
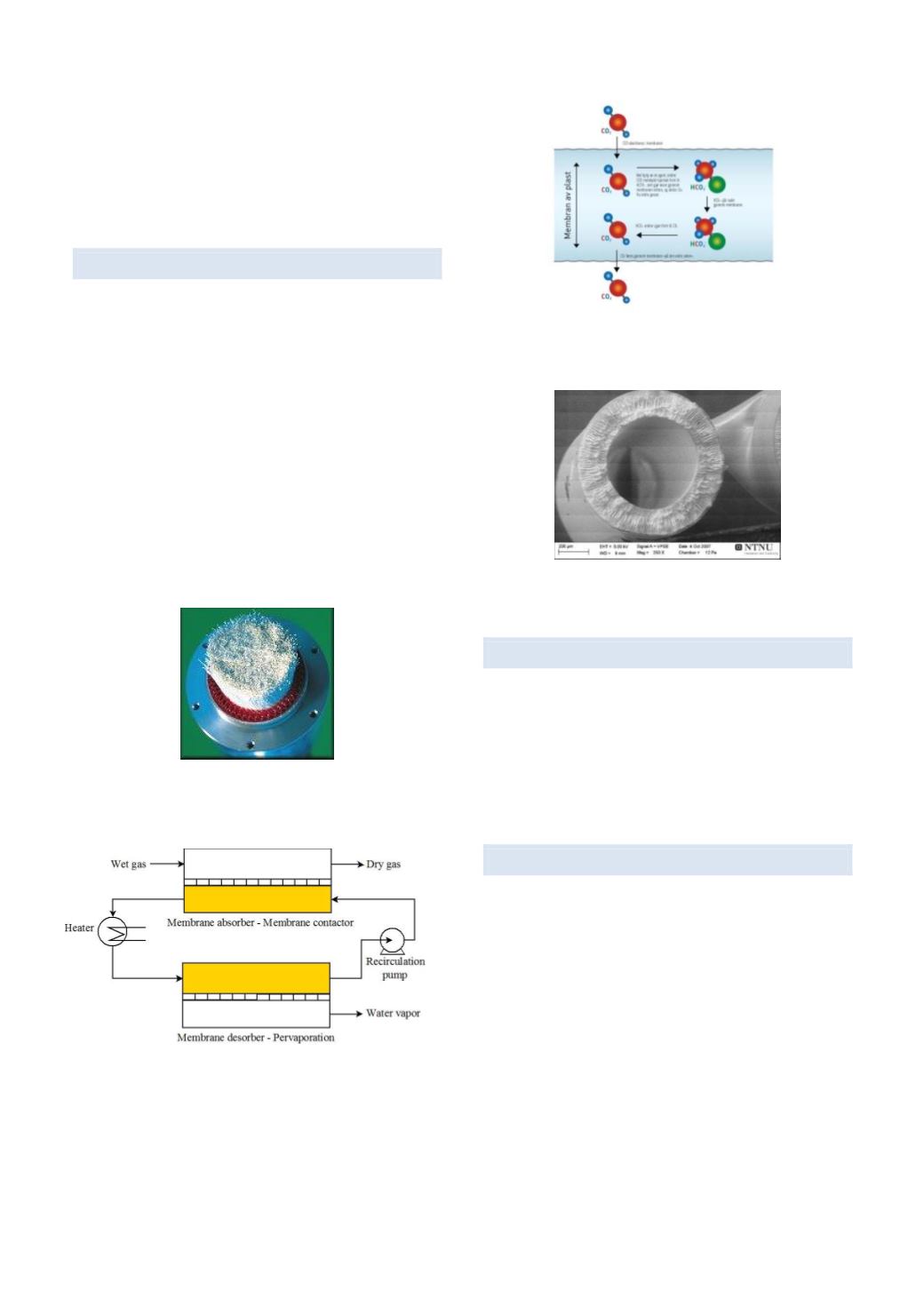
Department of Chemical Engineering
Annual Report 2015
30
phase of execution is to design and construct large
modules for a two-stage FSC-membrane system, and to
prove the performance as expected from process
simulation and additionally to document the membrane
durability by exposed to the flue gas of Brevik cement kilns
over 24 months.
BIP GASSMAKS/ NFR PROJECT NAGAMA
The project started late 2011 ended in 2015. The
objective has been CO
2
removal from high pressure
natural gas streams using a polymeric blend membrane;
using as one of the polymers in the blend the patented
PVAm facilitated transport membrane – other materials
suitable for high pressure applications are also
considered. The project includes material development,
pilot construction, durability tests and simulations. The
main challenge in this project is to maintain the good
performance at high pressures (
100 bar). Advanced
high pressure test rigs have been built, one for
permeation tests and one for durability tests. Special
restrictions for HMS are very important in this operating
range. Industrial partners are Statoil and Petrobras.
Bundle of hollow fibre membranes in an industrial
module–packing densities can be up to 30 000 m2/m3
Illustration of the mechanism in the patented CO2
facilitated transport membrane
SEM-picture showing a membrane. D0-DI: 1-6 mm cut
though a hollow fibre
KMB PETROMAKS / NFR A GREEN SEA
The project started in 2010, and Sintef Energy is the
coordinator and ended in 2015. The project has had
activities within four alternative technologies for natural
gas sweetening. Memfo’s activity within the project has
been to development of a nanocomposite membrane
material for a membrane contactor There were two PhD-
students in the project, one within Memfo.
MCIL-CO
2
/ NFR /CLIMIT
The project started in the middle of 2012 with focus on
the development of a novel membrane contactor
process using ionic liquids as absorbents for pre-
combustion CO
2
capture. The project is scheduled for 4
years and finances 2 PhD-students within Memfo. The
research activities include (1) build up a lab scale setup
and simulation modules to demonstrate the proposed
process and (2) provide knowledge and experimental
data for the further up-scaling of the process. In 2013
two exchange PhD students from the project partner also
contribute to this project in the development of ionic
liquid based solvent.