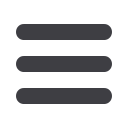
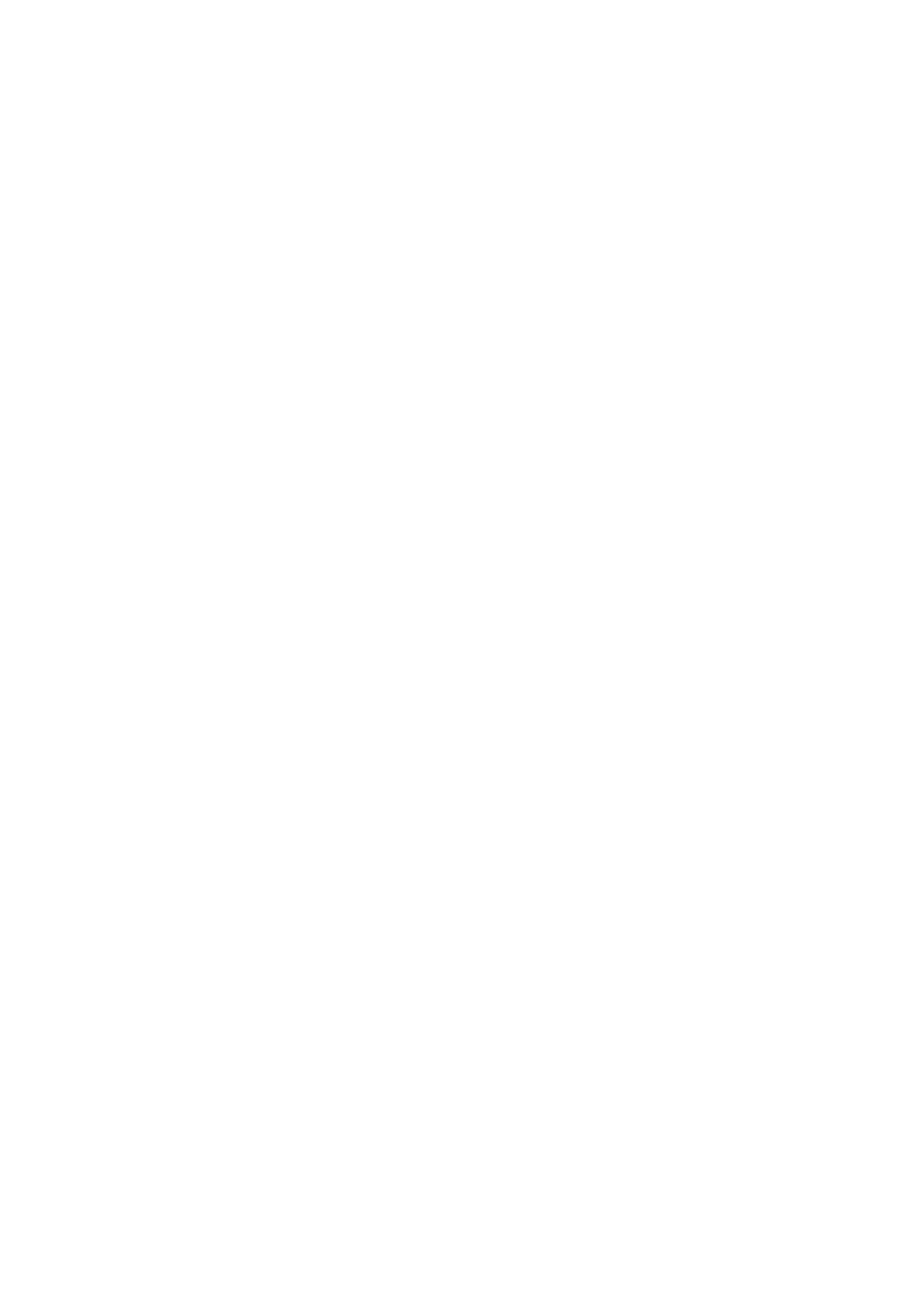
The distribution of intermetallic phases is influenced by the cooling rate and grain
size of the starting material [8].
The annealing after solidification can have effects on microstructure. Rong [3]
melted a silicon sample and solidified it at known cooling rate. A second sample was
melted and held at 1200°C for 12 hours. Only the intermetallic particles were still in
liquid state at this temperature, whereas the silicon matrix was solid. The shapes of
the intermetallic phases changed and the grain size was not affected. In the starting
sample the inclusions are found as elongated bands on the grain boundary. After
annealing they appear as round particles. It seems that the elongated particles have
split due to a decrease in surface energy. The temperature required to get an annealing
effect is estimated to be above the melting point of the intermetallics, between 900°C
and 1200°C.
Iron, aluminium, calcium and titanium are the most common impurities in MG
-
Si
and make up to 4% of the total weight percentage. High amounts of FeSi
2
are
expected to be found in MG
-
Si. The FeSi
2
-phase will have two different
microstructures according to the temperature of MG-Si. They are respectively called
high temperature FeSi
2
(HT-FeSi
2
or FeSi
2.3
) and low temperature FeSi
2
, (LT-FeSi
2
or
FeSi
2
). If the cooling rate to room temperature is fast enough, the HT
-
FeSi
2
structure
can be obtained at low temperatures. The cooling rate is fast enough in industrial
solidification to avoid a complete transition from HT to LT-structure. It has been
shown by a previous work that this transformation takes 3 hours at 700°C in order to
be complete [9]. Besides, Anglezio et al. [10] have reported that the HT
-
FeSi
2
is
stabilized by aluminium substitution in the lattice. According to Margaria [11] the
maximum content of Al can be up to 8% at. in order to improve the stability in a
efficient way. Boomgard
[12], Tveit [13] and Bjorndal [14] state that the
transformation occurs in two steps:
•
Step 1
:
HT-FeSi
2
ĺ
LT-FeSi
2
(Si)
: The transformation occurs with a change in
volume, and starts at defects such as cracks or grain boundaries. If these are not
present, the reaction will be hindered.
•
Step 2: LT-FeSi
2
(Si)
ĺ
LT-FeSi
2
(Si) + Si
: As soon as Step 1 has started, an
interface will begin to move through the material. Behind the interface there will
be a supersaturated LT-phase where silicon precipitates. As a matter of fact, the
HT-phase structure has a high vacancy concentration in the Fe lattice. Therefore
silicon precipitates can be noticed during this transition, especially at the grain
boundaries. The lattice increases its dimension. Stresses and cracks are therefore
generated because of silicon precipitation.
Margaria et al. [15] have analysed the variation in relative amounts of intermetallic
phases after annealing at different temperatures. They identified the compounds by X-
ray analysis and Scanning Electron Microscopy. Five annealings were performed at
five different temperatures. It was noticed that the amount of quaternary phase
Al
6
CaFe
4
Si
8
increased while the amounts of CaAl
2
Si
2
and FeSi
2
decreased. The peak
of this transformation is reached at about 925°C. An equilibrium reaction was written
to explain this phenomenon. The reaction between intermetallic compounds could be
a possible mechanism, but it was not proved in that work.
84