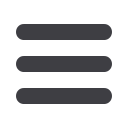
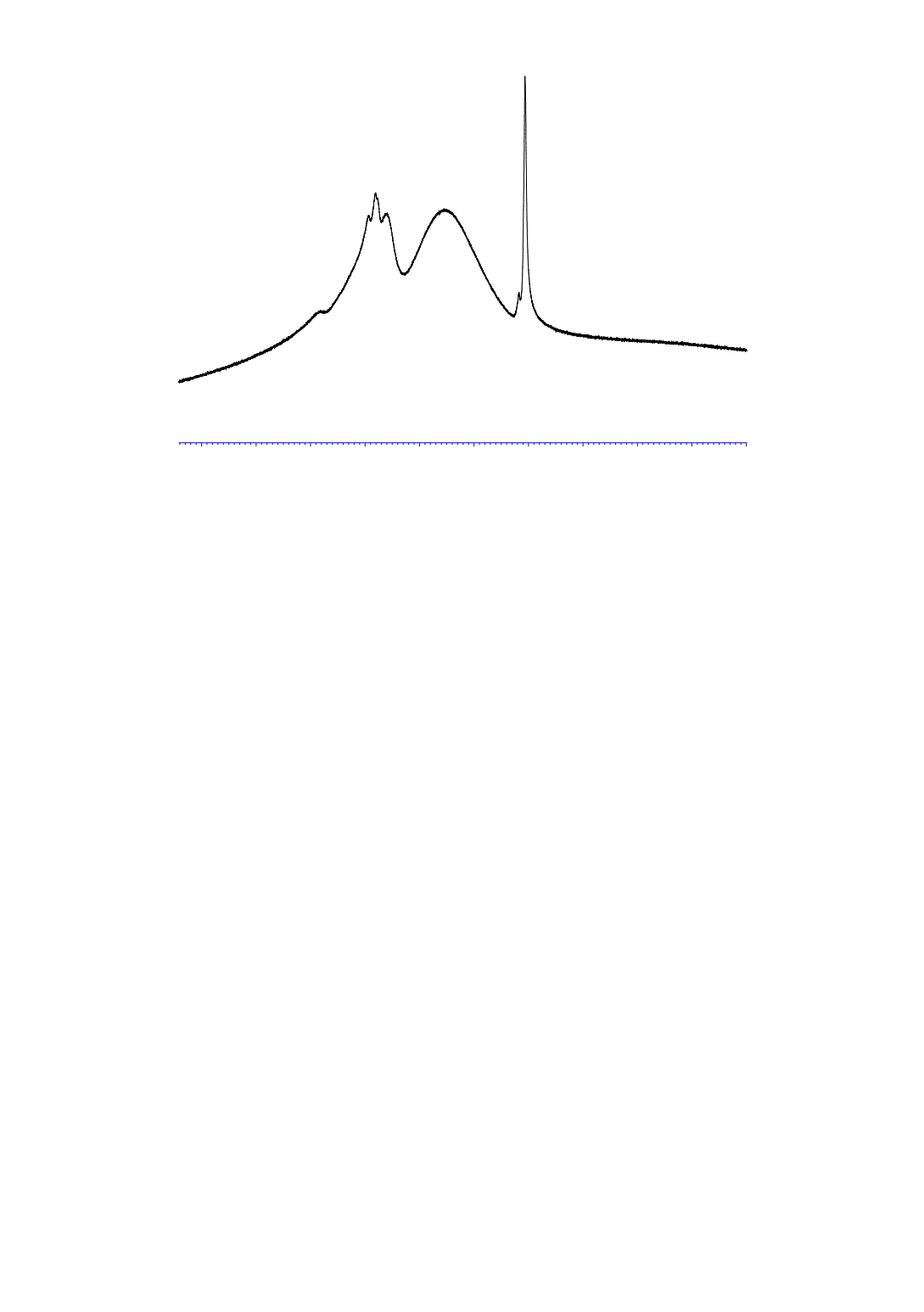
Figure 8:
27
Al-NMR of the high boilings discharged from the distillation process as
waste (Al concentration ~4500 ppm), broad hump from 20 – 120 ppm caused by probe
and cavity of the NMR spectrometer
Thus, the results of the NMR investigations strongly suggest that AlCl
3
is the main cause of the
precipitation of solids in the distillation process. It is present in the primary product of the direct
synthesis and is present in all stages of the distillation process. It therefore most likely is the
reactant to form several undesired products. The most problematic products are
tetrachloroaluminate salts which are scarcely soluble in silanes and in the high boiling residues
of the silane purification process. Together with carbon compounds they form solid precipitates
to be found in filters and on the walls of evaporator pipes.
After identification of the main cause for the precipitates there are several methods conceivable
to avoid processes leading to the formation of solids. The most obvious method would be the
removal of AlCl
3
from the silane product mixture of the direct synthesis. Since it has a
considerable solubility in this mixture it can´t be filtered off.
Published are several procedures to bond dissolved AlCl
3
to solids in packed bed columns. For
this, reactions with Lewis-basic functional resins, clays or sodium chloride (NaCl) to give
sodium tetrachloroaluminate (NaAlCl
4
) are described in the patent literature
[1]
. The problem
of packed bed columns is the limited mass flow which can be realized with this kind of
equipment if the mobile phase is a liquid and the complexity of the regeneration or renewal of
the column material. Thus, a high volume production can usually not be achieved if the
purification of the product mixture involves passing it over a packed bed. Furthermore, the
reaction with NaCl works best in the gas phase and at elevated (> 180°C) temperatures to
remove the then molten NaAlCl
4
from the packed bed, but this causes high process costs and
may result in changes in the product mixture due to undesired side reactions.
More suitable for mass production would be processes which generate an insoluble aluminum
compound directly after synthesis by addition of an agent to the product mixture. The resulting
compound could then be removed by separation processes like filtration or phase separation.
These conversions should be fast and complete at or near room temperature to remove all or
most of the aluminum in a short time and with low costs. The strong Lewis-acidic nature of
AlCl
3
is very helpful in this respect.
The reaction of AlCl
3
with NaCl to yield NaAlCl
4
can be carried out by adding NaCl to the
product mixture and stirring the resulting slurry. But this is a very slow process since the
160
140
120
100
80
60
40
20
0
-20
-40
ppm
MiniSpec -CopyrightCorporateAnalyticsWackerChemieAG
CurrentDataParameters
NAME 2682153D-LIMS
EXPNO
10
PROCNO
1
F2 -AcquisitionParameters
Date
18.09.2014
Time
15.18.08
INSTRUM
spect
PROBHD 5mmPABBOBB-
PULPROG
zg
TD
16384
SOLVENT
CDCl3
NS
1024
DS
4
SWH
52083,333 Hz
FIDRES
3,178914 Hz
AQ
0,1572864 sec
RG
574.7
DW
9,600 usec
DE
7,00 usec
TE
299,2 K
D1
1,00000000 sec
========CHANNEL f1========
NUC1
27Al
P1
6,30 usec
PL1
0,00 db
SFO1
130,3183240 MHz
F2 -Processingparameters
SI
32768
SF
130,318329 MHz
WDW
EM
SSB
0
LB
1,00 Hz
GB
0
PC
1,40
1DNMRplotparameters
CX
28,22 cm
CY
16,16 cm
F1P
168,299 ppm
F1
0,00 Hz
F2P
-40,159 ppm
F2
0,00 Hz
PPMCM
7,38818 ppm/cm
HZCM
0,00000 Hz/cm
Integrale
AlCl
3
144