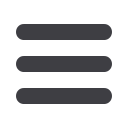
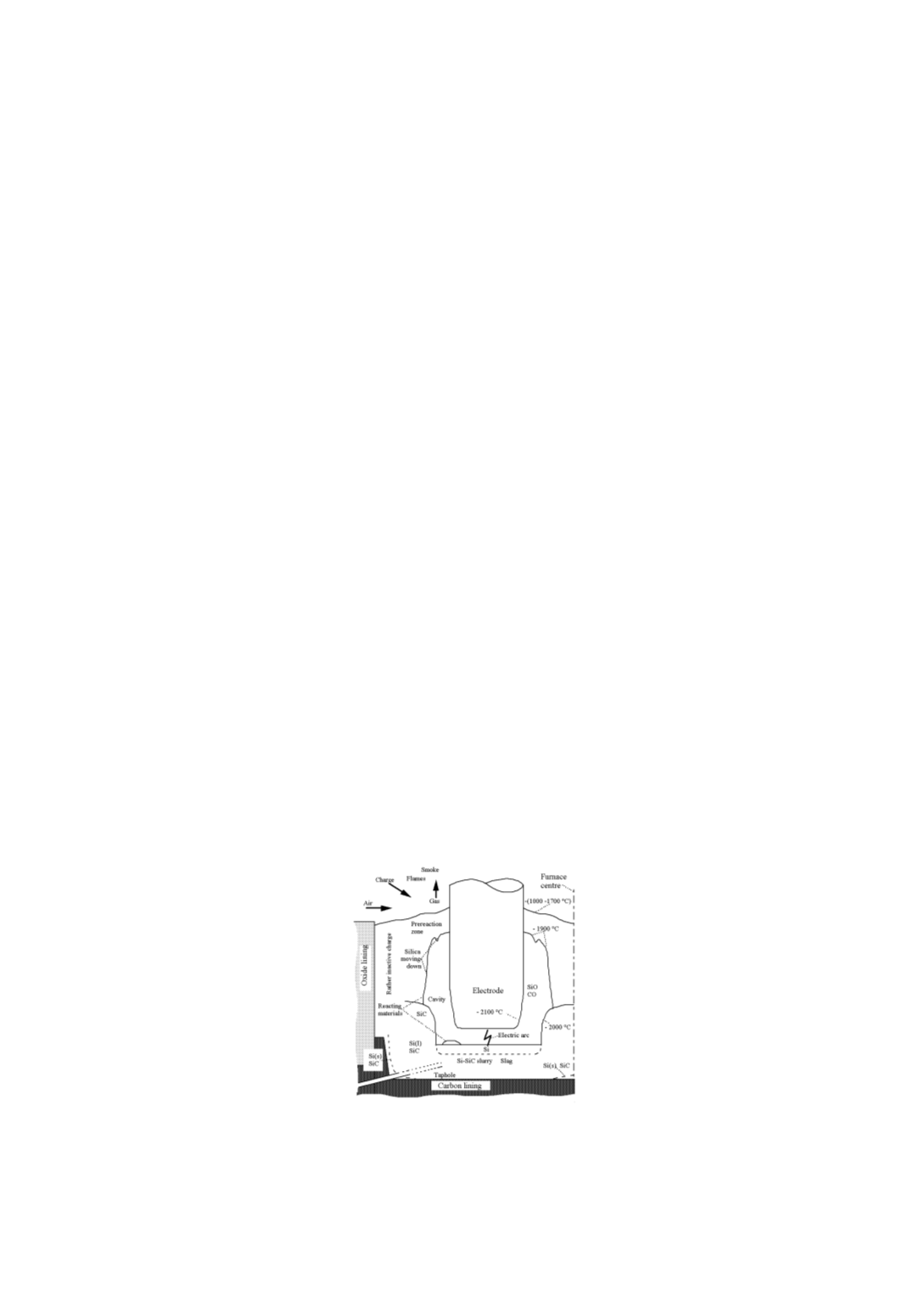
Silicon for the Chemical and Solar Industry XIII
Kristiansand, Norway, June 13 – 16, 2016
Five furnaces five different stories
M. Ksiazek
1
, M. Tangstad
2
, E. Ringdalen
1
1) SINTEF Material and Chemistry, Norway
2)
NTNU, Department of Material Science and Engineering, Trondheim, Norway
Abstract
Since 2008 five excavation of submerged arc furnaces (SAF) was carried out in
Norwegian ferroalloy industry. The paper presents comparison of observation and
data from excavations of two ferrosilicon furnaces and three silicon furnaces. In this
paper similar type of zones have been given the same terminology in order to compare
the different excavations, Some of the main differences between the different
excavations is the extent of slag in the furnaces as well as the extend of SiC crust. The
high temperature zone varies from cokebed to large cavities.
Introduction and background
In principle, the production process for high silicon ferrosilicon and silicon are very similar.
Both processes involve carbothermic reduction of SiO
2
in a submerged arc furnaces.
However, in the ferrosilicon process the iron ore or other source of iron is added. In the Si
production, quartz and carbon materials in the form of charcoal, coal and coke are added as
raw materials. Woodchips are added to increase the permeability of the charge as it descends
in the furnace. The Si-production process requires temperature above 1800 °C hence electrical
energy consumption in the order of 11-13 MWh per ton of produced metal [1]. The main
literature today, describing the Si process is the work by Schei [|1] where the interior of the
furnace is summarized in
Error! Reference source not found.
.
Figure 1
: Zone and interior of Si furnace [1].
33