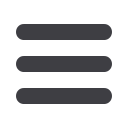
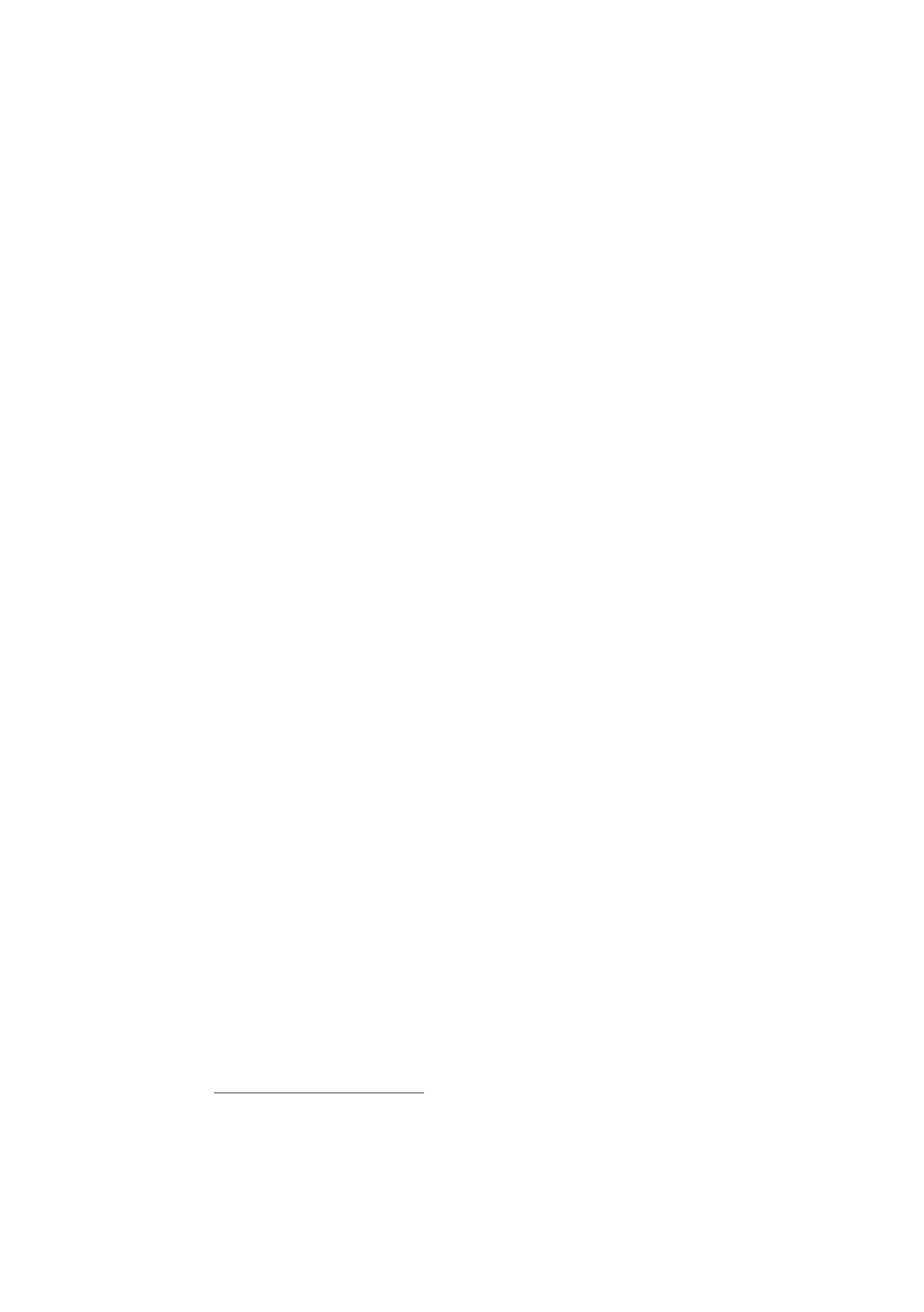
than 45 microns in size and cannot easily be used in the processes for which
the ground material is intended. Generally, the wastes vary from 5% - 10% of
the volume of material processed. In 2015, the volume of this wastes is
estimated to be 70 000 to 140 000 tons per year
3
. Fine grain silicon wastes are
replete with practical challenges relating not only to handling but also to
contamination and environmental impact. In standard casting of silicon metal,
slow cooling of the moulds create areas of macro and micro grain structures,
the latter containing high levels of metallic impurities which are prone to
fracture easiest during standard milling/grinding of silicon to small PSDs
(Particle Size Distribution). Standard customer specifications of silicon metal
for the polysilicon industry generally (with exceptions) require a lower limit of
approx. 45μm in diameter, below which the material is not conducive to
efficient fluidization in the TCS reactor. Some debate exists as to whether the
solution to improving the utilization of this material is equipment related, i.e.
re-designs of the specific reactors, or improved techniques in sizing of silicon.
In this case, the authors are convinced the solution is the latter due to lower
processing costs of resizing this material via atomization versus high capital
costs of equipment reconstruction or upgrades.
(ii) Kerf from LAS and FAS wafering processes
Silicon ingots made from high purity polysilicon are sliced into wafers and
generate a loss of silicon (“kerf”) equal to the thickness of the wire used in the
cutting process. This silicon, which is of equally high purity as polysilicon, is
mixed with the cutting fluid and remnants of the wire used, which usually is
coated with silicon carbide (LAS based) or Nickel (FAS based). The material
is very fine in nature and can reach sizes of less than 5 microns. The waste
from this process varies according to the thickness of the wire and other factors
but generally is estimated to be 40%-45% of the original polysilicon processed.
In 2015, the wastes from this source are estimated to be 150,000 tons.
In total, the waste generation of silicon from the PV and Chemical sector in 2015
exceeded 200 000 tons. This amount of wastes will only increase as the PV sector
grows.
Wasted energy
A real accounting of the cost of the wastes in question in terms of energy expended
is astounding, but this can be ignored because the energy spent to produce the primary
metallurgical silicon and polysilicon will be consumed with or without the wastes. A
more relevant perspective is the amount of potential energy lost from these wastes
because the silicon could not be transformed to a solar device that can generate
electricity.
The total lost potential solar energy from the aforementioned wastes can easily be
calculated by taking the total silicon and estimating the annual electricity output this
silicon would have generated had it been used to make solar devices. Assuming 150
3
Based on estimates of the total demand of metallurgical silicon required by the photovoltaic and chemical sectors
46