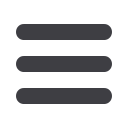
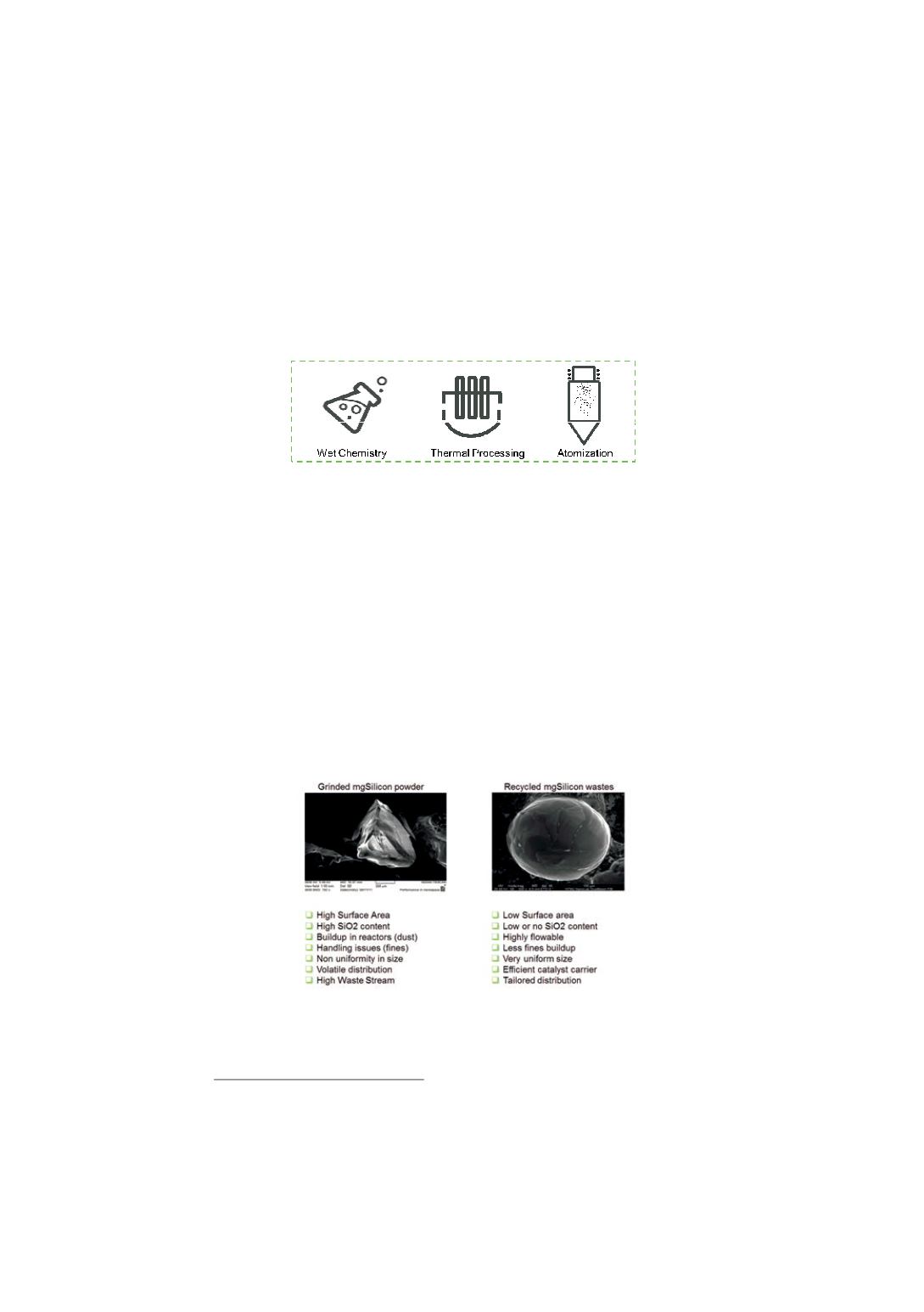
Technical Solution
The proposed technology concept utilizes in-house developed process steps along
with inert gas atomization technology.
The wet and thermal steps will not be disclosed herein but the atomization process
step brings distinct advantages including improved handling from uniform particle
shape and size; increased reaction rate due to evenly distributed intermetallic phases
formation of binary, ternary and even multicomponent silicides at the grain boundaries
(some beneficial to the MCS reaction).
Of the many benefits of atomized silicon to the polysilicon process
8
, one of the main
ones is the ability of doping the material with a selected catalyst that can aid in the
reaction kinetics of both the Direct Chlorination and Hydrochlorination processes. The
cooling rate of silicon, when atomized, is on the order of 10
5
– 10
6
K/second which
prohibits metallic impurities in the silicon from quickly segregating, as can easily
happen in traditional casting of silicon and slow cooling of ingots. Additionally, the
physically restricted shape of the particle creates barriers to segregation from one
particle to another. Rapid cooling of the silicon during atomization also creates surface
points on the particle at which the intermetallic phases are present. When low
temperature catalysts are used, these “last to freeze” elements tend to also be present on
the surface.
Figure 5 Comparison of grinded MG silicon versus recycling MG silicon wastes
8
Uniform size and shape, flowability, lower segregation of impurities, usage of fine grain feedstock, low
surface area, catalyst addition, etc.
51