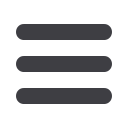
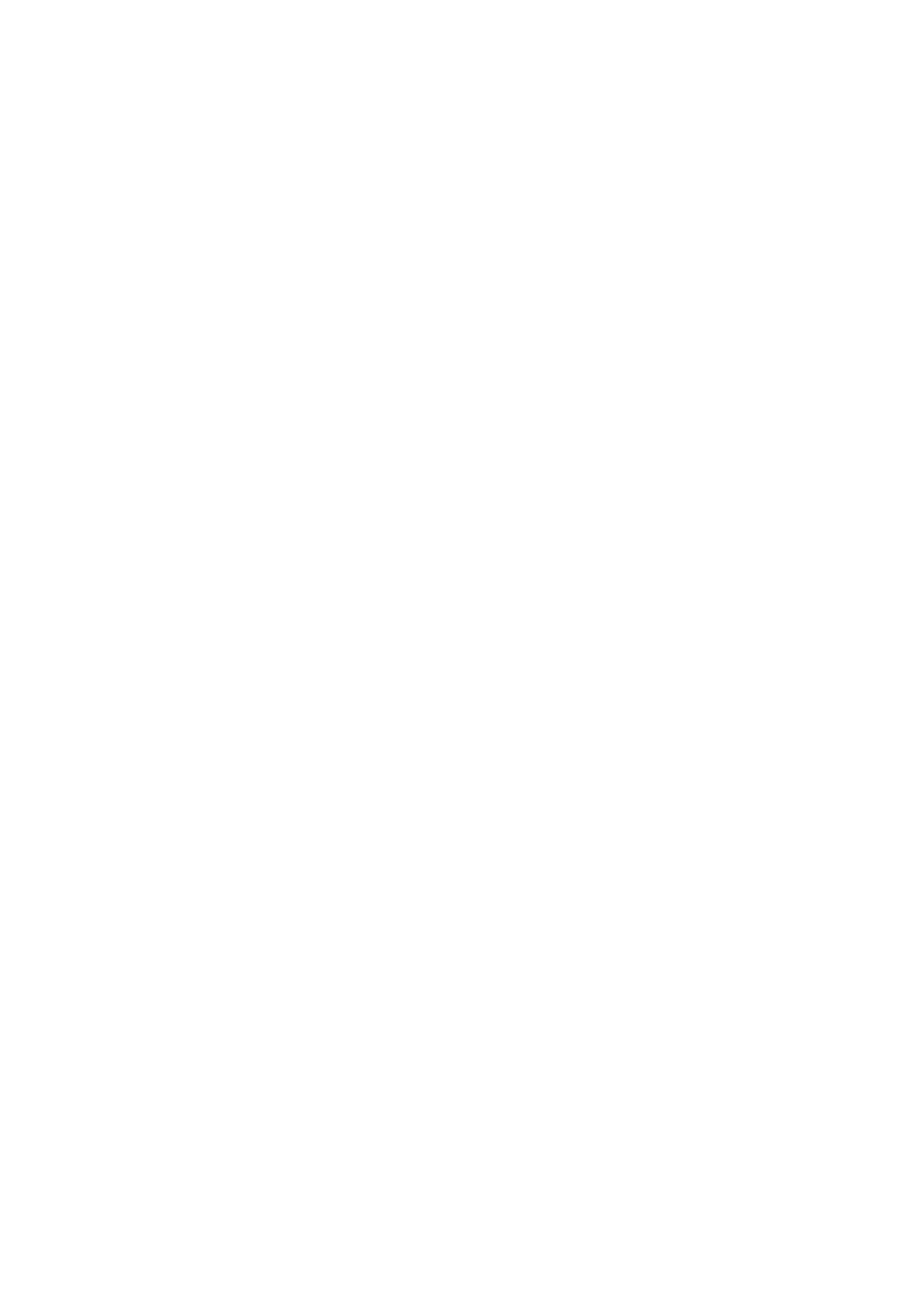
barking, chipping and drying energy; the pyrolysis energy requirement, and output and
distribution of by-products (condensate). Downstream, furnace operation affects the
flow rate, temperature, and composition of the off-gas. The off-gas heat recovery and
re–integration to wood drying and pyrolysis introduce some feedback, and thus an
implicit problem formulation. The combustible gas and liquid by-products from the
pyrolysis introduce possibilities for either export of condensate (as a bio-oil), or
extended electrical energy recovery through gas turbine/motor combustion, additional
steam cycle, or a combined cycle (CC).
This publication represents the first step towards a much larger case study were
experimental results are integrated through mathematical models in a system model
describing the entire silicon process. Consequently, several aspects remains to be
investigated, for example; how will an integrated charcoal production affect the transfer
of unwanted elements such as Na, P and B to the final silicon and micro silica products.
How will process economy be influenced by fluctuations in prices for raw material and
new products. The authors are well aware of these challenges but also recognize that
this initial study shows some very promising results.
Conclusions
Under the pyrolysis conditions and experimental setup used in this study a significant
amount (more than 50%) of the original chemical energy in the biomass feedstock can
be recovered as condensate/bio-oil. At these conditions a charcoal with a fixed carbon
content of roughly 80 % can be produced and 25 % on mass basis of the original dry
wood log can be turned into charcoal. In the continuation of this work the economic
viability of the integrated process together with other configurations will be
investigated to determine an optimum integration in terms of energy and mass together
with an evaluation of upgrading strategies and market and technological maturity for
high value products from the bio-oil.
7