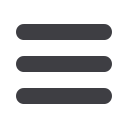
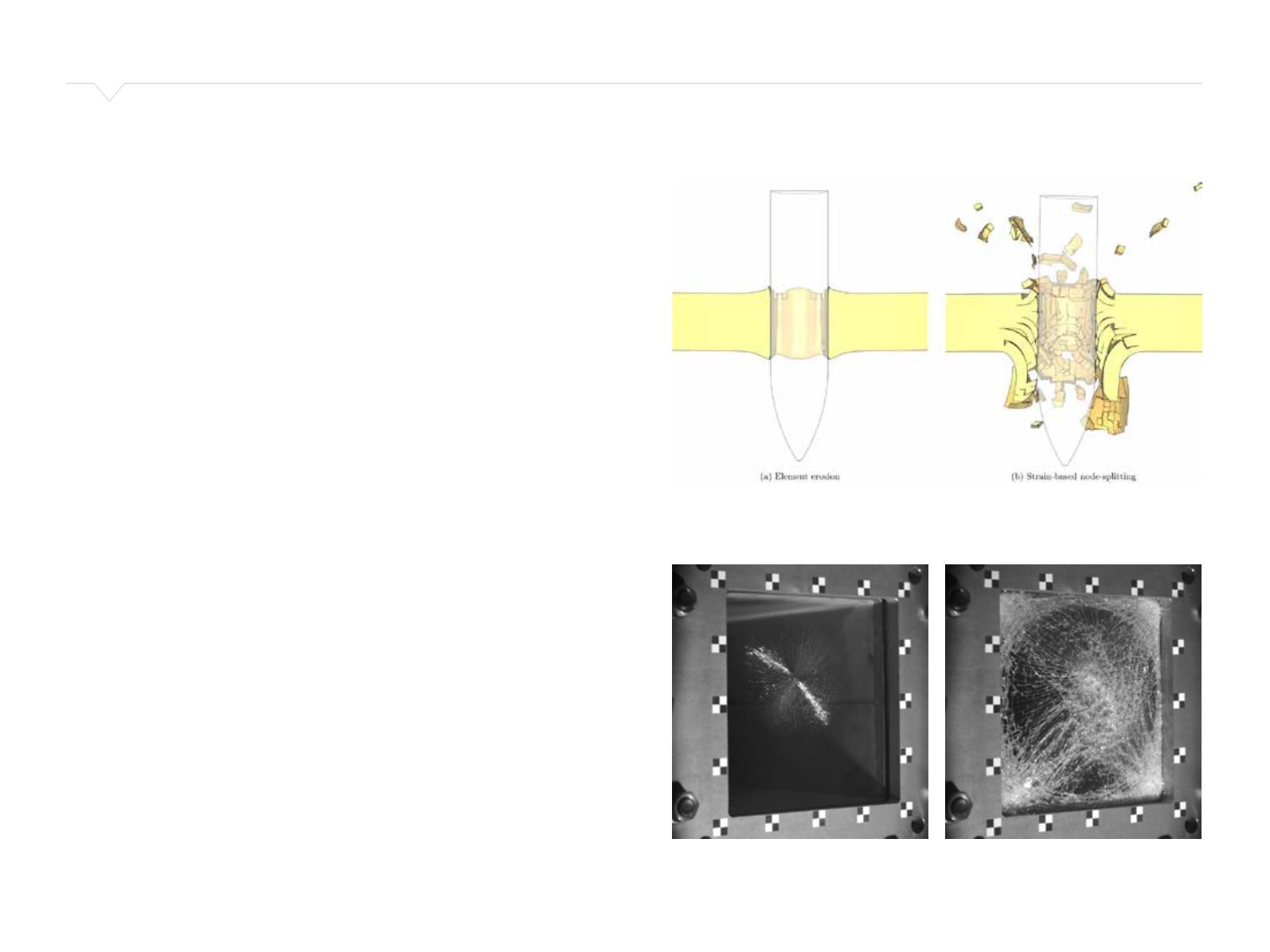
18
Research Programmes
Protective Structures
Head of Programme: Tore Børvik
Design against accidental loads, such as explosions, impacts
and collisions, has become increasingly important for a
number of engineering and industrial applications. To meet
the challenges posed by such complex loading conditions,
product development and structural analysis are increasingly
carried out in virtual environments using the finite element
method to achieve safer and more cost-effective designs. The
fundamental goal of protective structures is to improve the
survivability of people and vital infrastructure to a given threat.
It is important to realize that the protective structure is the
last layer of defence against a threat when all other protective
measures have failed. It is thus of utmost importance that such
structures are designed and validated on a sound theoretical
and experimental basis. To do so, accurate, efficient and robust
constitutive models and solution techniques used in a multi-
scale modelling context are required. Further, new designs
need to be validated through high-precision experiments
involving advanced instrumentation such as three-dimensional
digital image correlation for full-field displacement and strain
measurements. Although much information can be obtained
from laboratory tests, relying on such an approach would be
too costly and inefficient. Computer-aided design, together
with a strategy for material selection, optimization and well-
selected validation tests, can significantly lower the cost
and enhance the overall quality and efficiency of the required
protection.
The main objective of this research programme will be to
develop advanced computational tools and establish validated
modelling guidelines for computer-aided design of safer and
more cost-effective protective structures. Another objective
is to replace phenomenological models with physical models
in a top-down/bottom-up multi-scale modelling approach in
order to reduce the number of mechanical tests as much as
possible in the design phase. This will be carried out in close
collaboration with the other projects within CASA.
The main research activities in 2015 have been:
• Experimental and numerical study on the perforation of
empty and sand-filled aluminium panels and Fracture and
fragmentation of AA6070 aluminium plates during impact
loading (Jens Kristian Holmen’s PhD project).
• Experimental and numerical study on plated structures
subjected to blast loading (Vegard Aune’s PhD project).
• Fragmentation of window glasses exposed to blast loading
(Karoline Osnes’ PhD project).
• Impact against coated and uncoated offshore steel pipes
(Ole Vestrum’s CASA project).
The two first PhD projects are activities from SFI-SIMLab,
which are directly pursued in SFI-CASA. Karoline Osnes’ PhD
project was started in August 2015, while Ole Vestrum started
his PhD project on Optimization of protective structures in
January 2016. Examples from the PhD projects of Jens Kristian
Holmen and Karoline Osnes are shown in Figure 8 and Figure 9.
Figure 8: Images from simulations of a 20 mm thick plate in aluminium alloy AA6070 with (a) element erosion and (b)
node splitting in the IMPETUS Afea Solver.
Figure 9: Images from blast-load experiments in SIMLab’s shock-tube facility on a double-laminated window glass
showing initial (left) and final (right) cracking.