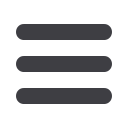
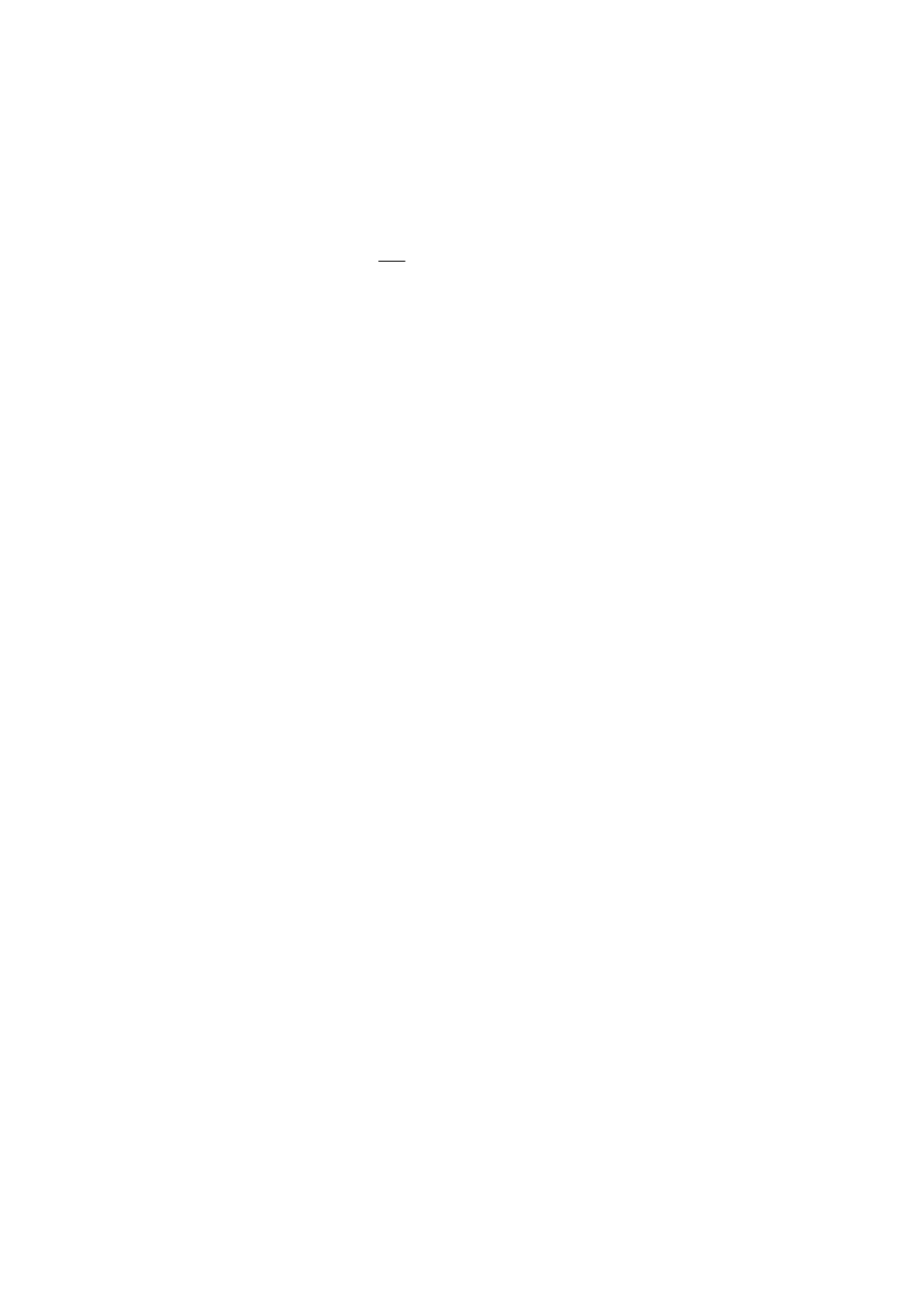
undercoked in practice. The silicon yield may even be better than normal in this case
since extra silicon is produced from the SiC while the silicon yield is calculated based
on the silicon charged as quartz via the raw materials only. However, the silica
production will normally also be higher than usual in this situation since there is then
less carbon than usual in the raw materials to catch ascending SiO(g) according to Eq.
7 before it leaves the furnace top.
If the charge is undercoked and there is no more (or too little) SiC available, the
process becomes truly undercoked. Then the silicon yield drops as we do not have
enough carbon to remove both oxygen atoms from as much quartz as during optimal
furnace operation. This means that some of the quartz that would normally react
according to Eq. 1 and produce silicon, instead must react according to the gross
reaction Eq. 4 and produce SiO(g).
The consequence is that more silica is produced and the silicon yield drops
accordingly. The top of the charge will then often become very hot, the gas
distributing becomes very uneven and the downwards material flow of the charge will
often suffer for reasons already discussed.
Overcoked furnace
u > 0 in Eq. 2, on the other hand, there is more carbon in the raw materials than what
is needed with the current silicon yield. This extra carbon will form SiC that builds up
in the furnace as it does not find enough oxygen in the quartz to leave as CO(g). The
value of b in Eq. 2 is then zero. This corresponds to an overcoked situation.
If you enter an overcoked situation from a period with good furnace operation, the
silicon yield is expected to be almost unchanged, perhaps even somewhat better than
normal since you have more than usual carbon to catch ascending SiO(g) with. More
silicon is then returned to the hot zone where some of it may add to the silicon yield.
The increased capture of SiO(g) also means that less SiO(g) leaves the furnace.
The operators are likely to see a nice and calm furnace top, good tapping conditions
and good production, and they will have a tendency to be happy with a nice day at
work while they should instead start to worry because SiC will gradually build up and
eventually cause major problems if it is allowed to continue long.
The basic problem in the tapping area will be that the SiC after a while will make it
harder for the silicon to drain out from the tap hole. In the charge, the SiC will form
crusts that can prevent a good downwards material flow. Over time, these crusts are
likely to change the geometry of the cavity around the lower part of the electrodes
from wide and well functioning cavities to narrow cylindric cavities where the electric
arc easily jumps over to the cavity wall from somewhere up on the electrode flank as
described above.
Again, the electrode will move fast upwards several tens of cm, but this time it will
have a tendency to rush fast down again as the SiC-cylinder may have almost the
same diameter far up along the electrode so that it does not matter so much for the
current whether the arc burns high up in the cavity or further down.
So if you observe an electrode that rushes fast up and fast down again, you are
welcome to suspect an overcoked furnaces. To remove the SiC, you have to run the
furnace slightly undercoked, with the unpleasant side effects of undercoked operation.
Uncertainties in the carbon balance
As stated earlier, we need too add 1% more carbon in the raw material mix for every
2% increase in the silicon yield. This means that the carbon balance is a dynamic
quantity that the metallurgist must pay much attention to.
72