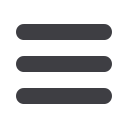
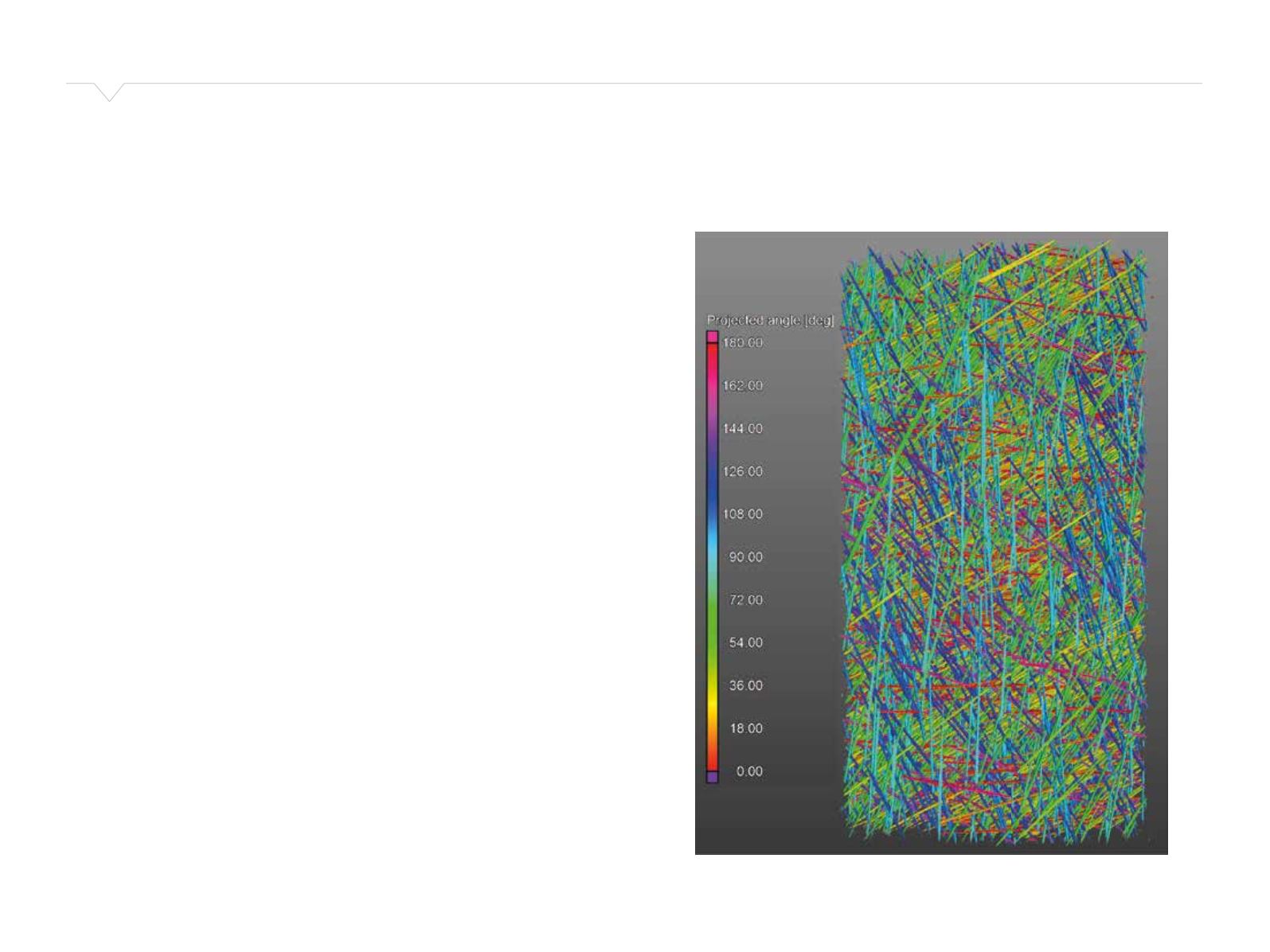
16
reSearch PrOGrammeS
Polymers comprise a wide range of materials, including natural
and synthetic materials. The demand for such materials
has increased considerably during the last few decades.
Applications include safety-related parts in cars, coatings,
thermal insulation in offshore components, seals and inter-
glass layers in laminated windows. The finite element method
has only recently been employed as a tool in the design
process of parts made of polymers. Therefore, constitutive
models for such materials are less mature than for metals.
Prediction of fracture is also a topic of interest for research and
industry. Knowledge about the physical mechanisms governing
the thermo-mechanical behaviour is of utmost importance for
successful development of material models.
The main objective of the research programme Polymeric
Materials is to develop and improve material models
representing the thermo-mechanical response up to fracture
for polymers. The models will be developed for application in
an industrial context. Particular attention is paid to validation
and efficient identification of the parameters involved in the
models. Actual materials include commodity thermoplastics
(like PE and PP, commonly reinforced with small mineral
and/or rubber particles), fibre-reinforced thermoplastics,
elastomers and foams made of polymers.
The research activities in 2015 have been within the following
fields:
• Modelling of polymers.
• Characterization and modelling of large-strain response of
ductile thermoplastics.
• Characterization and modelling of glass-fibre reinforced
polymers.
• Start-up of a new PhD project on modelling of ductile failure.
The first of these projects has gained major attention since
2012. The polymer model now includes a hypoviscoelastic–
viscoplastic part. Depending on the material and problem at
hand, the viscoelastic and viscoplastic parts may be switched
on or off. Anisotropic elasticity, which is relevant for fibre-
reinforced polymers, is also implemented in the model.
Further, three damage models are included. For validation,
there has been cooperation with Toyota for a couple of years.
It was continued in 2015 through the master’s thesis of John
Fredrick Berntsen, which was carried out at Toyota Motor
Europe’s Technical Centre in Brussels from January to June.
This joint master thesis served to enhance the application
of the model at Toyota, and seems to be an adequate way of
implementing technology at the user partners.
The large-strain response of ductile thermoplastics has been
the topic of Marius Andersen’s PhD project, which is about to
be finished. It contains development of robust methods for
experimental characterization as well as a constitutive model
that is able to represent the stress-strain curve at different
strain rates and temperatures. Petter Henrik Holmstrøm
started his PhD project on the modelling of fibre-reinforced
materials in August 2013. Improved material models should
in some way take the distribution of fibre orientation angles
into account. A preliminary computer tomography (CT) scan
of a polypropylene reinforced with glass fibres, see Figure 6,
shows promising results.
The three first activities are continuation activities from SFI
SIMLab which are highly relevant for SFI CASA. Sindre Olufsen
has been engaged to work on the PhD project on the modelling
of ductile fracture in the period 2015 – 2019.
The interaction with the industrial partners engaged in the
Polymeric Materials programme is maintained through annual
technical meetings. Such a meeting was arranged in Munich in
early November 2015, and gathered Audi, BMW, Gassco, Statoil
and Toyota.
Figure 6: Computer tomography (CT) scan of glassfibre – reinforced polypropylene (PP).
Polymeric Materials
Head of Programme: Arild Holm Clausen