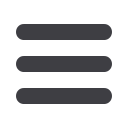
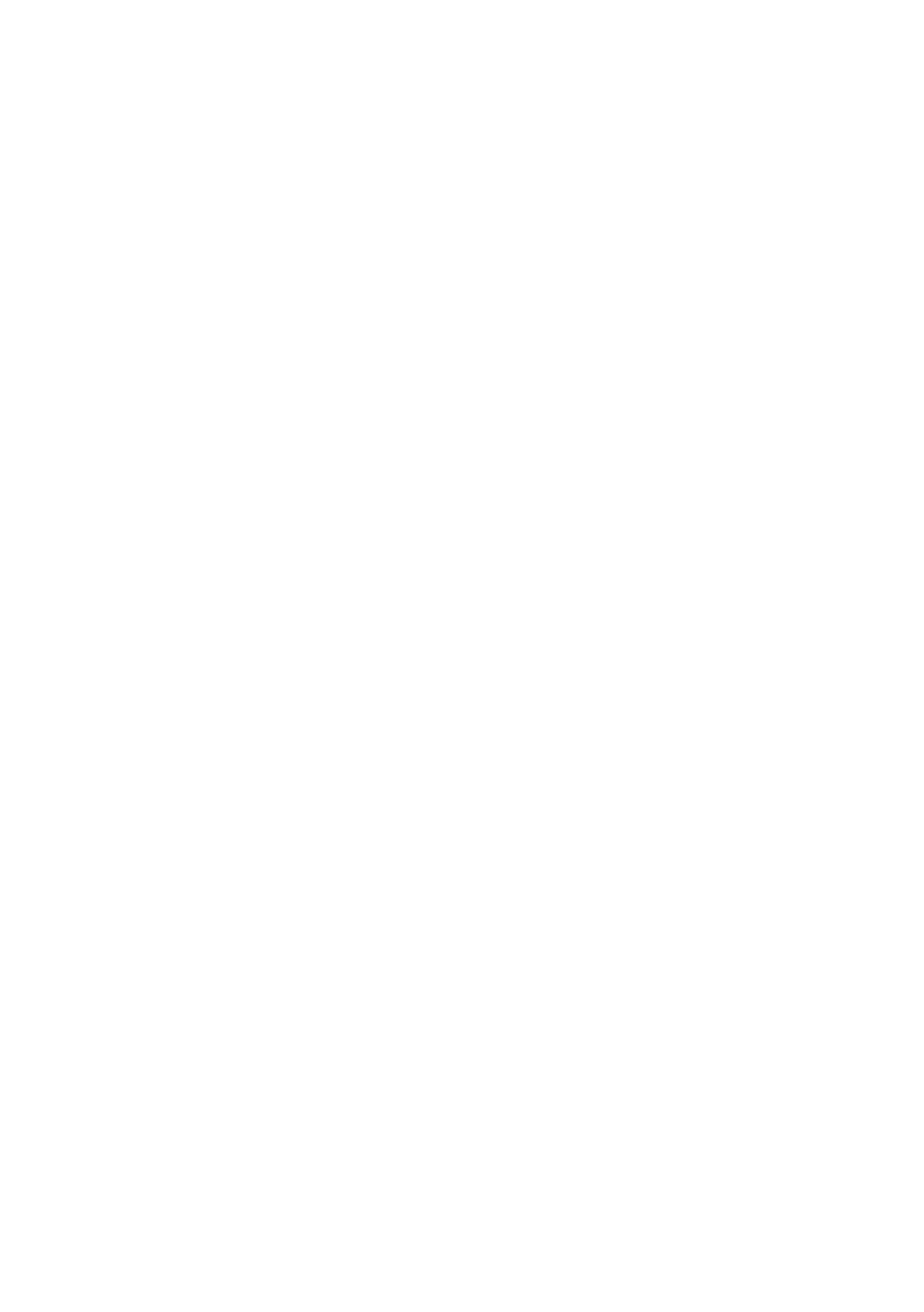
Silicon for the Chemical and Solar Industry XIII
Kristiansand, Norway, June 13 – 16, 2016
Identification and root cause analysis of micro-cracks in a
trichlorosilane reactor
Sean Gaal
1)
, Bill Larson
2)
, John Herman
1)
, Eric Davis
1)
1) Dow Corning Corporation, Midland, MI, USA
2) Hemlock Semi Conductor, Hemlock, MI, USA
Abstract
During a routine inspection cracking was identified in a carbon steel trichlorosilane
fluid bed reactor in the weld heat affected zone under a lifting lug. Further
investigation using wet fluorescent magnetic particle inspection revealed more
extensive cracking. A root cause analysis was performed which identified the
mechanism as chloride salt induced stress corrosion cracking. Methods are identified
to mitigate the risk.
Introduction
Stress corrosion cracking (SCC) of metals is a form of environmental cracking in
which cracks form in the simultaneous presence of a tensile stress (as an applied stress
due to live loading or as a residual stress from fabrication) and a corrosive
environment. A unique characteristic of SCC is that the metal dissolution component
of the corrosion reaction is essentially localised to the site and interior of the cracks,
generally this is the primary factor in determining the rate of propagation. This type of
localisation is atypical, it is only found in certain combinations of metals and
corrosive environments. In corrosion engineering, this has led to the compilation of
SCC susceptibility for a given metal by associating it with specific corrosive agents or
environments.
Identification
Trichlorosilane reactors are routinely inspected, as part of the maintenance schedule.
To accomplish this, they are first emptied and then washed out with water,
hydrolysing any residual chlorides. During a routine visual inspection some small
cracks were observed on the inside of the reactor, corresponding to the location of a
lifting lug which had been welded to the vessel exterior. To better characterise the
cracks the inside of the reactor was sand blasted and the cracks were imaged using
wet fluorescent magnetic particle (WFMP) analysis (Figure 1). It was quickly
discovered that the cracks were significantly more extensive than initially realised,
located under the lifting lug near the man way and in several areas of the knuckle
radius.
171