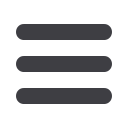
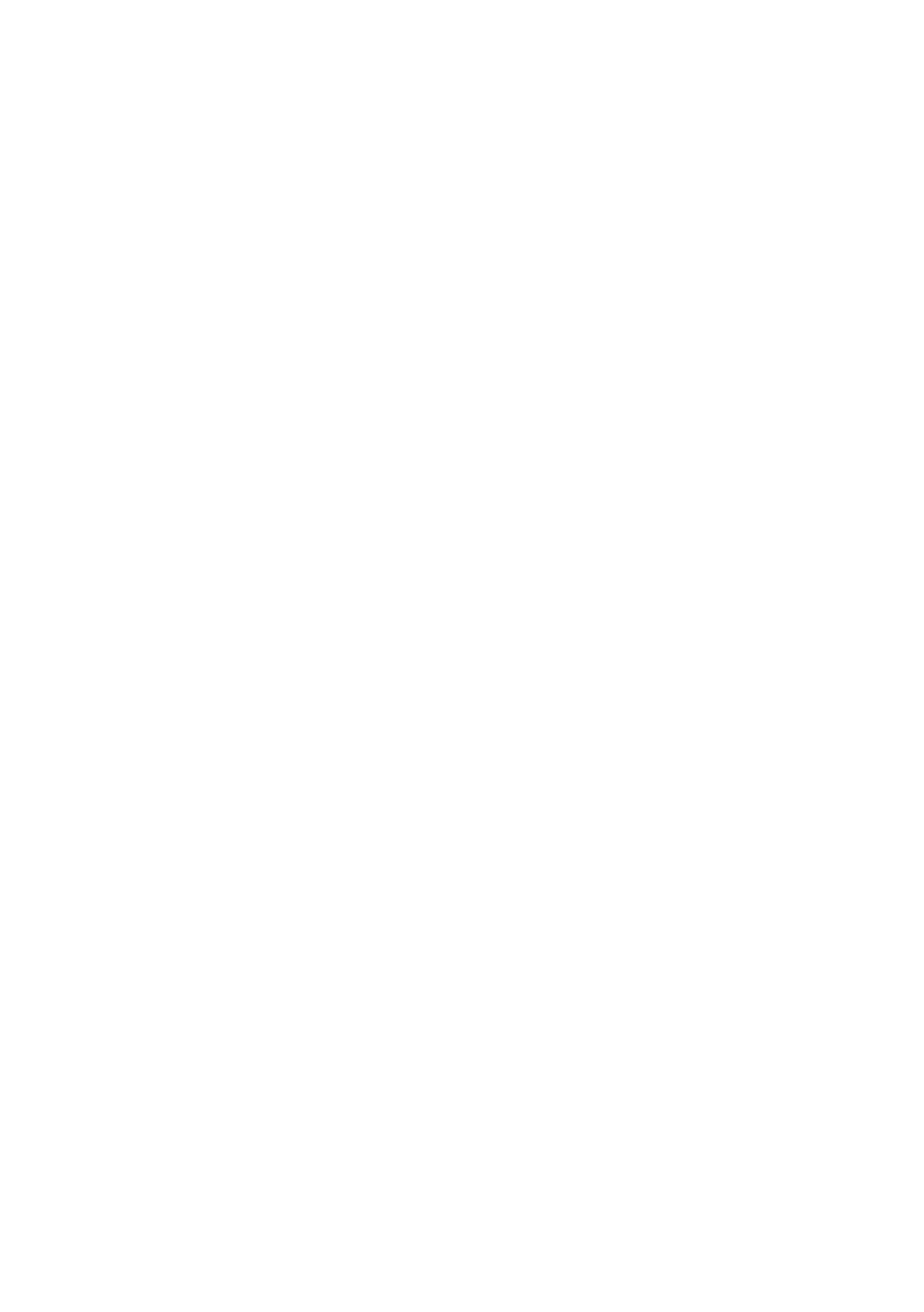
Introduction
Increasing global consumption and the threat of anthropogenic climate change put
pressure on the global society to increase resource efficiency and reduce CO
2
emissions.
Current production of primary silicon and ferrosilicon alloys are characterized by high
energy requirements and significant emission of climate gases. Elkem consumes
roughly 12 TWh of energy (electricity and carbon based reductants combined) and
emits an estimated 1.3 MT of CO
2
annually. In an effort to dramatically improve on
these numbers, Elkem has proclaimed its ambitions to develop a novel silicon and
ferrosilicon production process with the prospect of major reductions in overall energy
consumption and close to zero CO
2
emissions from fossil carbon sources.
The novelty of the process lies in the direct integration between the silicon production
process and a charcoal production facility, thereby enabling an additional reduction in
energy consumption and CO
2
emissions. In combination with an energy recovery
facility, the energy recovery factor of the total system will far outweigh that of
conventional silicon-furnace heat recovery systems. The integrated charcoal, metal and
energy recovery process has been termed
Carbon Neutral Metal Production
(CNMP
for short). The integration with charcoal production introduces by-products that are
novel to the conventional silicon production process; gases and condensate from
pyrolysis, bark, and fines from biomass and charcoal handling. Consequently, this
requires a new heat recovery system, boilers, handling, and more. There are also
uncertainties coupled to the charcoal production, such as identifying process conditions
for charcoal production in order to fulfil satisfactory specifications, as well as
understanding how process conditions affect mass and energy distribution between the
two by-products (gas and condensate).
Charcoal production is a subject that has been studied for centuries or millennia and
several reviews are available on the topic [1-6]. The distinction between fast and slow
pyrolysis refers to the heating rate of the fuel. Slow pyrolysis, is typically conducted at
heating rates ranging from 1-5 °C/min, whilst during fast pyrolysis the heating rates are
in the 100-1000 °C/s range. The heating rate is the most important factor influencing
the yield of liquids; increased heating rate results in increased yield of liquids. The
upper liquid yield limit is around 75 % on mass basis [7]. In order to obtain such high
yields, a short vapour residence time (in the literature a vapour residence time of less
than 2 s seems to be the generally agreed upon number) is necessary since the pyrolysis
vapours react through secondary reactions and form gases and additional char through
polymerization. If charcoal is of interest, prolonging the vapour residence time has
showed to be positive in regards of charcoal yield since this promotes secondary, char
forming reactions. This can be accomplished by limiting the amount of purge gas or by
using large particles or thick beds thus introducing a mass transfer limitation from the
biomass to the gas phase. The coupling to soak time (hold time) at maximum process
temperature here becomes analogous; i.e. if the pyrolysis vapours are allowed to react
with the charcoal for longer period of time more will be converted through secondary
reaction to gas and additional charcoal [8, 9]. Fixed carbon content increases rapidly
and roughly linearly with pyrolysis temperature from 300 to 400 °C (fixed carbon
content 20-70 %) and then slows down reaching a maximum value at around 90 % at
800 °C [10] provided that sufficient residence time is given for the fuel particles.
In preceding work, it was identified early on that the carbonization technology needs to
be integrated with existing infrastructure used in the silicon production process in order
2