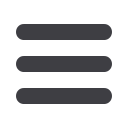
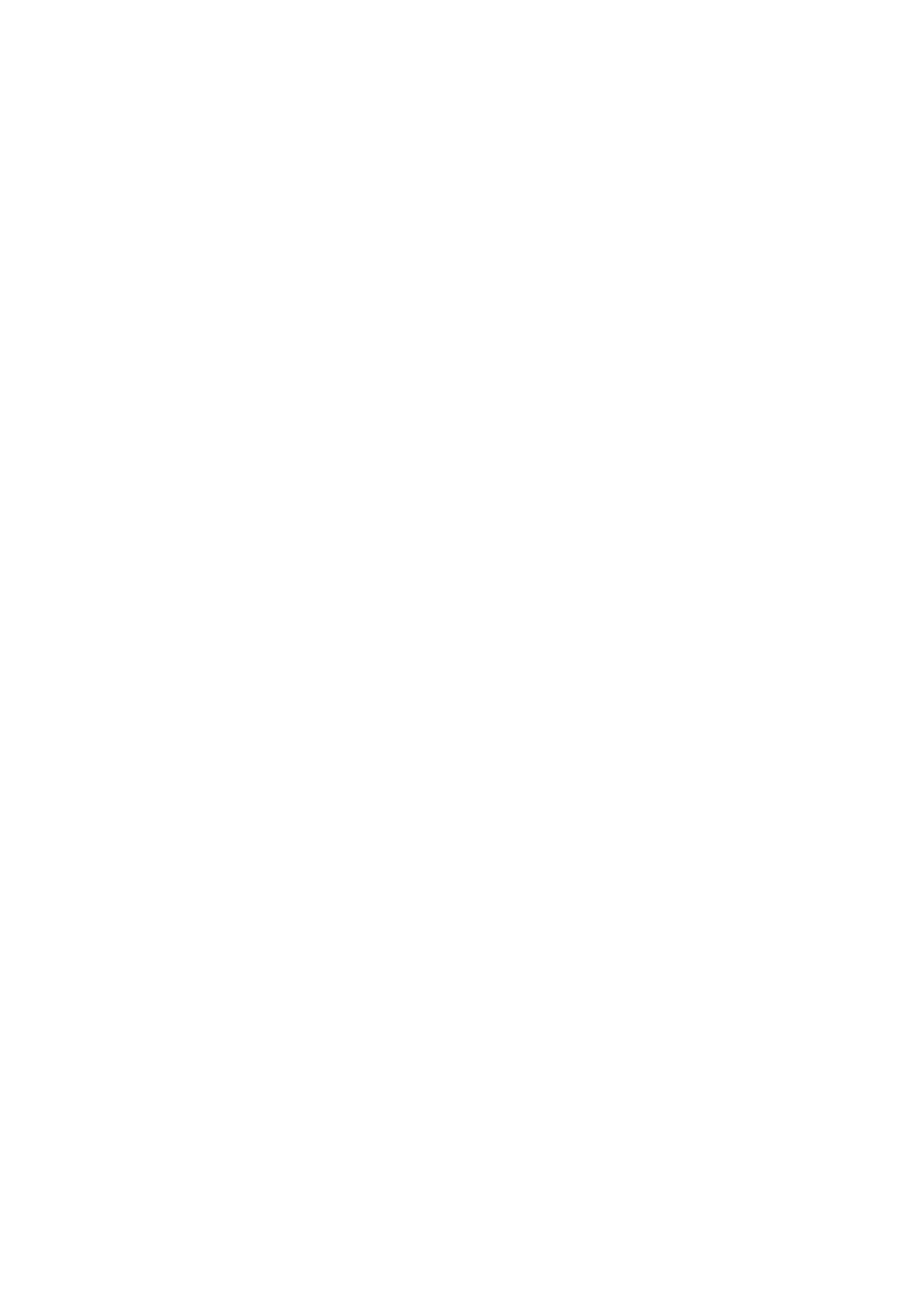
(i) Project RE-Si- CLE, “Recycling of Silicon Waste from PV Production Cycle”
(EU funded, 2002 to 2004): No industrial realization, difficulties related to
small SiC particles
(ii) Projekt „SICAREC“ (Deutsche Bundesstiftung Umwelt, 2009 bis 2013):
„Recyclingverfahren für Siliziumwafer-Sägeabfälle mit Wiederverwertung des
Siliziums in der Solarzellenfertigung“: No industrial realization.
(iii) J Air Waste Manag Assoc. 2013 May; 63(5):521-7. Tsai TH, Shih YP, Wu YF,
„Recycling silicon wire-saw slurries“: The separation of Si and SiC has been
found as a major challenge
(iv) Yen-Chih Lin, Teng-Yu Wang, Chung-Wen Lan, Clifford Y. Tai, „Recovery
of silicon powder from kerf loss slurry by centrifugation“, Powder Technology
200 (2010) 216–223: Centrifugation results up to around 91% at a yield of
74.1% have been seen as realistic, however not sufficient for industrial
implementation.
(v) Project SIKELOR „Silicon kerf loss recycling“ (EU funded, 2014 - 2016),
Garbo (IT), University of Greenwich (GB), University of Padua (IT), EAAT
(D), HZDR (Helmholtz- Zentrum Dresden-Rossendorf, D): currently running
research project, also targeting solar grade material
In conclusion, an industrial application of these approaches has not been reached so
far either a) due to the immense challenges of getting polysilicon purity levels and/or b)
due to the significantly fallen polysilicon prices.
The current approach of recycling wastes by
Viridis.iQGmbH does not follow the
same logic as those listed above. The idea of recycling wastes firstly has to take into
account that the wastes themselves are of lower purity and likely can only be reused at
places in the value chain where this purity is accepted by the process. In the current
case, the recycling of grinding and kerf wastes can only realistically be reused at the
beginning of the PV value chain where the strongest and most rigorous purification step
is used, i.e. the conversion of solid silicon to gaseous trichlorosilane or
Methylchorosilane and its subsequent distillation.
The recycling process planned by
Viridis.iQis based on a three step approach in
which the various waste sources are homogenized and treated with a wet chemical,
thermal and shaping step.
The wet chemical process step results in a dry powder that is then melted in a specially
designed melting furnace, from which the liquid silicon is then atomized in a modified
inert gas atomizer.
The input material to the process is micron size silicon waste from grinding
processes and dried kerf, containing silicon and silicon carbide which has already gone
through a separation process. The material is loaded into a specially designed thermal
treatment furnace for melting and then tapped into ladles for pouring into the atomizer.
48