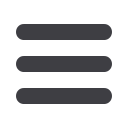
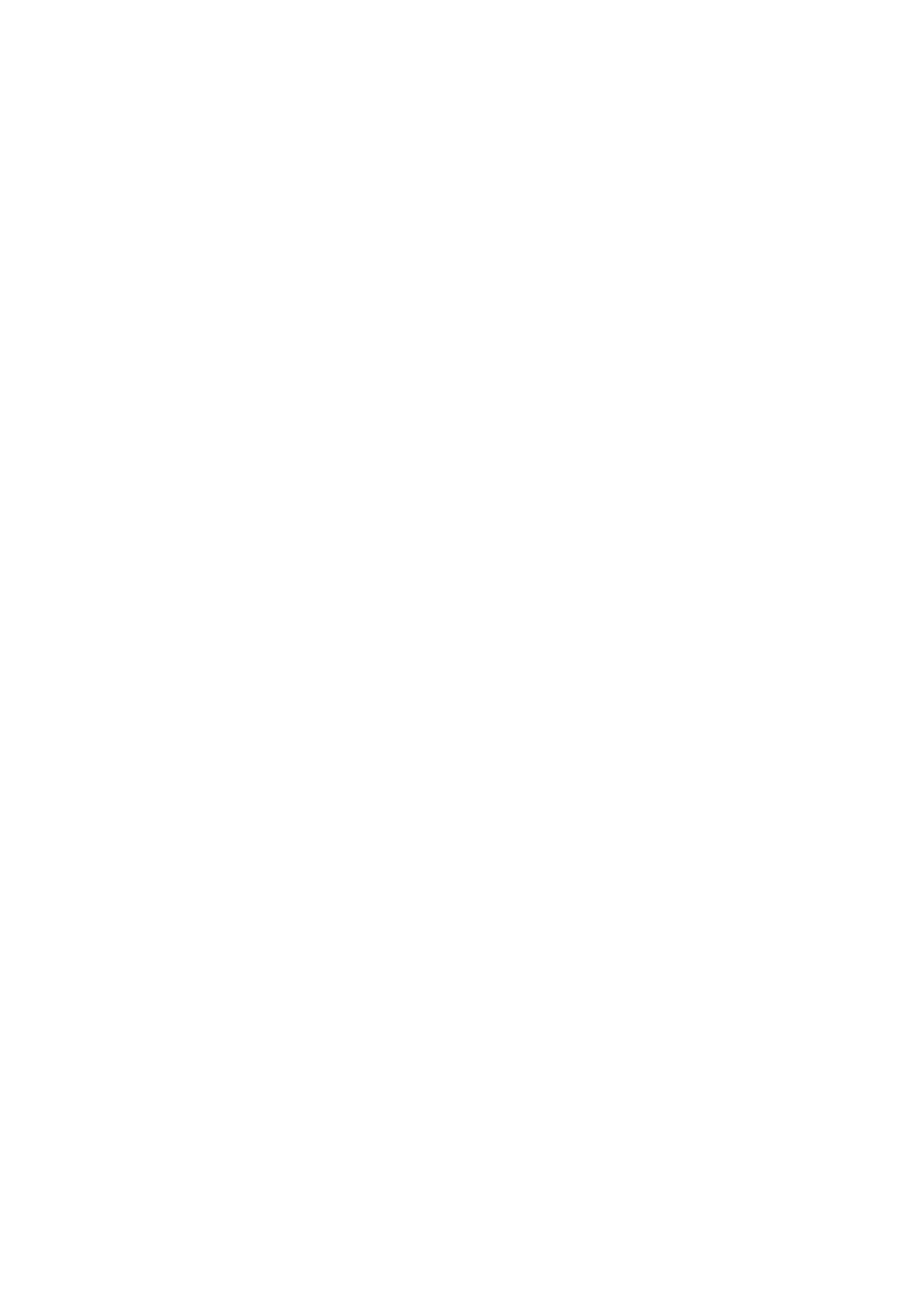
selectivity (ratio of dichlorodimethylsilane over total chlorosilanes) and reactivity
(quantity of chlorosilane produced per hour and kg of Si) of the chlorosilane synthesis
in the fluidized bed reactor.
Iron, aluminium, calcium and titanium are usually the main elements in metallurgical
grade silicon. Other elements are referred to as trace elements. Previous studies have
provided a description of the intermetallic phases found in MG-Si material produced
with standard process route [1, 2, 3, 4, 5]. The main intermetallic phases are FeSi2,
Al3FeSi2, FeSi2Ti, Al2CaSi2, Al6CaFe4Si8, CaSi2, Al6Fe4Si6 and TiSi2. Some
studies have been carried out to assess the effect of composition and cooling rate on the
type and amount of particles.
Nevertheless, this empirical knowledge has not yet been fully systematized into an
efficient and practical tool. The purpose of this paper is to present such a tool under
development by SINTEF in collaboration with Elkem. The model is currently based on
gathered literature data covering the major binary and ternary systems. The main
challenge is in integrating it into a predictive microstructure model covering a large
range of compositions and various solidification conditions. This paper will describe
the microstructure model, its calibration and a simple application to illustrate the
potential use in industrial product/process design. Please note that unless otherwise
stated all alloy composition are given in wt%.
Microstructure model
The microstructure model, hereafter referred to as Sistruc, has been initially developed
in 2009 by A.L. Dons following a similar approach as for the Alstruc model [6]. The
main objective of this tool is to be predictive, fast and user-friendly which implies that
one has to balance complexity with some simplifications and approximations. In the
following sections, we will present the main aspects of the current version. One
essential aspect of the current model is that it solves equilibrium phase formation during
solidification. At any step during solidification, the solid-liquid interface is assumed to
be at equilibrium and the phases form accordingly. Possible solid state phase
transformations are not accounted for in the model.
Model equations
Two main values have to be computed by the model to determine the phase formation
path: i) the concentration dependence of the liquidus temperature and ii) the solubility
of the different phases. In addition, for some particles, the model also computes the
particle composition based on the current liquid composition. The generic formula to
compute the liquidus temperature is given by:
ܶ
ൌ ͳͶͳͶ
ߙ
ܥ
ଷ
ୀଵ
ߚ
ܥ
ܥ
ஷ
( 1 )
where
i
denotes the solute element (Al, Ca, Fe, Ti, B and P are considered in the model)
and C the concentration in the liquid,
ߙ
are the coefficients of the third order polynomials.
76