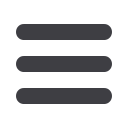
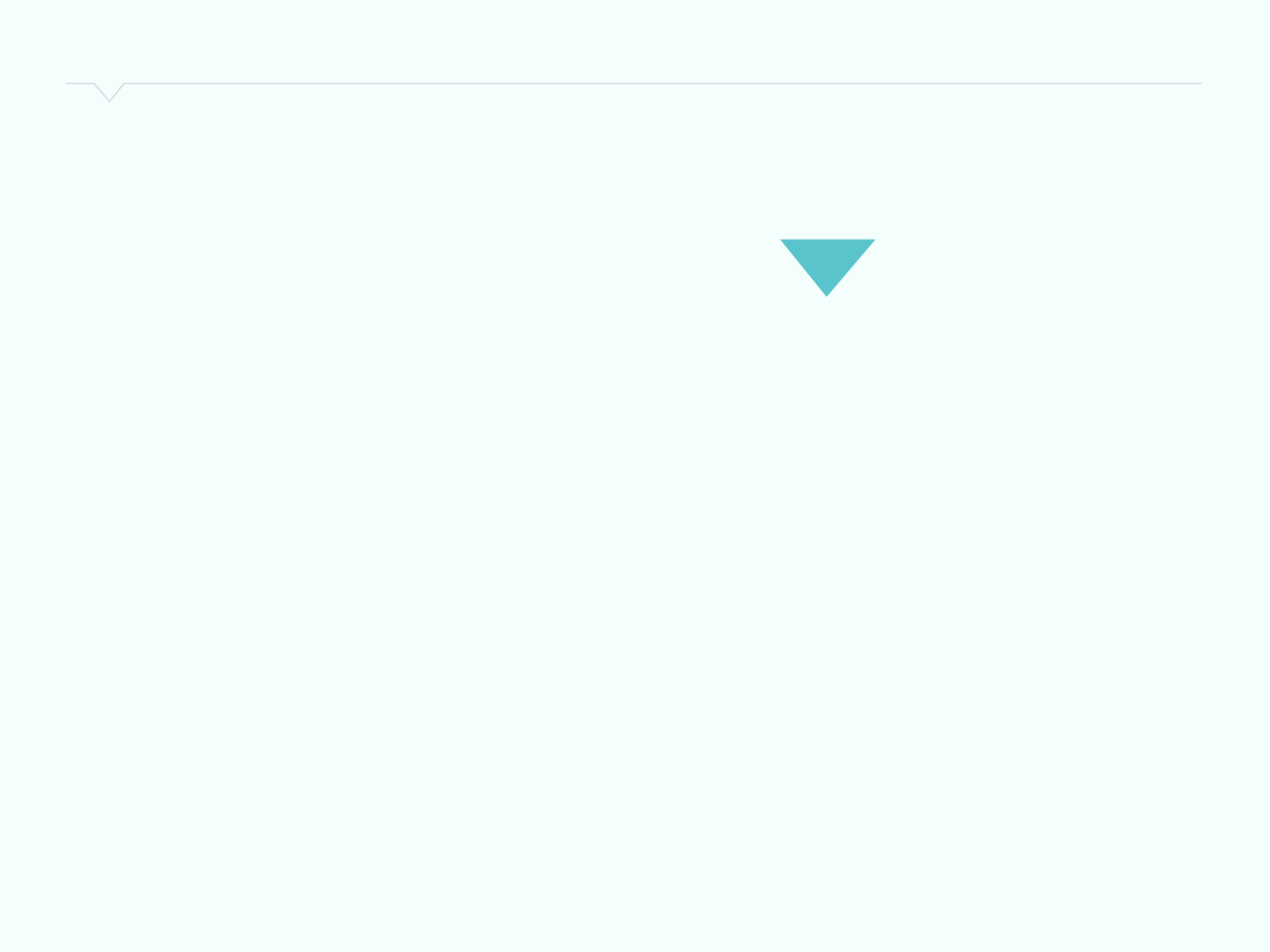
8
story
“I became involved with Honda as a master’s student, when
Professor Magnus Langseth wanted me to study flow-drill
screw connections between aluminium plates for Honda R&D
Americas. They had contacted SIMLab and wanted to invest in
a long-term strategic partnership. Therefore, this became the
topic for my master’s and PhD theses. This was in 2012.
MUTUAL BENEFIT
I had been working on the project for two and a half years when
we thought it was time for me to go and work with Honda for a
while. We anticipated that this would be beneficial both for me
and for the partnership between Honda and SIMLab. The people
at Honda were excited and we decided on a ten-week stay.
On 11 April I found myself in the huge parking lot in front of
the R&D building in Columbus, Ohio. Coming from a tiny island
in Norway where there are ten cars per hour on heavy-traffic
days, the size of things at Honda amazed me. I was working
in a shared office space with two thousand others. The office
was the size of three football fields, very different from the
SIMLab environment. Working in such a large company was
very interesting. I learned a lot about being a small part in
a big machine and about the dynamics of large companies. A
couple of weeks after I started, we worked out a draft work
plan for my stay, based on previous discussions. Honda had
a list of suggestions about what I could do there. Professor
Langseth and Associate Professor David Morin gave their input
to the plan in a video meeting. I believe that this was a key
point for the success of my stay. Now the partners and I had
a mutual agreement about the expectations and I could spend
the limited time efficiently.
FULL-VEHICLE CRASH SIMULATIONS
While at Honda, I had the opportunity to work with full-
vehicle crash simulations. The size and complexity of these
simulations are astonishing, with 15 million elements and
thousands of different parts. In my PhD research I have been
working on how to model FDS connections in large-scale
finite element simulations. However, before I went to Honda
I had only worked on rather simple simulations, mostly with
a single connector. To understand the physics of what is going
on in a connection, we performed experiments with simple test
specimens under controlled loadings. Furthermore, to evaluate
the accuracy of different macroscopic modelling techniques
for FDS connections, we simulated the tests and compared
the results with the test results. Working with the full-vehicle
simulations at Honda gave me valuable experience regarding
FDS modelling as well as experience with different aspects of
large finite element simulations in general. For Honda it was
valuable to learn how to use the macroscopic model that was
currently most promising for FDS connections.
INCREASED KNOWLEDGE TRANSFER
An important motivation for SIMLab to send me to Honda was to
increase the knowledge transfer between the two partners. One
of SIMLab’s strengths is the modelling of aluminium and Honda
is using aluminium in several of their cars. This was therefore
a good opportunity for Honda to apply and understand the
SIMLab Toolbox and the SIMLab Metal Model. I held workshops
for people in my work group involved in the modelling of
anisotropic aluminium where I lectured on the Toolbox and
they got hands-on experience using it for the calibration of the
Metal Model. I believe this experience was very interesting for
Honda. Eric DeHoff, a senior researcher at the core methods
group, said that he had listened to presentations from SIMLab
about the Toolbox several times but had not really understood
it until now. I believe this is a good example of how we can
efficiently transfer knowledge between SIMLab and our
industrial partners.
DIFFERENT PHILOSOPHIES
Knowledge transfer goes both ways. Working on aluminium
modelling with Honda gave me the opportunity to learn about
their philosophy when it comes to material modelling and
the models they are using. One aspect was that SIMLab and
Honda have some significantly different philosophies. For
large-scale simulations, the philosophy at SIMLab is to use
simple parameterized phenomenological material models
which conform to well-established physical principles (like
positive plastic dissipation). The complexity of the models
and the number of calibration tests needed, depend on what
physical behaviour you want to capture in the simulations
(for instance anisotropic behaviour). At Honda, the result
in the end (comparison between component simulation
and the experiment) is most important, not whether the
models comply with physical principles. If a model violates
a few thermodynamic principles but is easy to calibrate and
gives satisfactory predictions of the anisotropic behaviour,
an engineer will use it anyhow. I believe this is a common
difference between academia and industry. Understanding
the different ways of thinking is important to “bridge the
gap” between SIMLab and its industrial partners and between
academics and industry in general.
ROOM FOR IMPROVEMENT
While my stay at Honda was a success, I hope the experience
from my visit can improve other PhD candidates’ future stays
with our industrial partners. However, one thing comes to
mind. During the short time I was there, I did not participate
much in the work they do at Honda. I spent my time working
on the items in my work plan that we set up during the first
weeks. I wish I could have been more involved in some of the
current projects other people in my group were working on. In
retrospect I realize that this is a point that should have been
included with the rest of the items in the work plan in the first
place.
Long story short: I have learned a tonne, gained experience for
myself and SIMLab, had fun and made new friends.”
PhD candidate Johan Kolstø Sønstabø
spent ten weeks at Honda R&D Americas
as part of his work on flow-drill screw
connections to join aluminium sheets.
Here is his report from the stay:
MY STAY WITH
Honda R&D Americas