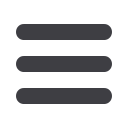
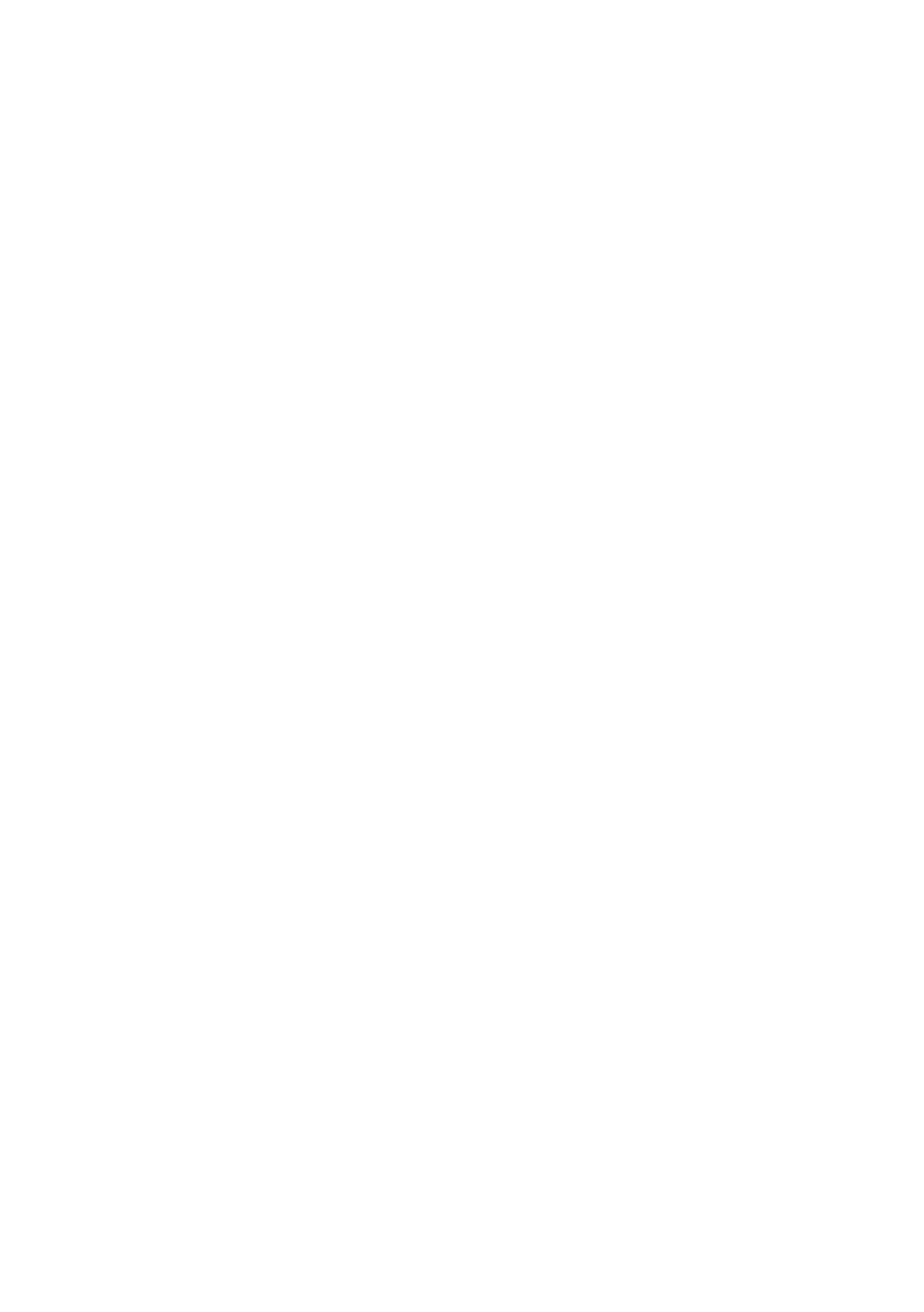
of information about interaction of CH
3
Cl (or methyl groups from other sources) with
these surfaces and subsequent reactions. However, it remains a challenge to connect
these results with the observations on actual direct process reaction mass, which is a
very complex solid mixture of silicon with Cu catalyst, several promoters, and more
than 10 metallic impurities.
1
The required information for making the connection
includes (a) which is the key active site causing the majority of methyl group
decomposition? And (b) how does that relate to the active site that catalyzes MCS
formation?
The first part of this manuscript surveys literature about side-reactions of methyl
groups and related by-products. The second part reports new methods for studying the
reaction of Si with CuCl, which is a key step for forming the active catalyst of the
direct process.
Methyl group decomposition in the direct process
During the direct process reaction, it is desirable to keep the per-pass conversion of
CH
3
Cl well below 100%. Excess CH
3
Cl improves the reaction rate of silicon. The un-
converted CH
3
Cl is separated from products and recycled back to the process.
1
Of all
methyl groups from the converted portion of CH
3
Cl, however, only part of them are
incorporated into MCS. The other methyl groups go through different side-reactions
and generate different by-products. For convenience, they are collectively termed as
“unproductive” methyl groups in this manuscript. Unproductive methyl groups reduce
material efficiency of the direct process. Some unproductive methyl groups go
through C-H bond cleavage (decomposition reaction) to generate coke and hydrogen
ligands incorporated into hydrogen (H
2
), hydrocarbons and MCS products with a Si-H
bond. These side-reactions and by-products, as well as possible reaction mechanisms,
are summarized below.
By-products associated with methyl group decomposition
Some unproductive methyl groups lose hydrogen atoms and become carbonaceous
residue (coke) deposits on the reaction mass. Coke formed in the direct process is not
purely carbon based. Coke with hydrogen-to-carbon molar ratio in the range of 0.5-
1.8 has been observed.
8
It was proposed that coke can catalyze formation of more
coke or even deactivate the direct process reaction.
8,9
Olakangil systematically studied
coke formation in the direct process.
10
The impurities present in chemical grade
silicon were found insignificant for coke formation. On the other hand, phosphorus, a
promoter used in the direct process, was found to suppress coke formation at higher
temperature and pressure. CO
2
profiles obtained from temperature programmed
oxidation (TPO) of coke deposition showed two major peaks, which were attributed
to coke formed near two different sites. The lower oxidation temperature peak was
attributed to coke formed near a site rich in copper and/or chlorine, while the higher
temperature one was attributed to coke formed near a site lean in copper and/or
chlorine. The assignment was based on observation that copper and chlorine catalyzed
oxidation of carbon black and reduced oxidation temperature. However, the
possibility of generating two forms of coke was not ruled out.
10
Based on kinetic
study, Olakangil proposed coke formation mechanism consists of reactions 1-6 (S as
an unoccupied active site consisting of Cu, Si or promoters). The proposed
mechanism include key assumptions such as (a) reaction 2 was a rate-determining-
step; and (b) reaction intermediates were adsorbed on reaction mass surface.
10
148