
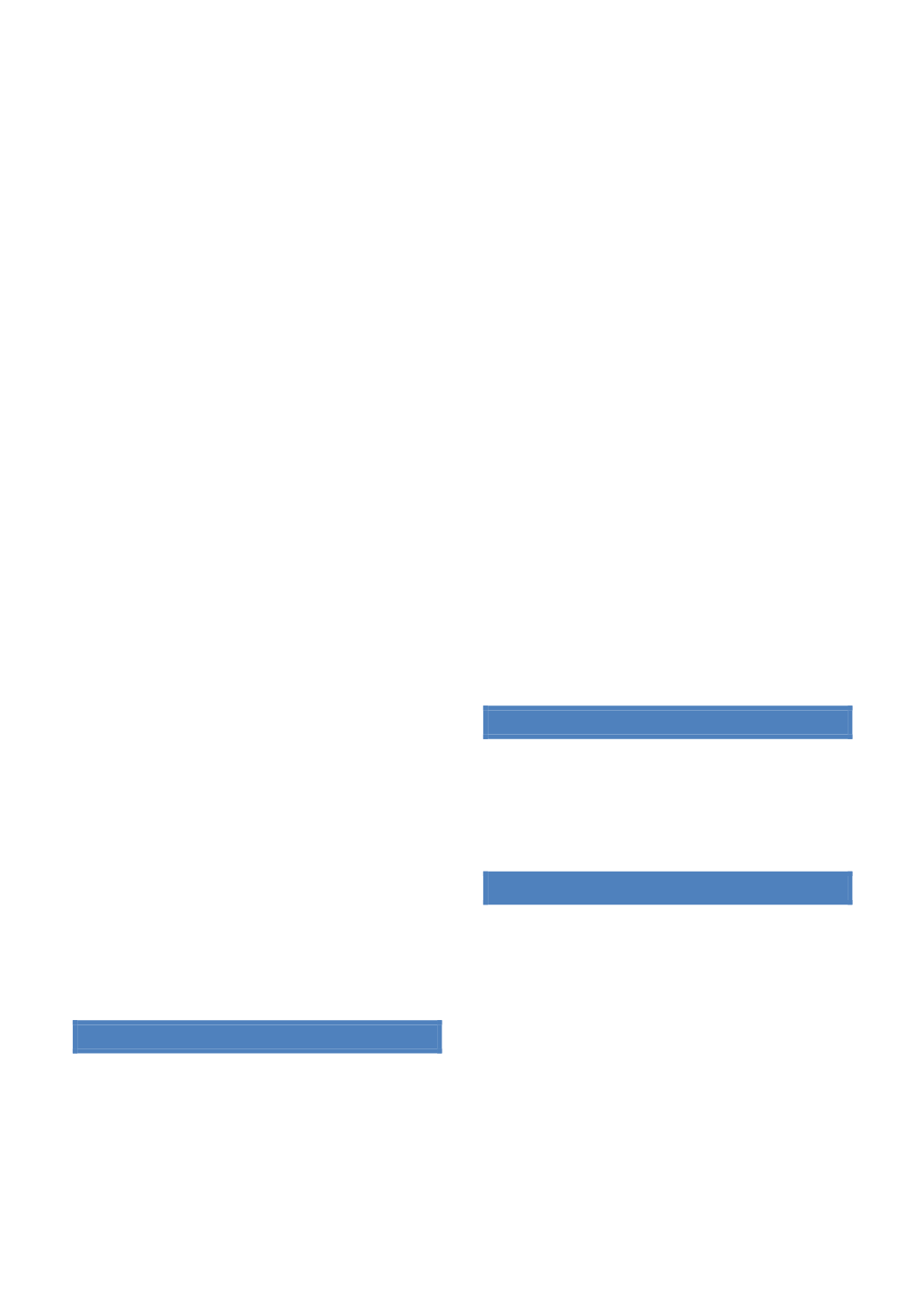
Department of Chemical Engineering
Annual Report 2015
20
developing consistent and structurally solvable process
models on different scales that match the particular
application. The technology is physics-based with
extensions to allow for grey-box modelling. It aims at
replacing various graphical interfaces to simulators and
generates code for the major chemical engineering
simulators such as gProms, Matlab, Modelica etc. but will
also be able to generate stand alone, application-tailored
simulators. The fourth generation of a high-level
modelling tool (Preisig) incorporates object-oriented
tools for efficient thermodynamic modelling, which
extend into the efficient computation of thermodynamic
information. Rather than a traditional implementation of
activity or fugacity coefficients, emphasis is put on the
use of structured equation sets governed by
thermodynamic consistency rules (Haug-Warberg).
The thermodynamic models are implemented in
symbolic form with automatic differentiation capabilities
and serves as the basis of several industrial strength
simulations (YASIM, CADAS) and energy accounting tools
(HERE) in co-operation with Statoil, Hydro and Yara
(Haug-Warberg). A primary aspect of thermodynamic
(and other physics) modelling is the required consistency
of physical units. We have a procedure to obtain self-
consistent models, including automatic generation of
gradients. This technique has so far been tested up to
sixth order gradients, which are needed for higher-order
critical point calculations.
In cooperation with Yara AS we have implemented a
thermodynamic stream calculator “Yasim”. It has a
gentle learning curve using the familiar Excel worksheet
interface whilst using state-of-the-art thermodynamic
methods. All model information including mass balances,
energy balances, chemical and phase equilibrium
relations are defined in symbolic form. Differentiations
are done in symbolic form. These properties add
unsurpassed flexibility to Yasim that is not found in any
other software of its kind. The ease of use should make
it ideally suited for training and use in an industrial
environment.
MULTI-SCALE MATERIALS MODELLING
The MoDeNa project, which NTNU (Preisig) is
coordinating, is part of EC's Framework 7 program.
MoDeNa stands for
Mo
delling of morphology
De
velopment of micro- and
Na
nostructures and is part
of an EC cluster consisting of 4 + 1 projects: Deepen
(Tyndal, Irland), MMP (TNO, Netherlands), NanoSim
(SINTEF), SimPhoNy (Fraunhofer, Germany) plus a fifth
associated member ICMEg (RWTH, Aachen). The
cluster's objective is to generate a platform for the
materials modelling for process and product design,
which in the long run extends to operations, thus control
on all scales The MoDeNa consortium includes UNITS
(Trieste, Italy) for nanoscale modelling, VSCHT (Prague,
Czech Republic) for mesoscale modelling, Uni Stuttgart
(Germany) for thermodynamic properties, TUE
(Eindhoven, Netherlands) for micro-scale fluid
properties, POLITO (Turin, Italy) for macroscopic flow,
Wikki (London, GB) for the platform, BASF
(Ludwigshafen, Germany) for the cases of thermoplastic
Polyurethane and Polyurethane foams. IMDEA (Madrid,
Spain) for the modelling of the mechanical properties,
whilst DIN (Berlin, Germany) is together with NTNU
attempting to define a standard for the representation
of mathematical models. NTNU is the coordinator and
responsible for the generic organisation of the models,
workflows, data models and data storage as well as the
systematic generation of surrogate models, which
involves a loop of design of experiments – detailed
model simulations – fitting of the surrogate model –
quality assessment and if necessary an improved design
of
experiments.
Preisig is also member of EMMC, the EC's European
Materials Modelling Council.
MODEL-PROCESS INTERFACE
The model generally needs to be fitted to experimental
data, and the group has always had a strong focus on
statistical methods and experimental design (Hertzberg).
Although Professor Hertzberg retired in 2007, he is still
active in this area, and in particular, in mentoring.
SYSTEMS BIOLOGY
The system biology activity in the group is rather new,
and we here provide a more detailed status on it.
Whereas the rest of the Process Systems engineering
group looks at any process, whether it is a large industrial
scale process or a smaller parts of the process, and strive
to model, optimize and control it, the systems biologist
in the group (Nadav Bar and coworkers) use similar tools
to achieve the same in processes from the world of
biology. This includes understanding the biological
system, modelling it qualitatively and quantitatively,
analysing the models to find hidden properties, and
ultimately developing control applications in order to
drive the system towards more desired objectives. We