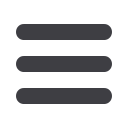
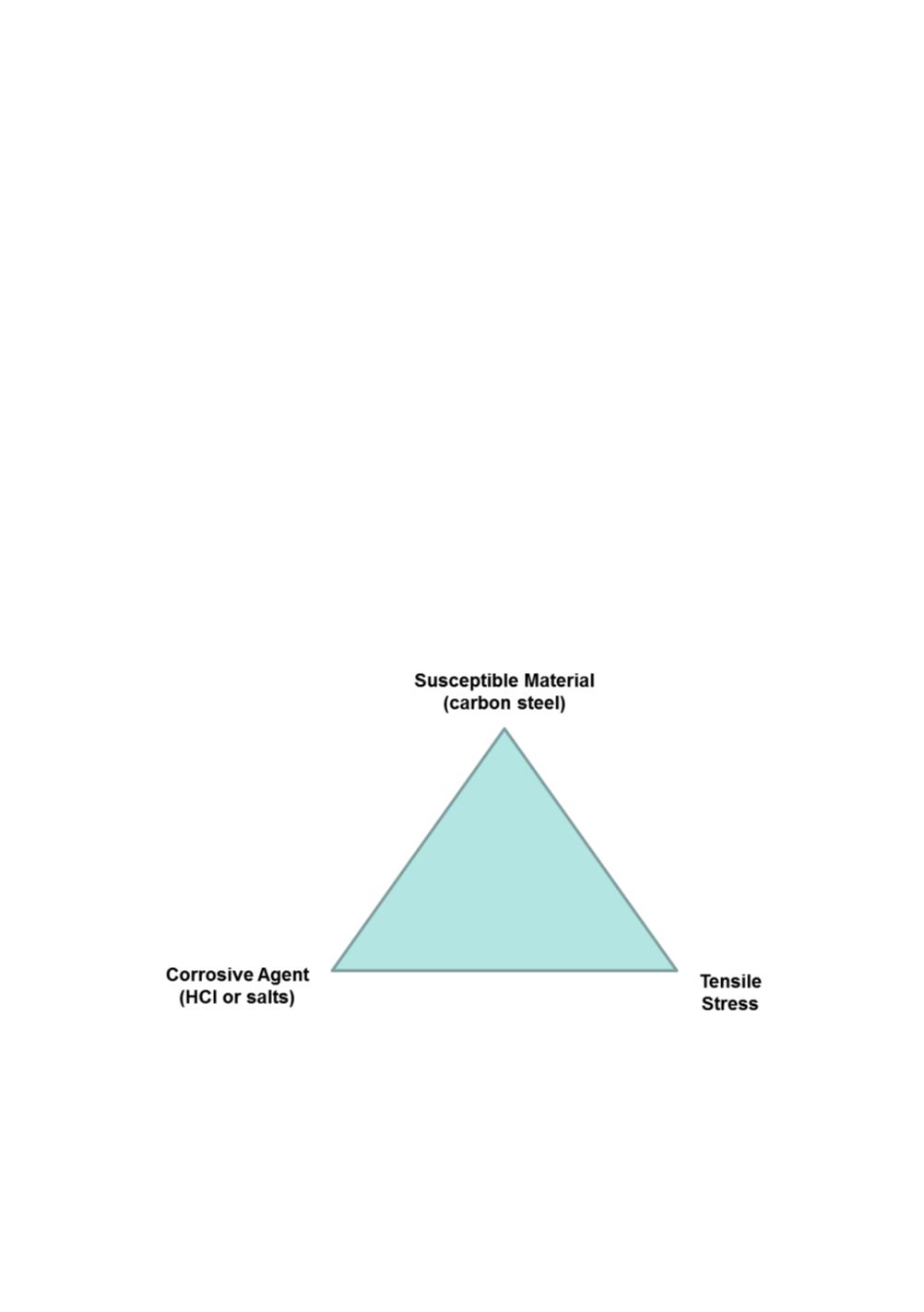
In this investigation the fractures are only located at areas where high stress might be
present; at lifting lugs and at the knuckle radius where extensive forming has
occurred. Carbon steel is generally considered immune to chloride stress corrosion
cracking, but chlorides were the main component in the crack.
A search of literature uncovered two chloride based agents identified as causing stress
corrosion cracking of carbon steel, by HCl+AlCl
3
(2) and FeCl
3
(3). Although the
conditions are not identical, literature does establish a precedent for chloride stress
corrosion cracking in carbon steel under the correct conditions.
In the trichlorosilane reactor, the feed materials are hydrogen chloride and
metallurgical silicon. The major metallic impurities in the metallurgical silicon are
iron and aluminium, which will react with hydrogen chloride to form salts. It is
feasible that the salts and hydrogen chloride are then able to react with the surface of
the carbon steel to form a very thin but brittle iron (II) chloride layer. The tensile
stress within the steel is then able to crack this brittle chloride layer, forming further
corrosion products and resulting in the slow propagation of a crack.
Mitigation
Stress corrosion cracking requires several conditions to co-exist, in this case a
susceptible material, a corrosive medium and residual tensile stress. This can be
illustrated with a triangle, similar to a fire triangle. If one of the conditions is
eliminated, then the SCC will not occur.
Figure 10:
Required conditions for stress corrosion cracking.
Susceptible Material
The material of construction is carbon steel, which is susceptible to chlorination
resulting in iron (II) chloride. Although it is feasible to use a different alloy, this
would be an expensive solution.
SCC
177