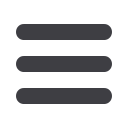
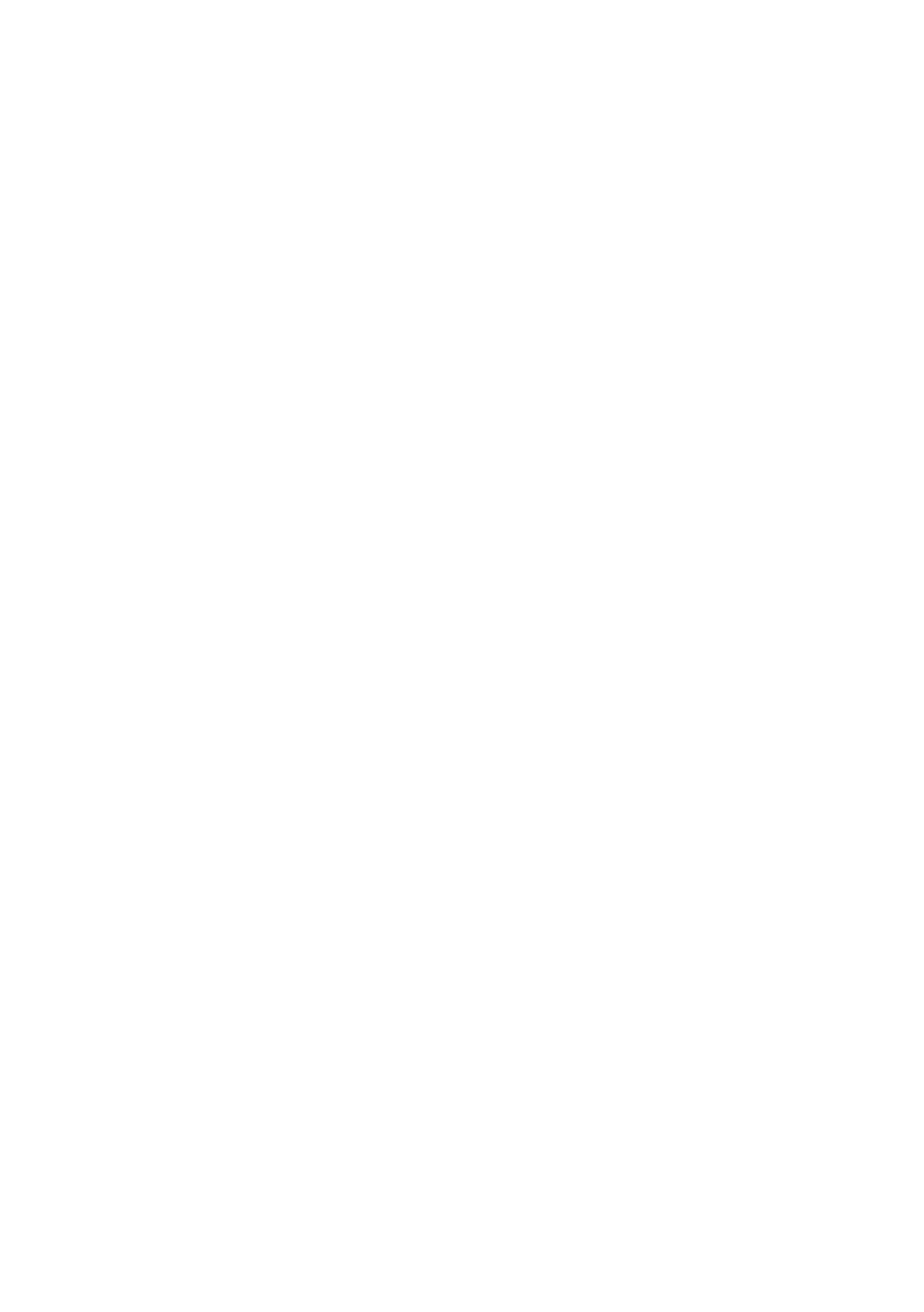
high temperatures are reached by an alternate current electric arc burning preferably
from the tip of the electrode to the metal pool below it.
A large gas filled cavity forms around the lower part of the electrode because the
raw materials do not always move easily downwards on their own for reasons to be
explained later. The high energy density clears the area around the electrode tip to
create a cavity in which the electric arc can burn and deliver high enough
temperatures for silicon production.
The electric arc can also burn from the flank of the electrode to the cavity wall and
passes through the hot electrically conducting materials there, most importantly C and
SiC, and continue all the way to the other electrodes. On its way, energy is released in
the cavity walls and wherever the current goes by ohmic heating and by small electric
arcs from one conducting particle to the next. Calculations show that the core of the
electric arc can exceed 25 000K. Hence radiation is important for heat transfer in this
zone.
Silicon is primarily produced in the hot zone by Eq. 5, but also in the upper zone
by Eq. 6.
SiC(s) + SiO
2
(l) = 2 Si(l) + CO(g)
(5)
2SiO(g) = Si(l) + SiO
2
(l)
(6)
SiO(g) produced by several reactions in the hot zone will react with carbon in the
upper part of the furnaces according to Eq. 7.
SiO(g) + 2C(s) = SiC(g) + CO(g)
(7)
Eqs. 6 and 7 are the most important reactions to prevent SiO(g) from being lost from
the charge top.
Selected operational aspects
A comprehensive description of all important operational aspects will take all to long
to give. Only a few selected aspcets are described below.
In the upper zone, the quartz is heated as it descends and meets hot gas emerging from
the lower/inner zone. The quartz melts in the lower part of this zone and flows down
under the electrode as a highly viscous fluid. Little else happens to the quartz in the
upper zone, expect that it may start reacting when it gets to the cavity wall and
becomes exposed to high temperature gases and radiation from the electric arc.
Too large quartz lumps will reach the hot zone without being properly heated in
the center. This will lower the temperature in the hot zone, which is bad since the ratio
of SiO(g) to CO(g) then increases, bringing more SiO(g) out of the zone together with
the CO(g). Recovery of SiO(g) then becomes more difficult and the losses increase.
Too small quartz fractions, on the other hand, may also cause problems since the
gas distribution may then suffer. Mechanically and thermally weak quartz will add to
the fines fractions and is in general unwanted.
The carbon materials will also be heated in the upper part of the furnace.
Preferably they react completely to silicon carbide according to Eq. 7 in the upper
part.
Even gas distribution, small enough carbon particles and good intrinsic SiO-
reactivity promotes this reaction which is extremely important for two reasons:
68