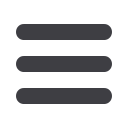
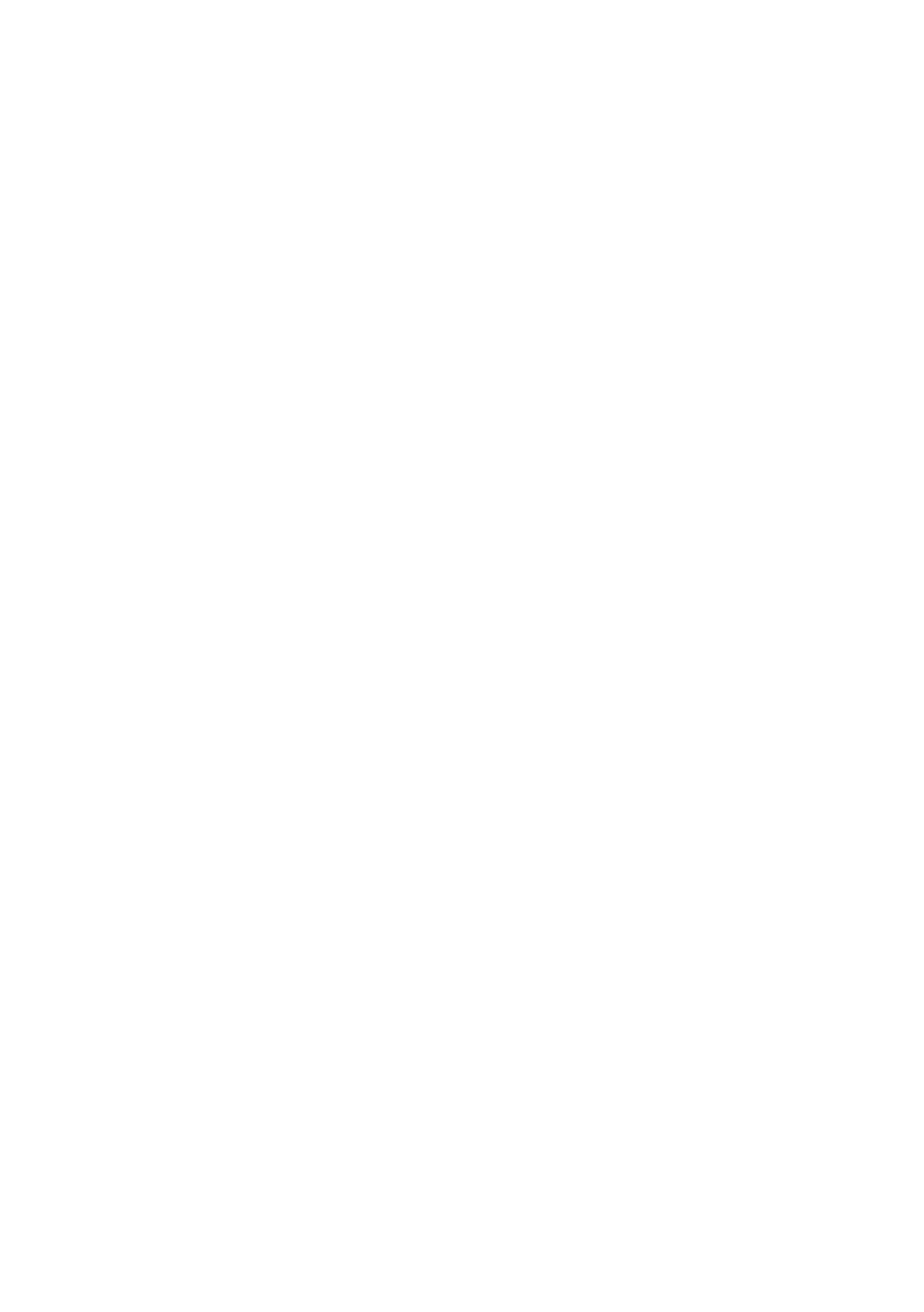
Silicon for the Chemical and Solar Industry XIII
Kristiansand, Norway, June 13 - 16, 2016
Metallurgically purified silicon for photovoltaics –
current development routes at Silicor Materials
M. Heuer
1)
*, M. Kaes
1)
, T. Bartel
1)
, A. Turenne
2)
, T. Jester
2)
1)
Calisolar GmbH, Magnusstrasse 11, 12489 Berlin, Germany
2)
Silicor Materials, Inc., P.O. Box 610220, San Jose, CA 95161, USA
*E-mail:
Matthias.Heuer@silicormaterials.comIntroduction
The most common feedstock material for photovoltaics is polysilicon produced by
Chemical Vapor Deposition (CVD) of silanes via the classical Siemens technology and
similar processes. An alternative route of producing solar grade silicon is the purification
of raw silicon using metallurgical processes without converting it into silanes. The
general challenge of the metallurgical route to Solar Grade (SoG) silicon is to establish
an impurity control along the metallurgical processes and to ensure a silicon product ready
to be used in photovoltaic applications.
At Silicor Materials this is achieved using enhanced segregation during a solvent growth
of silicon from a Si-Al melt solution at temperatures significantly lower than the melting
point of Si [1].
The process can be described as a liquid to solid refining process comprising a number of
refining steps, whereby, metallurgical grade silicon (MG-Si) with a purity level of 99.5%
Si is refined up to the levels needed for solar application. The four principal refining steps
are:
• Solvent Growth Refining – A molten, hypereutectic aluminum-silicon alloy is allowed
to cool, leading to a growth of a network of pure silicon crystals, from which the
remaining liquid eutectic can be decanted.
• Wet-Chemical Aluminum Removal – The remaining eutectic on the silicon crystals
is dissolved in hydrochloric acid forming poly aluminum chloride (PAC).
• Directional Solidification – Clean silicon crystals are re-melted and directionally
solidified resulting in fully refined silicon ingots.
• Final Preparation – Purified silicon ingots are cleaned, cut, chunked and blended to
eliminate residual chemical variation.
In addition to the primary output of SoG-Si, the process route has two by-products of
added commercial value, i.e. an Al-Si master alloy for use in the aluminum casting
industry and poly aluminum chloride, used as a coagulant for waste-water treatment
applications.
Silicor’s purification process has the advantage that the solvent growth refining takes care
of all impurities except aluminum and can be carried out at relatively low temperatures
in simple equipment that is well established in the metallurgical industry.
Naturally, the final removal of aluminum is most essential and takes place in a directional
solidification which is assisted by a pure liquid glass-flux on top of the melt [2].
Accordingly the research and development at Silicor Materials is focused on further
improvements of the solvent growth refinement and the final removal of Al.
9