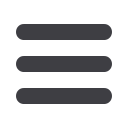
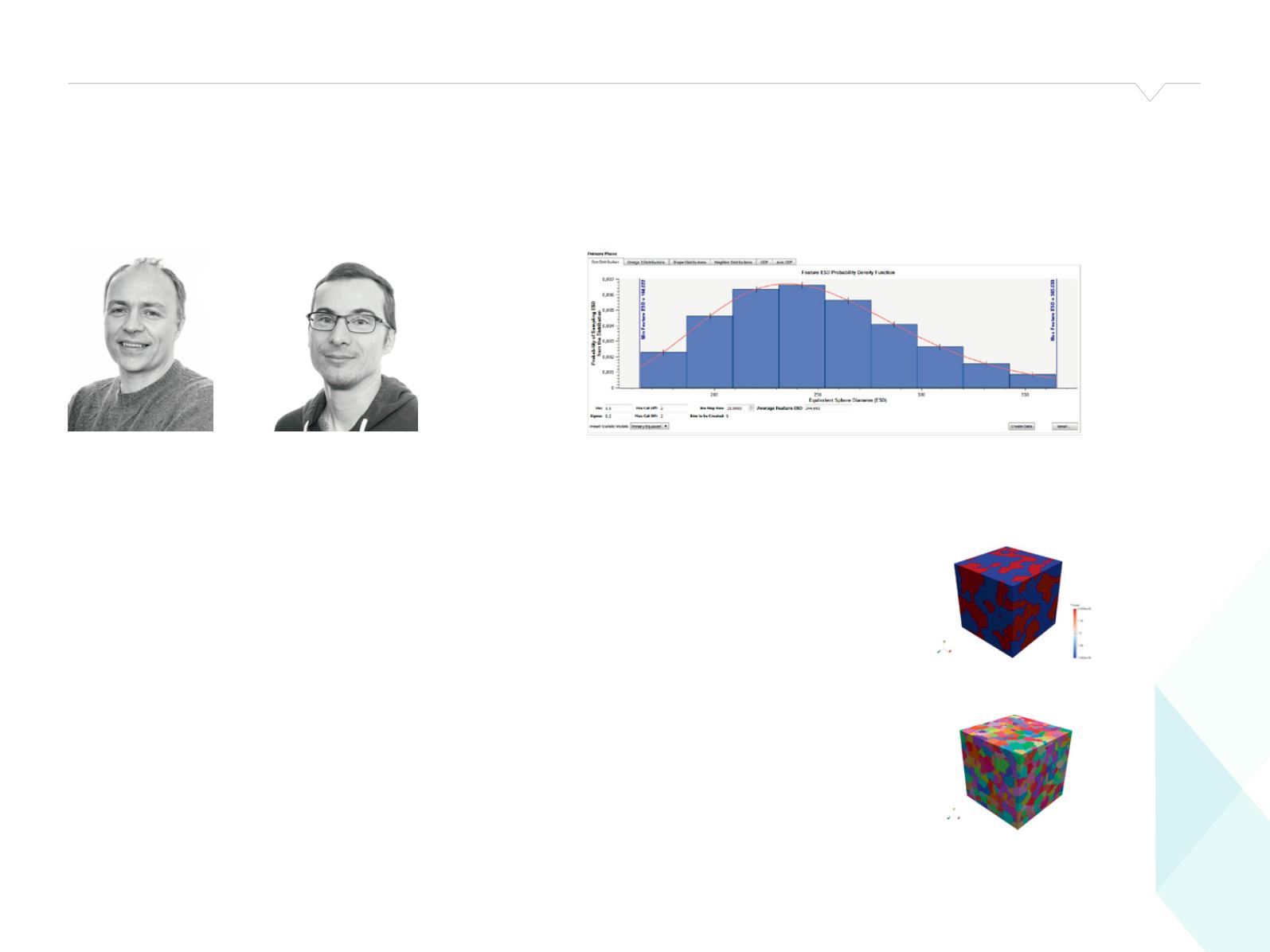
19
technology tRansFeR
Methods and Tools
Heads of Programme: Odd-Geir Lademo and Térence Coudert
The Methods and Tools Programme represents the main
instrument to link
Basic research
at the Centre to Industrial
implementation at the industrial partners. The SIMLab Toolbox
is a synthesis of the research results. It supports and guides
the user to the necessary steps to build a reliable finite element
model for advanced structural analysis, such as selecting
the suitable material model, processing experimental data,
calibrating and optimizing the material model parameters.
Two main tasks have been performed during 2016. One was to
improve the existing SIMLab Toolbox and the other, in close
collaboration with the Metallic Materials Programme, was to
develop and introduce new tools for multiscale modelling.
Components in the SIMLab Model Library (SML) have been
released for the partners: SMM for Metals and SPM for
Polymers. Other developments have been carried out for
the SCMM (Crystal Mechanics), the SCZM (Cohesive Zone)
and for the SPPM (Porous Plasticity) and some of them will
be released in 2017. The development work is performed in
a professional software development arena ’
code.sintef.no’
,which enables team-oriented development through proper
systems for documentation, version control, issue tracking,
and continuous feature testing. Using the latter, the SMM
and SCMM are tested against well-known simulation cases
in an automated procedure using LS DYNA and ABAQUS. This
enables the developer to raise issues early when a change is
made in the user material subroutine. The model calibration
toolbox (e.g. MatPrePost) provides identification procedures
for the SMM and the SPM. As other material models could be
supported in the near future (e.g. Johnson-Cook model), the
development of a material card converter has been initiated.
Several tools are needed at different scales to assist the
research in the various programmes. In 2016, focus has
been given to generating representative volume elements
for FEA using the Crystal Mechanics model. The team has
selected an open source software DREAM.3D and developed
plugins that fit the needs of the Centre. As shown in Figure
11, DREAM.3D is modular software package that allows
users to reconstruct, instantiate, quantify, mesh, handle and
visualize multidimensional, multimodal data. It was originally
designed to analyse microstructure data coming from EBSD
observations, and can generate equivalent material structures
(as shown in Figure 12) from statistics that are synthetic or
are extracted from real data. A series of filters have been
developed to allow the generation of 3D hexa-based and 2D
shell-based meshes, with corresponding material cards for the
SCMM. The generated input files are for LS DYNA or ABAQUS.
During a multiscale modelling approach, several solvers and
data sets are used. Since the solvers may run on different
platforms and a variety of machines, the development team
has tried to find a solution to obtain an efficient mechanism
for storing and exchanging data. This problem is well-known in
software development and some solutions already exist (e.g.
SOFT5 in EU project NanoSim).
Figure 11: DREAM.3D software: plugin interface to control the grain distribution.
Figure 12: Example of
generated microstructure.
TECHNOLOGY TRANSFER