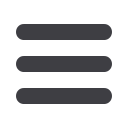
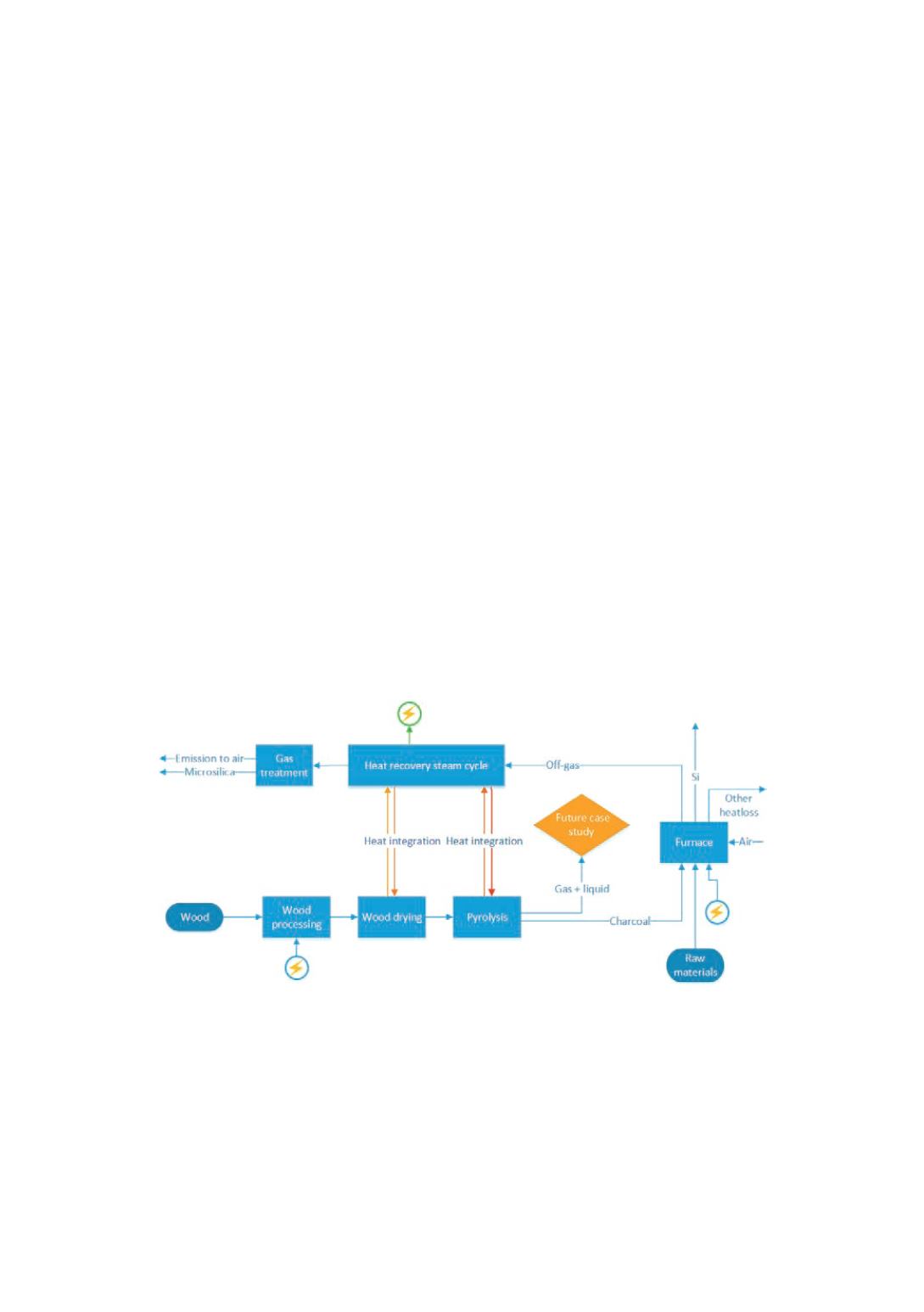
Upgrading of condensate
Applying the fast pyrolysis process, the bio-oil liquid product, depending on the quality,
can be sold and applied as a burner fuel directly. The process is well demonstrated and
several stakeholders exist globally [13]. Standards for bio-oil burner fuel exist as well,
even though bio-oil is currently not a well-established market product. Standardization
for other purposes is ongoing [14]. Catalytic bio-oil upgrading processes have not yet
been sufficiently demonstrated, and their technology readiness level (TRL) is low. The
catalysts used are mainly commercial refinery catalysts; new catalyst development is
ongoing at research stage. The commercial catalysts as well as the process itself are
facing several critical bottlenecks that are hindering successful demonstration and
commercialization. The short catalyst lifetime and the occurring deactivating/poisoning
mechanisms are the main challenges. The catalyst deactivation is caused by the coke
formation on the catalyst surface, temporarily blocking the active sites, while mineral
deposition can irreversibly deactivate the active sites (poisoning). Although the
catalytic pyrolysis oil upgrading processes are not commercial and critical challenges
remain, there are considerable efforts made towards demonstration. The efforts made
in the catalytic upgrading processes are expected to increase, hence the TRL, mainly
due to several reasons: (i) current techno-economic calculations show great viability
potential of liquefaction processes (pyrolysis and hydrothermal liquefaction) in
production of biofuels and (ii) finding new ways to utilize existing oil refineries,
infrastructure and know-how will be essential.
System perspective
There are several possible configurations for an integrated charcoal-silicon process and
the one showed in Figure 2 is just given as an example, different configurations will be
investigated in future case studies. However, already at this stage some aspects and
consequences of an integrated process can be discussed.
Figure 2.
Simplified block flow diagram of a potential CNMP concept.
From a given biomass specification and operation parameters such as temperature and
residence time, the pyrolysis unit/carbonizer will require different heat demand, which
will influence output flow rates, composition/element balance, and energy content of
charcoal, gases, and condensate. In addition, the integrated process is strongly governed
by specified furnace operation. Upstream; the furnace load and composition of raw
materials determine the necessary charcoal feed, which again affects pyrolysis load and
required wood input, as well as several related processing stages; wood input, de-
6