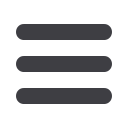
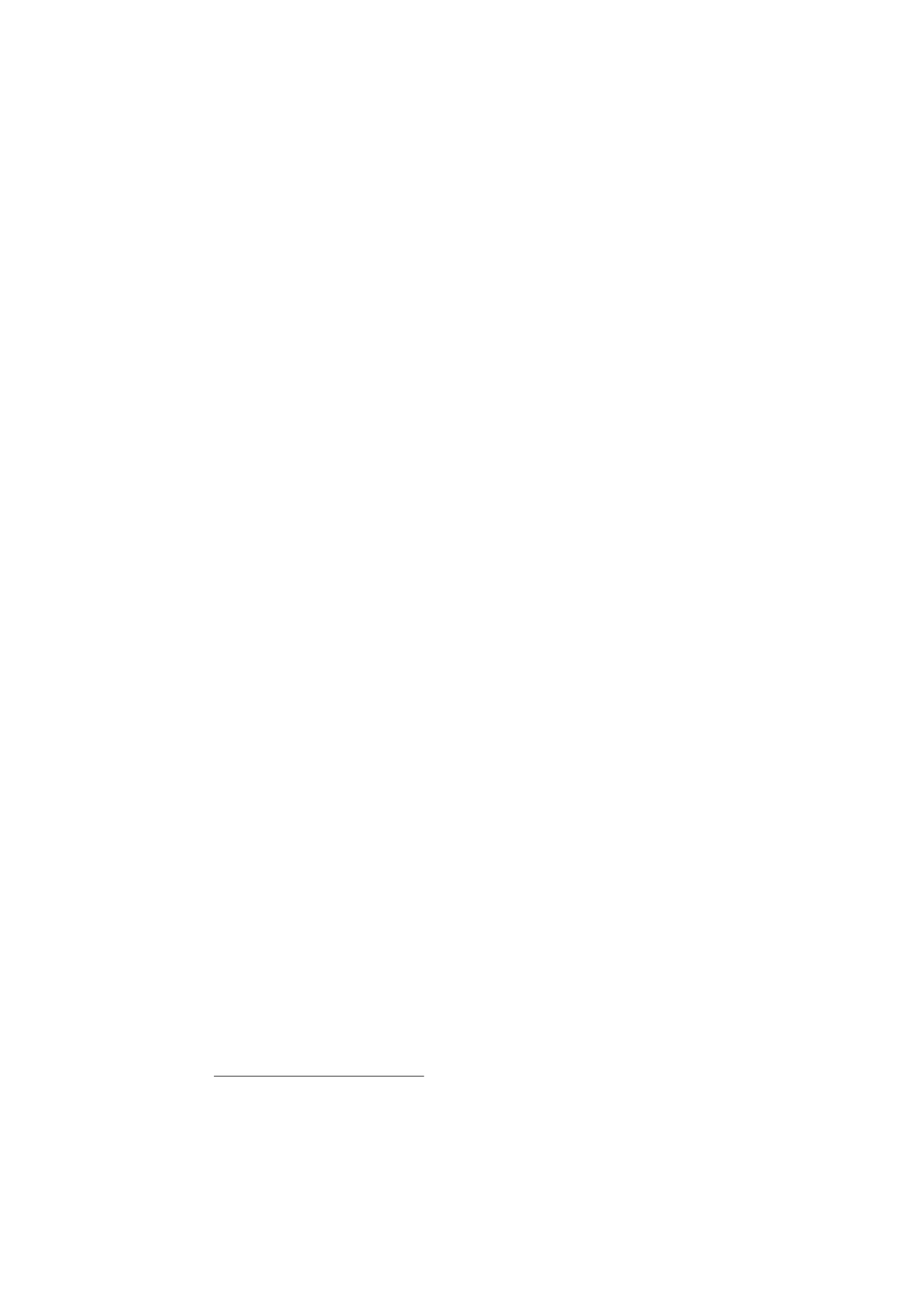
Silicon for the Chemical and Solar Industry XIII
Kristiansand, Norway, June 13 – 16, 2016
Recycling silicon from kerf and grinding processes -
the lost PV potential of silicon wastes
Dipl. Eng. Lou Parous
1
, Dr. Frank Weber
1
,
M.Sc. Eng. Valdiney
Domingos de Oliveira
1
, Dr. Wolfgang Herbst
1
.
Viridis.iQGmbH, Konstanz, Germany
1)
Viridis.iQGmbH - Von-Emmich-Str. 4, 78467 – Konstanz - Germany
Abstract
Every year the Photovoltaic sector expands as the cost benefits of solar are
disseminated worldwide with projections now for solar to reach the 100 GW per year
installed capacity in a very short time. With each GW of silicon based solar demand,
more and more metallurgical silicon is needed to support the polysilicon sector, which
is now on the verge of recovery after the last crisis in that industrial segment.
For all silicon based solar technologies, the processes required to provide polysilicon
for those technologies mandate the need for a ground metallurgical silicon powder as a
feedstock for this industrial segment. The silicones industry also requires the same
ground silicon, but the process of grinding silicon generates an off size material that
cannot be used by either industry. In fact, every year more than 100 000 tons of silicon
off spec waste is generated from this process that fall out of the value chain for which
they were originally produced.
Additionally, further down the process of making solar devices, the manufacturing
of solar wafers generates an additional more than 100 000 tons of silicon contaminated
with SiC from the FAS
1
and LAS
2
process steps that is not used to make solar energy.
The potential solar power from these wastes is forever lost and represents over 45 GW
annually given today’s PV market.
The authors are developing and planning a waste silicon recycling factory to convert
this waste from kerf and grinding processes back into the value chain as a feedstock for
polysilicon production, thereby reducing the lost potential of this waste and providing a
low cost feedstock for polysilicon producers. The authors are
currently developing a
factory project to capture the lost opportunity of waste silicon by combining proven
technology advancements in solid-liquid separation techniques with modern gas
atomization of silicon fines, resulting in chemically superior silicon with low impurities
and homogenous physical characteristics for polysilicon production and
Methylchorosilane production.
1
Fixed abrasive slurry
2
Loose abrasive slurry
43