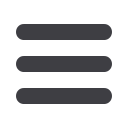
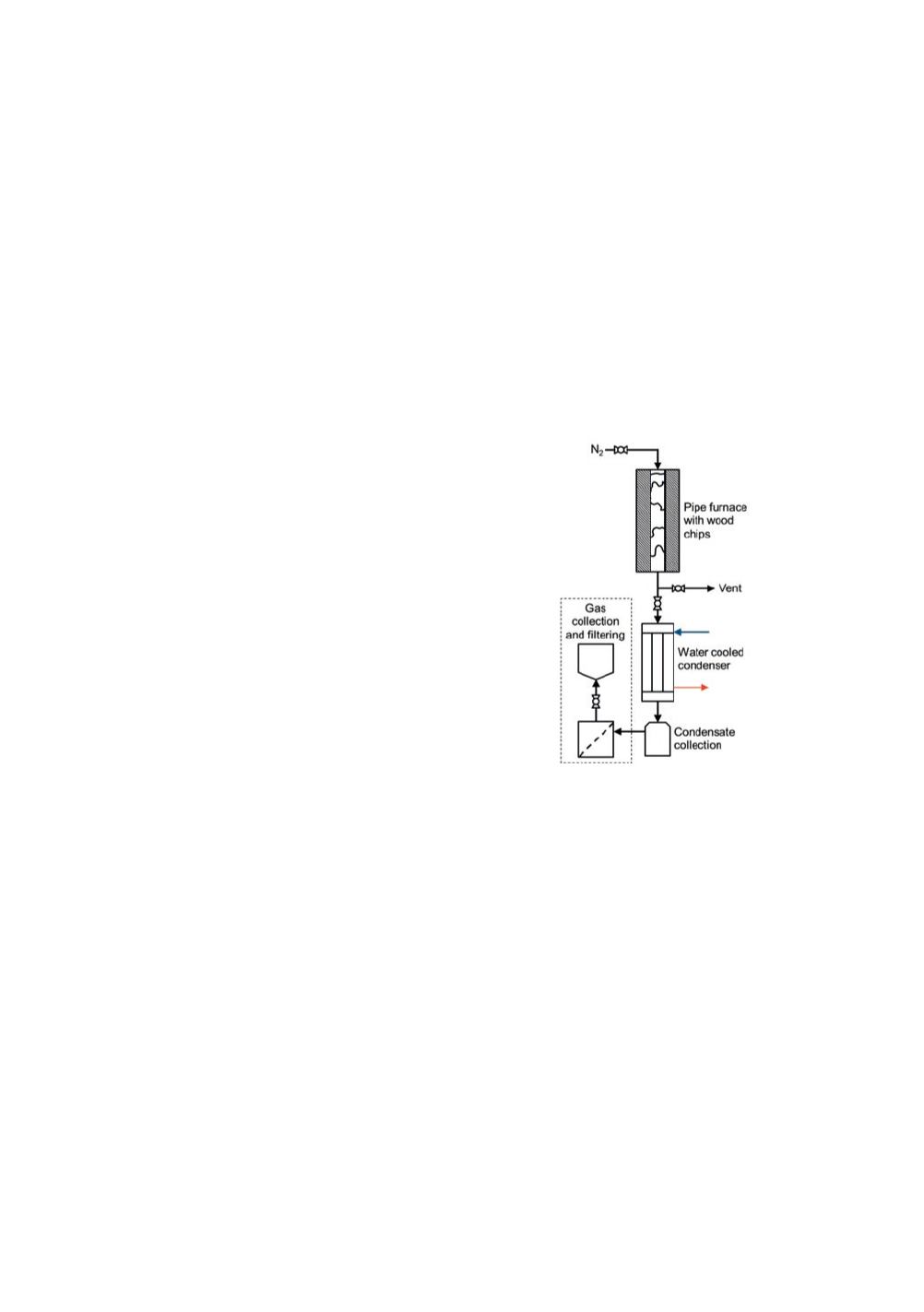
to be energy efficient. Here, integration refers to both energy integration and mass
integration. Energy integration can be to use heat from the silicon process and auxiliary
equipment as a source of energy for charcoal production (and vice versa). Mass
integration denotes recovering gas, fines, and condensate from the pyrolysis process
and integrating them into either energy production units such as boilers or gas turbines,
upgrading units or recovery units.
Taking this into consideration, the main objective with this paper is to perform a
detailed characterization of the main products from pyrolysis at conditions relevant for
a future Elkem process. The goal is that these and similar results can be used to conduct
a system study of the complete process; where charcoal production is integrated into
the silicon production process.
Method
Small scale pyrolysis experiments were performed in
order to obtain a complete mass and chemical energy
balance including the elemental balance for a feedstock
relevant to the CNMP concept. Pine wood chips were
selected as a reference feedstock since it is currently
used in the existing silicon production process.
Although the main product of interest is the charcoal,
there may be economical incentives to optimize the
recovery of condensates. Hence the experimental setup
was designed to maximize the recovery (but not the
production) of condensate. The experimental setup is
schematically described in Figure 1, and consists of the
following parts. A 40 mm pipe furnace approximately
500 mm long, a propylene-glycol cooled condenser
operating at a set temperature of 0
Σ
C, a glass wool filter
designed to trap aerosols and a Tedlar bag for gas
collection. The experiment was started by filling the
inner pipe of the pipe furnace with wood chips and the
pipe was then weighed and installed in the furnace. The
biomass was then dried at 120
Σ
C using a nitrogen purge
of 5 l/min for about 60 minutes. During the drying process the condenser was by-passed
and the steam was vented directly to the fume hood. After the drying process, the
nitrogen and vent valves were closed and the valves to the condenser and gas bag were
opened. Thereafter, the sample was heated with a heating rate of roughly 13 °C/min to
400-600
Σ
C depending on which final temperature was investigated. After the
maximum temperature was obtained the samples was kept there for 30-180 minutes
depending on the chosen soak time. Consequently, during the pyrolysis experiment no
purge gas was used and the pressure in the system was in practice "regulated" with the
expansion of the Tedlar bag (i.e. atmospheric conditions). After the required soak time
had been obtained the valve to the condenser and gas bag was closed, the furnace
switched off and the samples were allowed to cool overnight with a small N
2
purge to
prevent the charcoal samples from catching fire. Once the furnace had cooled off, the
gas and condensate collection systems and the amount of charcoal were weighed and
the yield was determined. The feedstock and products, condensate and charcoal, were
analysed to determine the elemental composition and the heating value. The collected
gas was analysed using a Varian CP-4900 micro-GC. Finally, a complete mass and
Figure 1.
Schematics of the
experimental setup
3