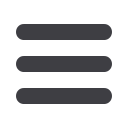
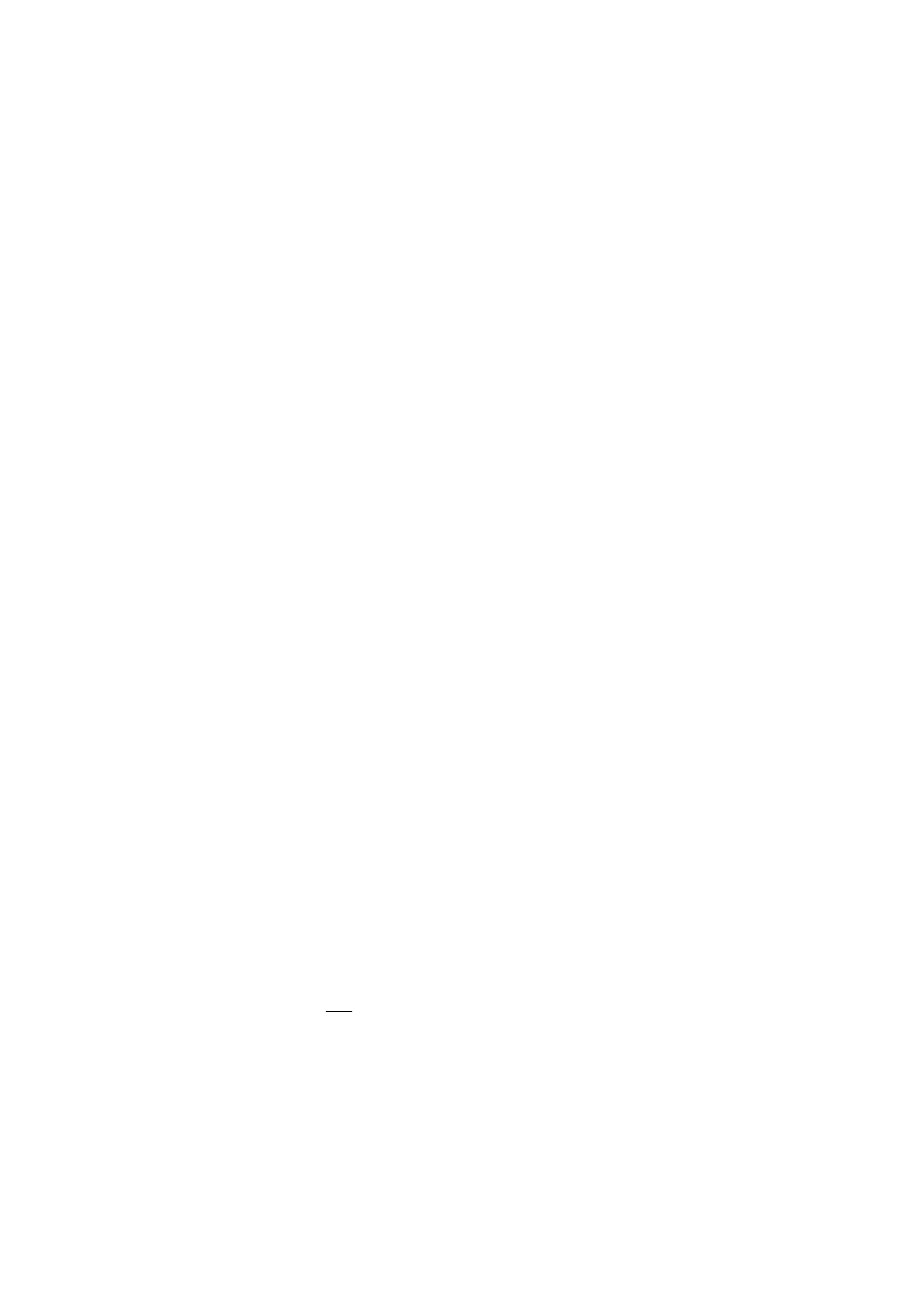
which will vary from one customer to the other. Further refining may be done after
tapping, if needed. This is normally decided upon receiving the analysis of samples
taken shortly before the ladle is full. Stable furnace operation and tapping makes the
refining much easier.
Suggested literature on tapping is [1] and [3] and on refining of silicon [1] and [4].
Process gases, silica fumes and energy recovery
Almost all free carbon that is added in the raw materials will leave the furnace as
CO(g). Only a small amount of it will be dissolved in the liquid silicon. A small
fraction of the CO(g) will come out of the tap hole, but most of it will leave through
the charge top together with some SiO(g) produced in the hot zone and water vapour,
volatiles and other gases driven off from the carbon materials as they are heated.
These very hot gases mix with air sucked in through the charging gates above the
charge and they will burn to CO
2
(g) and fine SiO
2-
particles called silica fume or silica
dust as they are sucked into the filter unit where the silica is collected. The silica is
sold, mostly to producers of concrete. Typically 10-20% of the quartz ends up as
silica, depending on the furnace operation.
Modern furnaces normally have energy recovery from the hot process gases before
filtering out the silica. Producing hot water for district heating is more energy efficient
than producing electric energy, but not all plants have a demand for district heating
nearby.
Basic overall chemical reactions
In the carbothermic silicon process we use carbon at high temperatures, in the order of
2000 C, to remove the two strongly bonded oxygen atoms from the silicon in quartz
(SiO
2
) according to Eq. 1.
SiO
2
(l) + 2C(s) = Si(l) + 2CO(g)
(1)
If we have exactly 2 moles of chemically active carbon (fix-C) for every mole of
quartz, we say that the
carbon balance
is 100%.
However, several other chemical species are present at these high temperatures,
most notably SiO(g), CO(g) and SiC(s), giving the more realistic Eq. 2 which is
discussed in much more detail for example in [1] than it is here.
a SiO
2
(l) + b SiC(s) + c C(s) = x Si(l) + y SiO(g) + z CO(g) + u SiC(s)
(2)
This equation allows both for net production of silicon carbide in periods where we
add more carbon that we should have done (overcoked process, u>0 and b=0) or net
consumption of SiC that has been deposited earlier if we add less carbon than we
should have done (undercoked process, b>0, u=0).
The special case b=0 and u=0 means a process where SiC is neither consumed nor
produced overall. Eq. 2 then transforms to Eq. 2.a when the parameter ‘a’ in Eq. 2 is
assigned the value 1 and x is the silicon yield (the fraction of Si in the quartz in the
raw materials that comes out of the tap hole as liquid silicon).
SiO
2
(l) + (1+x) C(s) = x Si(l) + (1-x) SiO(g) + (1+x) CO(g)
(2.a)
This is the situation we are aiming for where the carbon balance is optimal and good
furnace operation may prevail for a long time if everything else is also optimal.
66