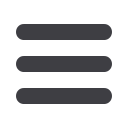
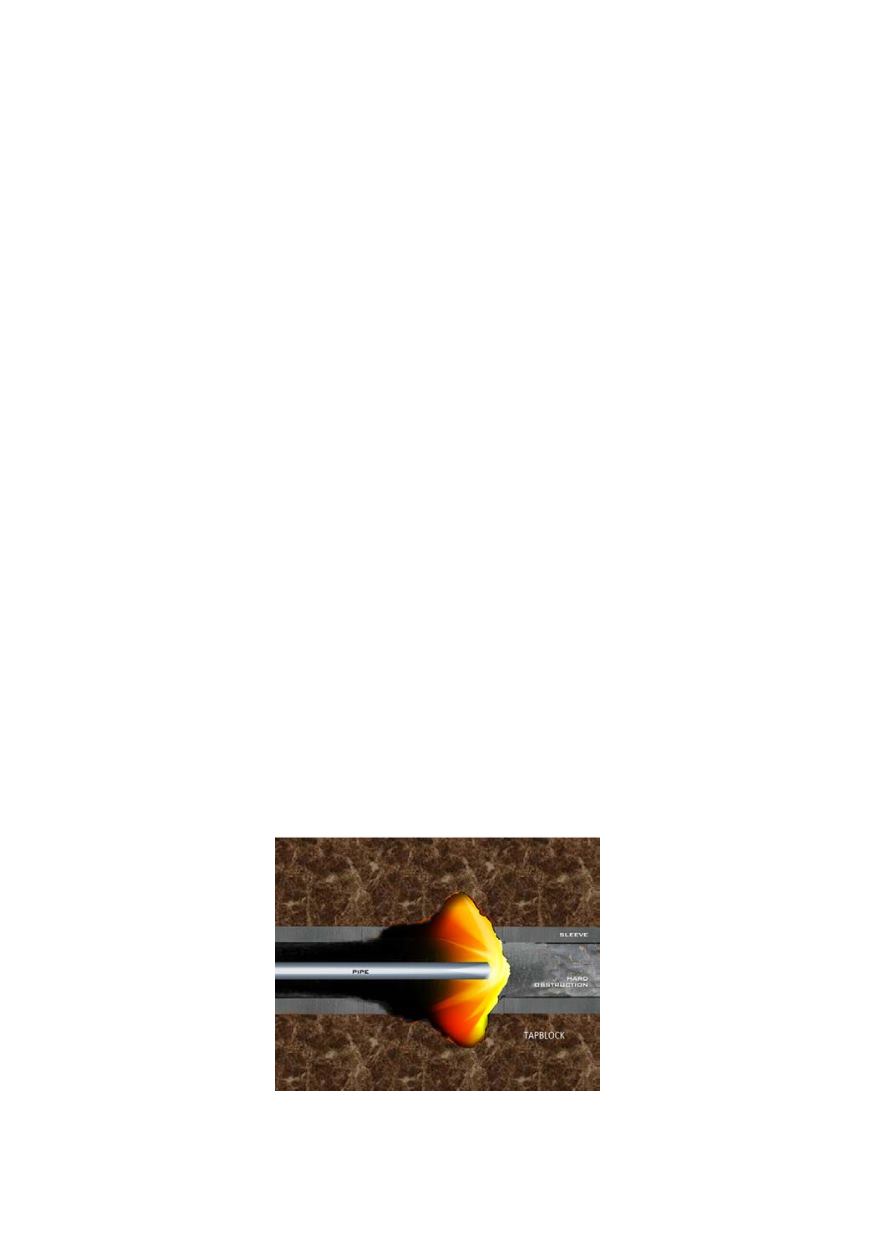
The company has developed a perfect balance between speed and the available mass
for the combustion process, creating the right exothermic reaction for each furnace
taphole demand.
These advanced oxygen lances offer an almost perfect combustion, resulting in an
operation with minimum emissions of fugitive gaseous and pollutants. In addition, it
completes the operation in less time than what is required by a standard lance.
Therefore, it emits much less fugitive gases during operation. The reduced number of
lances required, lower oxygen consumption and no left-overs (thanks to the special
lance-to-lance quick connector system EasyClick™) are some of the benefits taphole
operators enjoy using these new lances.
Increased accuracy and speed
These new lances are very accurate tools that enable the operator to perform a more
controlled operation; resulting in longer taphole life, fewer repairs and less down-time
Moreover, a lower projection of particles reduces the wear of PPE (personal
protective equipment.) Increased safety is also an important consideration. Trefimet
lances generate a more efficient and accurate energy which does not require pressing
the lance against the target; it lowers the projection of incandescent particles and gas
generation, giving greater control over the operation. The reduced operation time
required decreases the time of exposure for the operator at high temperatures. Less
stress, heat and sparks, coupled with greater cutting control, improve operations
safety, cutting accuracy and working conditions.
The Trefimet SuperOxibar, UltraOxibar and the TR models were developed specially
for Si metal furnace tapping operations.
Benefits for silicon tapping operations
Most of the thermal energy flow, due to the modus operandi of a standard oxygen
steel pipe (it needs something in front on which to bounce the oxygen, and heat in
order to combust), takes a perpendicular direction from the pipe, breaking by fusion
everything within a radius of 5 or more times the diameter of the pipe. Figure 7,
shows the consequential damages that a standard pipe could cause to the tapping
channel refractories.
Figure 7.
Standard pipe in taphole
59