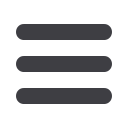
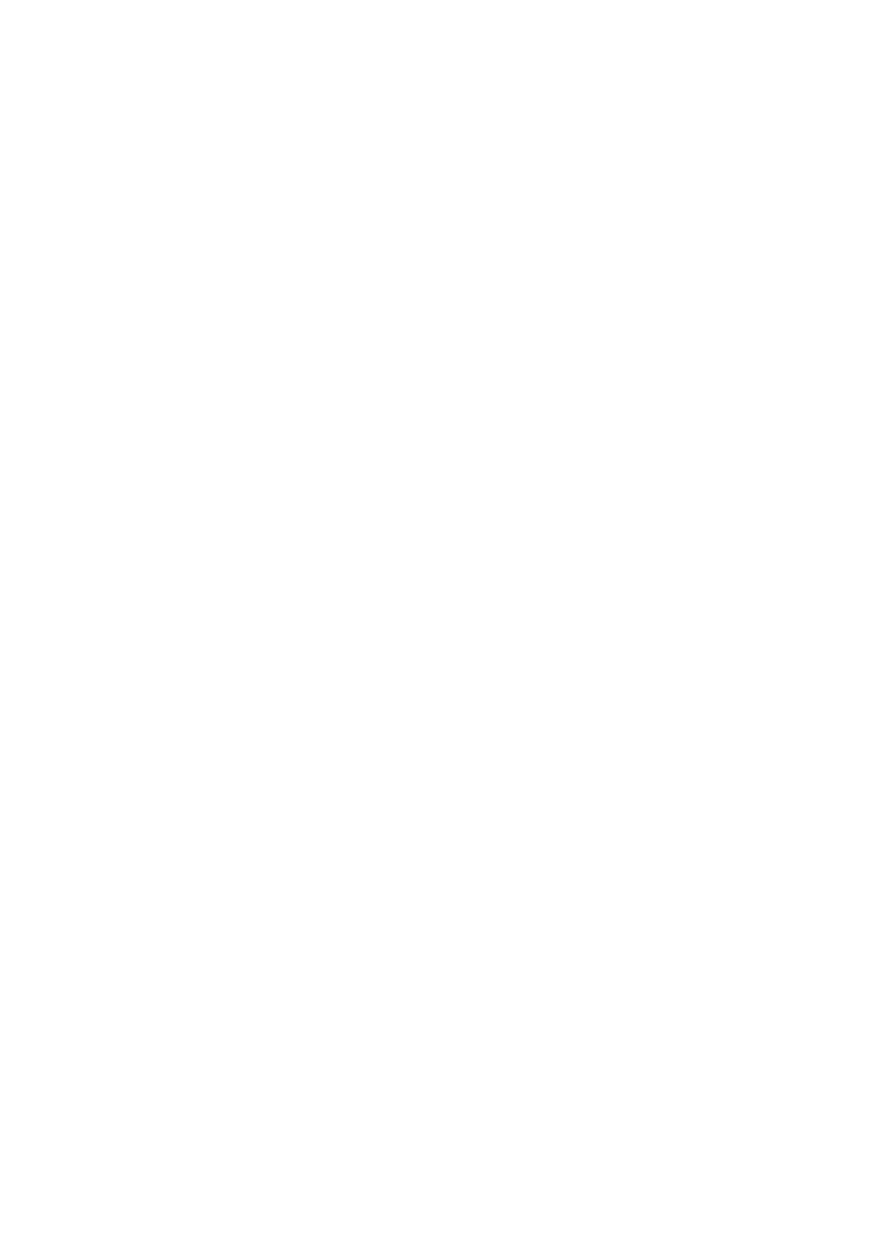
Furnace size
Carbothermic silicon furnaces range from very small units in the order of 5 MW to
about 45 MW. The process is run 24 hours a day week in and week out unless there
are problems with the operation or maintenance is required.
Energy consumption and raw material demand
A well operated medium or large furnace uses about 10.5 MWh per metric ton tapped
silicon and upwards depending on the electrical efficiency of the furnace and the
silicon recovery. A 35 MW furnace hence produces just over 3 ton silicon and 1 ton
silica an hour. This requires that about 7500 kg quartz and 2800 kg fix-C (reactive
carbon) are fed to the furnace every hour. The actual amount of carbon materials is in
the same order as the quartz, but varies with the ratio of coal, coke, charcoal and
wood chips since these materials have significantly different contents of water,
volatiles and ash. Tapping is continuous unless there are problems with the furnace
operation, the tapping area or with critical equipment.
The furnace pot
The diameter of the steel furnace pot for a large furnace is over ten meters while the
height from the bottom steel plate to the top of the charge may be six-seven meters.
The height of the charge may be three-four meters. The furnace pot can be stationary
for small furnaces, but it rotates slowly for most medium sized and large furnaces,
typically with a speed corresponding to one full turn in about a month. The rotation is
partly to protect the lining below the electrodes and partly to help break up crusts that
might otherwise form in the charge. Too fast rotation may cause electrode breakages.
The electrodes
The process requires a lot of electric energy which is delivered by three consumable
carbon electrodes at a relative low voltage and high currents. Typical values are 150-
300V and 50-100 kA.
The electrode diameter for large furnaces is in the order of 1.5 meters. The
electrodes are going through sealed openings in the smoke hood. They are lifted and
lowered automatically in combination with changing transformer settings in response
to changes in the furnace resistance, furnace conditions and electric strategy.
Many silicon furnaces use approximately 2.5 meter long full sized prebaked
electrode elements which are screwed together with carbon nipples to compensate for
an electrode consumption in the range 50-100 kg/ton tapped silicon. Other furnaces
use a relatively small graphite core in the centre of a steel cylinder filled with
Søderberg electrode paste known from production of ferrosilicon [2]. The Søderberg
paste is baked to solid electrode in the electrode holder region. This so-called
compound electrode is then extruded from the steel casing to keep the contamination
of iron from the steel casing at an acceptable level. Such electrodes are less expensive
than prebaked electrodes, but require more complex electrode equipment. They also
have some additional functional challenges compared to prebaked electrodes, but may
have some metallurgical advantages due to the high conductivity of the graphite core.
Feeding raw materials
The raw materials are mixed after weighing and then fed to the top of the furnace
either through several tubes like the one shown on Figure 1 or by special trucks
delivering batches through gates in the side walls of the smoke hood, or both. These
gates are also used for inspection of the furnace top and for stoking and tasks like
64