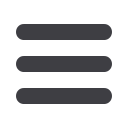
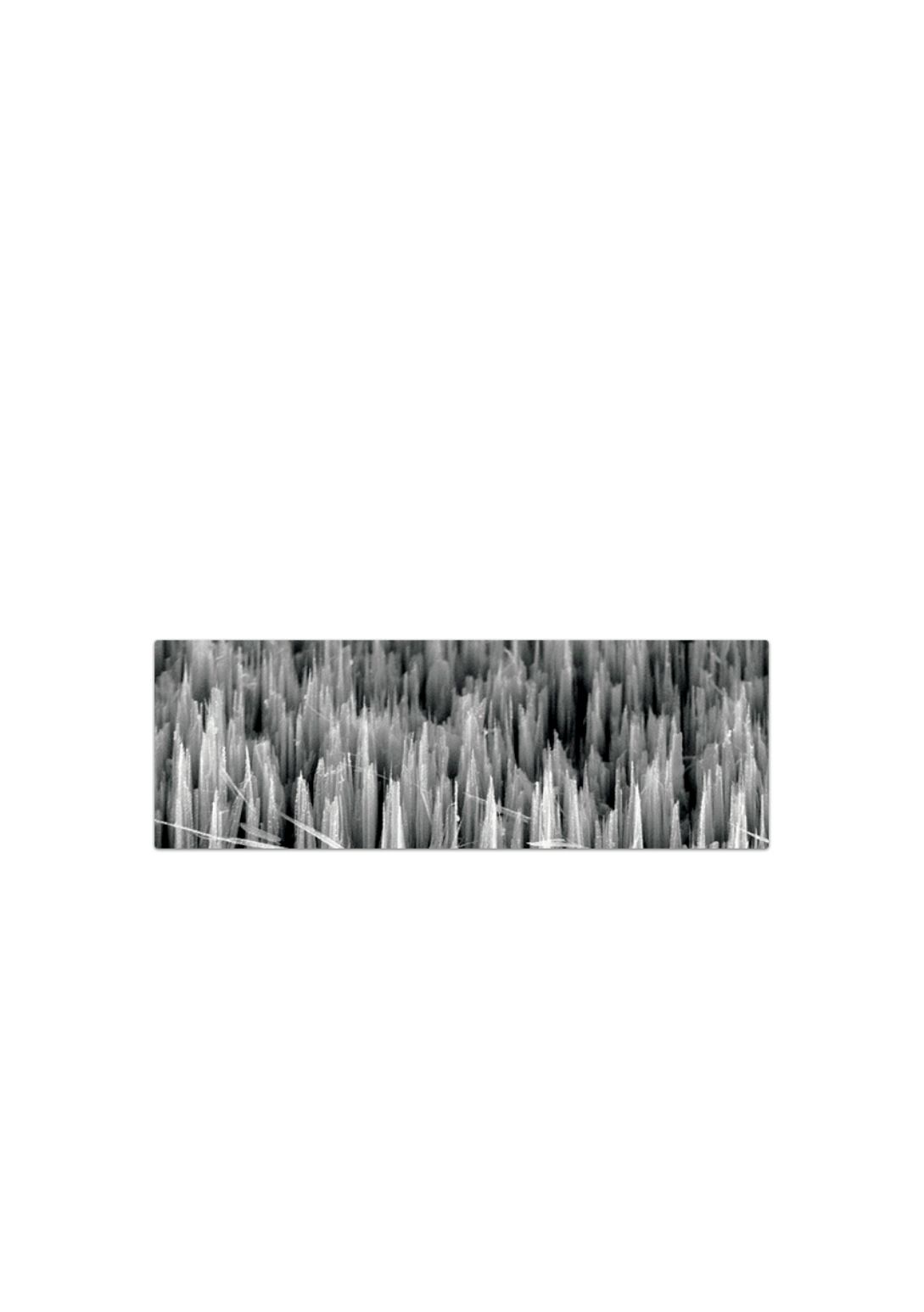
Batteries
One of the major focuses of Li-ion batteries over the last two decades has been in the
development and discovery of novel anode architectures with enhanced properties such
as increased capacity, cycle life and rate performance, together with consideration of
production cost and environmental impact. Silicon has been considered the best choice
for a number of important theoretical considerations.
Firstly, silicon forms a stable alloy with lithium of up to 4.4
ܮ
݅
ା
per formula unit Si,
leading to a vast theoretical capacity of 4212
݉
ܣ
ή ݄ ή ݃
ିଵ
, which is considerably higher
than that of graphite (372
݉
ܣ
ή ݄ ή ݃
ିଵ
). Secondly, Si anodes display long voltage
plateaus at approximately 370 mV vs Li/
ܮ
݅
ା
, thereby providing stable operating voltages
when coupled with positive electrodes such as LiCoO
. Lastly, Si is the second most
abundant element in the Earth's crust and is thus considered a candidate for reasons of
viable production cost and availability. However, silicon has a drawback that it is fact
that Si suffers from a large volume change (±400%) during (de)alloying process, the
strain of which potentially leads to pulverization of the local structure.
In order to avoid the latter problem, one approach mixes small quantities of silicon
particles in a flexible polymer binder, adding carbon to the mix to conduct electricity.
Tesla, for example, is increasing the capacity of his car batteries by adding little by little
increasing amounts of silicon in the anode. They have set the goal of increasing the
capacity of its batteries by 5% per year (although not all this increases will solely due to
adding more silicon).
&ŝŐƵƌĞ ϭ
͘
WŝůůĂƌĞĚ ƐŝůŝĐŽŶ ƉĂƌƚŝĐůĞ ƉƌŽĚƵĐĞ ďLJ ĂƐƐŝƐƚĞĚ ĞƚĐŚŝŶŐ
A novel approach by Nexeon has been to form nanoscale Si pillar arrays on micron scale
(2-25 microns) by metal assisted etching (Fig. 1), the resulting structure is treated with
binder and additives to form a composite electrode.
Independently of the approach, it is required micronized silicon with a purity between
99,99% to 99,999%.
18