right place. It is also essential that the skilful operators manage to
preserve optimal conditions in the tapping area until a new tap hole is opened.
Tapping is continuous, at least for medium size and large furnaces, unless furnace
operation or maintenance requires otherwise.
Figure 2
: Operator working in the tapping area.
The silica fume in the tapping area is collected as good as possible and routed into the
main off-gas channel from the smoke hood to be recovered in the fume filter. Some
furnaces have separate fume filters for the gas from the tapping area.
The typical tapping time for large furnaces is 1 1/2 to 2 hours. The silicon is
normally refined during tapping by purging oxygen and air through it via a porous
plug in the bottom of the ladle while fluxes are added at the top to adjust the refining
slag. The goal is to reduce the aluminium and calcium content to the desired levels,
65