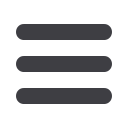
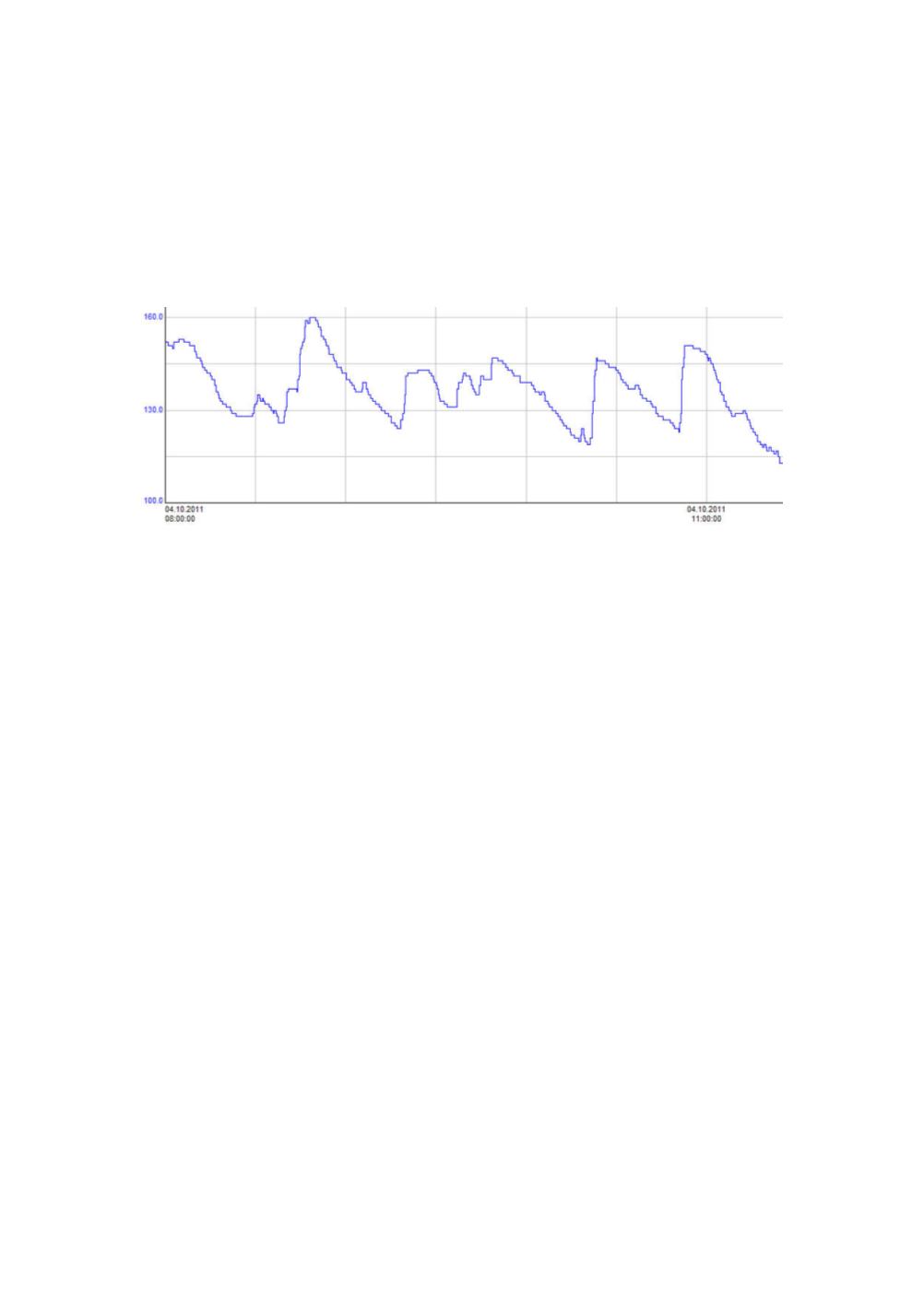
cavity wall increases. By my experience, it often takes in the order of 20-50 minutes
before the electrode tip returns to the original position.
While it was burning up in the cavity wall, the electric arc delivered much energy
there and less than usual underneath the electrode. More than usual quartz melted
down and less was consumed below the electrode during this cycle, and there is likely
a lot of molten quartz under the electrode as it returns to its original level. It would be
no big surprise if the electrode now jumps over to the cavity wall again and repeats
the cycle as shown in Figure 4.
Figure 4:
Example of an electric arc that repeatedly jumps over to the cavity wall about 30 cm
up on the electrode flank and gradually works its way down again in about half an hour.
If this continues, it would be a good idea to consider increasing the set point for the
current for a while to add more energy below the electrode and by that “clean up the
area” removing surplus charge. As soon as the electrode dynamics return to normal,
you should return to the normal C
3
value as this is by experience the value at which
the furnace performs best over time.
I would recommend considering a slightly higher carbon balance for the raw
material mix in the charge if the temporary increase in the C
3
value does not work
within some hours since the problem may instead be caused by too little carbon in the
charge.
Significant wear of the electrode flank is a likely result if this is allowed to
continue for long periods. The lower part of the electrode may then become very thin,
which would cause severe problems to the furnace operation. At some point the thin
tip of the electrode may suddenly break off. This is a larger problem in the
ferrosilicon process than it is for the silicon process as the iron in the charge increases
the electric conductivity of the cavity wall significantly.
Problematic electrode erosion may also occur if there are too much carbon in the
center of the furnace compared to the outside. The electric arc may then have a
tendency to burn towards the center of the furnace, eroding away the lower part of the
electrode on the flank facing the center.
The carbon balance
Undercoked furnace
The case b > 0 in Eq. 2 means that SiC already present in the furnace is consumed and
serves as an additional carbon source for the reduction of quartz. It also serves as a
silicon source adding to the silicon from the quartz. The value of u is then zero. This
technically corresponds to an
undercoked process
where we have too little carbon in
the raw material mix. However, if enough SiC is available, the process may not be
71