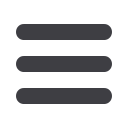
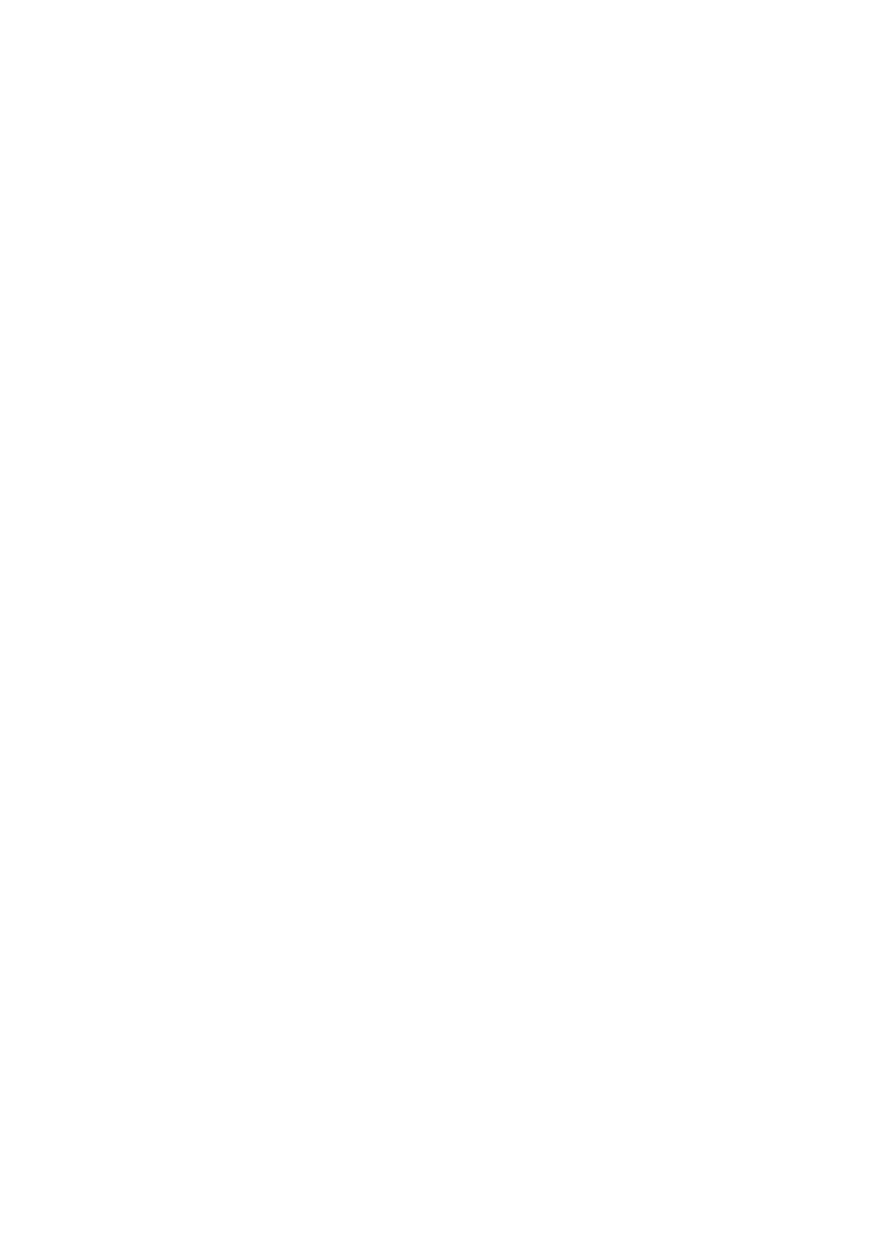
There are three major difficulties in reaching a perfect carbon control if we skip
discussing stupid errors in the weighing system or in other basic measurement- and
control systems.
The first is that we do not know exactly how much carbon we lose from the
weighing system until the carbon enters the production zones down in the furnace.
Materials may fall off the transport band or stick to it if wet. This can be checked and
estimated by frequent inspections of the transport route.
The second is that we have variations in the moisture of the carbon materials that
are difficult to estimate, especially if carbon materials are stored outside. Then a
heavy rain fall will give soaking wet materials close to the surface of the big pile of
raw materials while the interior may preserve its former moisture level. The water
content will then vary dramatically depending on from where in the pile the materials
are taken from day to day. The obvious solution is to store all carbon materials in a
building so that rain, snow or sun make no difference to the moisture levels. In any
case, the water content of the carbon materials must be measured on a regular basis
since variations will be found even for materials stored indoors. The frequency will,
however, be much higher for materials stored outside.
The third difficulty is that we do not know exactly what the silicon yield really is at
any given point in time. There are several reasons for this. One is that you cannot
blindly trust the amount of silicon that is tapped during a day since there may be much
more or much less silicon left inside the furnace now than it was 24 hours ago. And
you have no way to know what that difference is. Also, even though the silicon
process is often “promoted” as a slag free process, this is not really the case. The raw
materials have significant amounts of calcium and aluminium that partly leave the
furnace dissolved in the silicon and partly as a (mostly) Al
2
O
3
, CaO and SiO
2
containing tapping slag. The amount of tapping can vary very much from one tapping
to the next and from one day to the next. It is not practical to measure the amount of
tapping slag with high precision.
This means that there are considerable errors both in the actual amount of carbon
that ends up inside the furnaces over a day and in the amount of liquid silicon
produced in the same period. This means that we need to trend the estimated carbon
addition and the silicon production over several days, and consider adjusting the
carbon balance if we observe that significantly too much (or little) carbon seems to be
added during the last 2-5 days or so.
Neither do we know how much SiC that has been produced or consumed in the
report period. To estimate this, it is wise to calculate a total silicon balance and see
how silicon units accumulate or is consumed over weeks and months.
The problem with finding a good estimate for the true silicon yield based on the
amount of tapped silicon means that many metallurgists use the silica production for
estimating the silicon yield.
Finally it is noted that all metallurgists know that a high content of calcium in the
tapped silicon indicates that the temperature in the production zone is high provided
that no significant changes are done to the raw material mix. It is then reason to
believe that the electric arc is burning towards the metal pool. A low calcium content
will indicate either (a) that the electrode tip is too high up in the furnace or (b) that the
electric arc burns high up on the electrode flank or (c) that the process is undercoked
or (d) that the C
3
value is too low or (e) that considerable amounts of silicon is stored
inside the furnace. Who said that the silicon process was easy to understand?
.
73