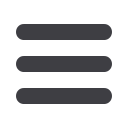
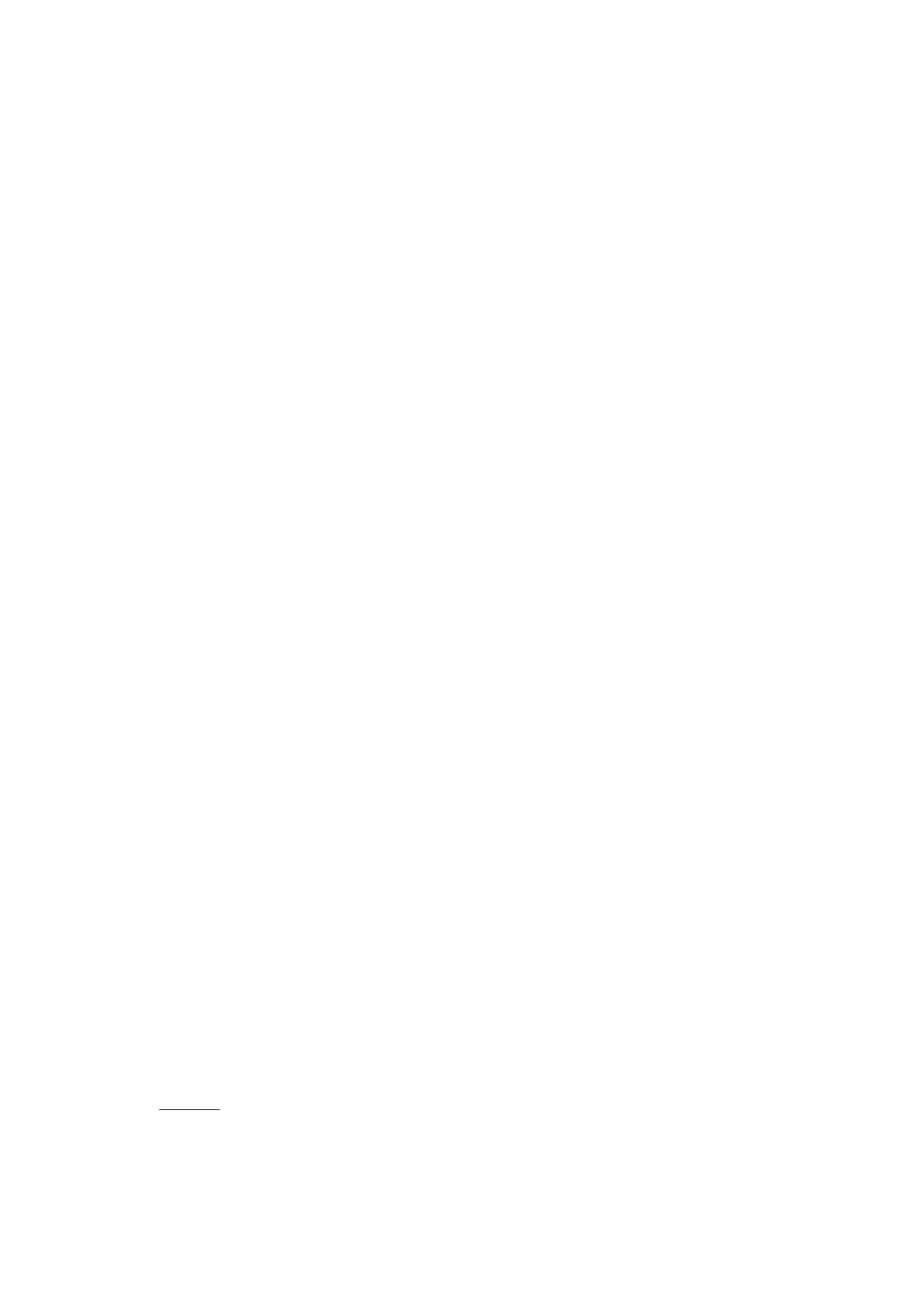
In the lower part of the furnace the electrical energy is provided through an arc. Here the Si
producing reaction are taking place, (1) as well as the SiO(g) forming reactions (2) and (3):
SiO(g) + SiC = 2Si + CO(g)
(1)
2SiO
2
+ SiC = 3SiO(g) + CO(g)
(2)
Si + SiO
2
= 2SiO(g)
(3)
In the cavity, there will hence be a mixture of SiO and CO gas in addition to other high
temperature gas species. The cavity is formed due to the condensate (Si, SiO
2
, SiC) sticking
the charge together, creating a void below as the raw materials are consumed. As the SiO
2
starts to melt, in the condensate and in the raw materials, the mechanical strength of the roof
top will decrease, and hence the roof top temperature is in the area of 1650-1800 ºC [2]. The
arc is not necessarily a single arc. It can be multiple arcs as well. The arc will mainly go
towards the Si bath or the SiC crust and as calculated, the arc could be maximum 10-15cm,
based on the electrical parameters. It hence shows that
Error! Reference source not found.
is an illustration, and not showing the accurate scale.
As the gas species are ascending into the charge at lower temperatures, the major part of SiO
gas will react. The gas can react on the surface of the raw materials according to reversing
reaction (2) and (3), producing a condensate of SiO
2
, Si and/or SiC, or with the carbon added
according to reaction (4).
SiO(g) + 2C = SiC + CO(g)
(4)
The back reaction of (2) and (3) and reaction (4) will of course be very important regarding
obtaining a high Si yield and low energy consumption. For FeSi process the reduction of iron
oxides to metallic iron takes place in the upper zone of furnace.
By the term “metallurgical excavation” it is hence defined as: using personal only dealing
with the metallurgy in the furnace, taking and analysing samples and reporting their findings.
Generally, the metallurgical excavations of industrial furnaces are commonly carried out in
addition to the rapid reconstruction of furnaces (Si furnace in Elkem Thamshavn, FeSi
furnace in Elkem Bjølvefossen, Wecker Si-furnace no.4). This meant that the excavation and
sampling was also done as fast as possible. Hence, the geometry of the zones in the furnace
was based on visual estimation from the outside of the furnace and samples were picked as
they were removed from the furnace. There are a number of actions that is traditionally taken
during shut down in the belief that it will ease the mechanical excavation-especially when fast
re-building is the priority. One is to move the electrodes in the manner of “pushing” the metal
and slag out as well as freeing the electrodes. Another is to melt the charge down before shut-
down, meaning stopping the charging some time before shutdown in the belief that less
material will be easier to remove. As excavations of industrial and pilot scale furnaces are
quite seldom and in addition have a high cost, there is not a multitude of reported information.
Though there have been some reports from industrial excavations, the descriptions of zones in
the furnace have not been focused to big extend. However, publication by Tranell et al. [2]
reported the various zones in a FeSi furnace and the summary of this work is used in this
paper. Tangstad et al. also distinguished and described several zones in Si furnace after the
excavation in Elkem Thamshavn [3]. Recent three metallurgical furnace excavations give the
possibility to compare obtained data with the data published previously. The geometry of the
zones in a Si furnace is dependent on the operation history, and hence it can be a number of
different geometries, sizes and composition of the various parts of the furnace.
The Furnaces, furnaces operation and shot-downs.
Finnfjord furnace no. 1 produced FeSi75 alloy was operated at 17.5 MW. The furnace is
about 5 m in inner diameter and 2.5m high and it was stopped with normal operation with the
electrodes down in operating position due to scheduled maintenance. After the furnace was
stopped the charge materials at the top were stoked to get even surface. The surface in the
34