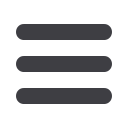
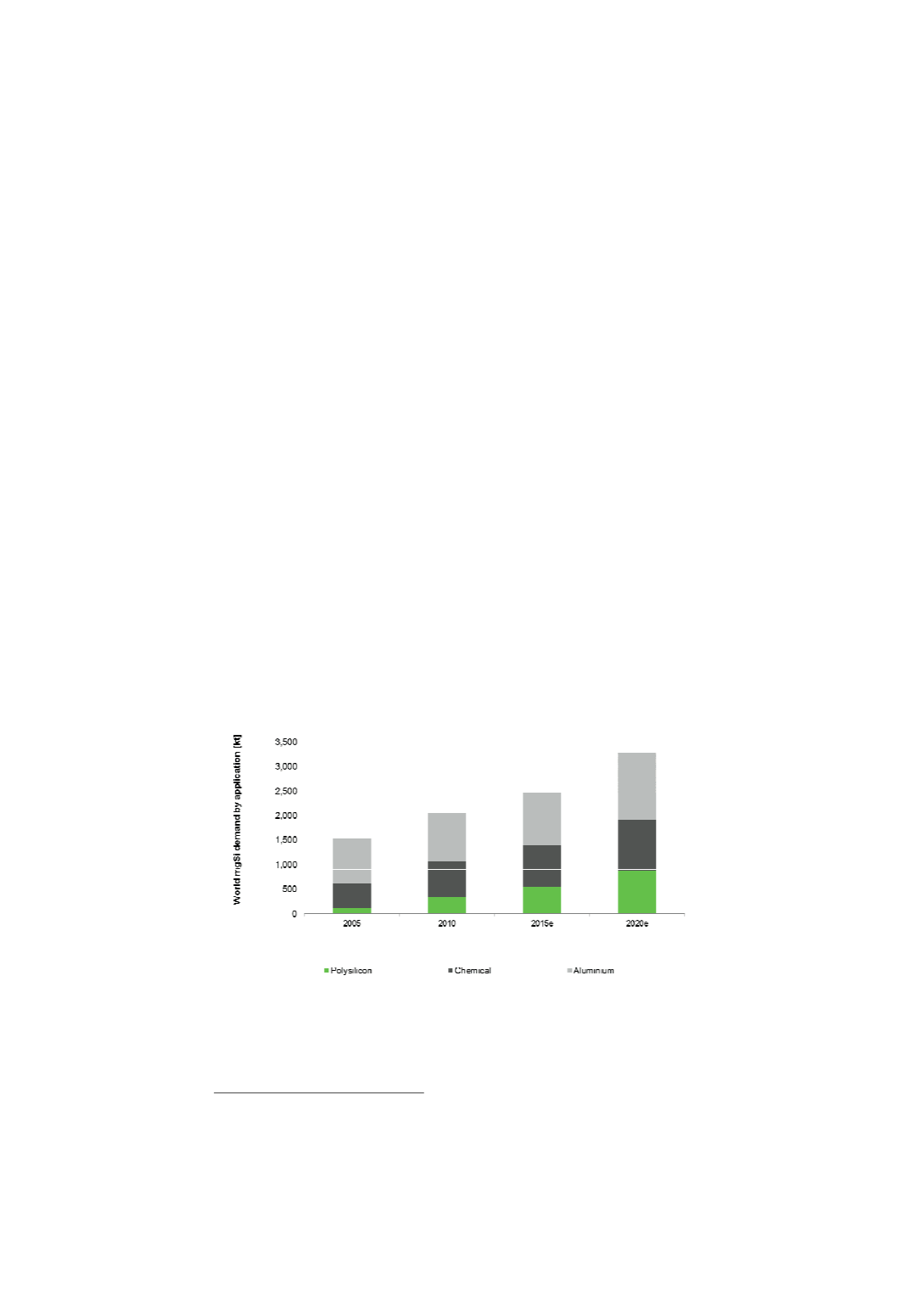
The resulting material is a customized silicon bead of average diameter 100 – 300
microns depending on customer requirements. The chemical purity of the material is
improved due to the standard refining technique applied in the melting step with
slagging and gas injection.
Depending on the mix of incoming raw materials, the resulting final product can be
tailored by increasing the mix of kerf (which has low metal content) and/or modifying
the refining steps. The integrated design of the factory allows for a small footprint and
can be implemented into existing industrial infrastructure.
Margin Improvements
Currently polysilicon producers are pushing cost reductions through economies of
scale, improved processes and upgrades or installation of new technologies. With global
top Tier 1 average cash costs for polysilicon being approximately $14.5/kg
6
, the overall
cost structure of polysilicon becomes increasingly dependent on metallurgical silicon.
Current metallurgical silicon prices are seeing a slump but generally are still on the rise
as average producer costs are rising.
Notwithstanding an intermediate drop in prices as new capacity comes on stream in
Iceland and other possible locations, the increase in demand for metallurgical Silicon,
even if only from the solar sector, will more than compensate for these incremental
capacity additions. A comparison of the evolution of the PV demand on metallurgical
silicon sheds light on the overall impact that this industry is having on the silicon
market.
Source: CRU,
Viridis.iQestimates
6
Viridis.iQinternal modelling
Figure 4 Growth of MG silicon segments
49