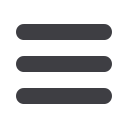
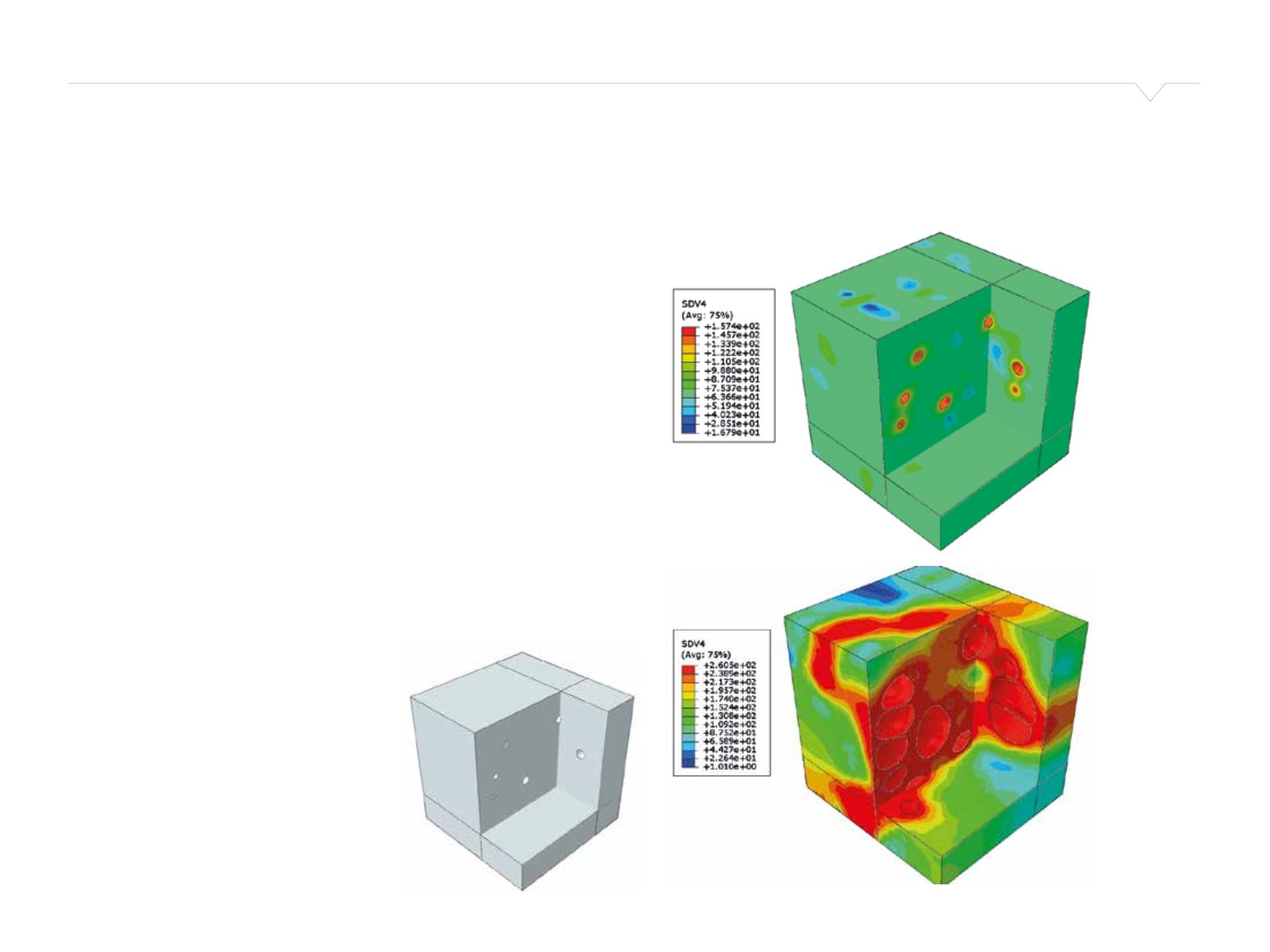
15
reSearch PrOGrammeS
Constitutive models describe the stress and internal variables
(representing in an average sense the microstructural
rearrangements of the material) as functions of the strain,
strain rate and temperature. In large-scale simulations of
structures, the framework of continuum thermo-mechanics
is typically adopted to formulate the constitutive models,
while thermo-mechanical testing is used to identify the model
parameters. Advanced constitutive models, including plastic
anisotropy, non-linear isotropic and kinematic hardening,
strain-rate and temperature dependence, damage evolution
and failure, tend to have a large number of model parameters.
In close collaboration with the Lower Scale programme, this
research programme applies multi-scale methods to develop
validated constitutive models for large-scale simulations
of metal structures. Thus the need for calibration of the
constitutive models against thermo-mechanical tests is
reduced and the prediction accuracy of the models increased
with respect to properties that are not always easily measured
by testing. Qualitative and quantitative descriptions at
different length scales are closely accompanied by well-
designed experiments at the relevant length scales for the
phenomena of interest (from the nano-scale to the complete
structure), as a basis for achieving improved understanding,
model development and model validation. The quantum,
atomistic and nano scales are covered by the Lower Scale
programme, while this programme deals with crystal plasticity
and continuum plasticity at the micro, meso and macro scales.
The themes of the two research activities in 2015 have been:
• Micromechanical modelling of ductile fracture in aluminium
alloys: The principal objective of this project is to develop
computational micromechanical models for strain localization
and ductile fracture, see Figure 5. These mesoscale models are
applied to aluminium alloys with various microstructures and
used to develop physically-based fracture models for large-
scale simulations of structures. However, the computational
micromechanical models developed here will be used for steel
and polymers in other projects in CASA.
• Ductile fracture of aluminium alloys at low stress triaxiality:
an experimental and numerical study: The two main objectives
of this project are a) to acquire new knowledge on the physical
mechanisms governing ductile fracture in aluminium alloys at
low stress triaxiality by use of experiments at various scales
and computational cell simulations and b) to develop improved
computational material models for damage evolution, strain
localization and fracture of these materials.
These activities are in turn the PhD projects of Lars Edvard
Bryhni Dæhli (2013-2017) and Bjørn Håkon Frodal (2015-2019).
The first is a continued activity from SFI-SIMLab which is highly
relevant for SFI-CASA, while the latter activity was started in
August 2015. In August 2016, Sondre Bergo will begin his
PhD study in this programme. The tentative topic for his PhD
project is micromechanical modelling and simulation of steel
materials.
Metallic Materials
Head of Programme: Odd Sture Hopperstad
Figure 5: Simulation
of void growth and
coalescence in unit cell
with multiple
pre-existing voids.