High temperature heat pumps will reduce CO2 emissions and lower energy use
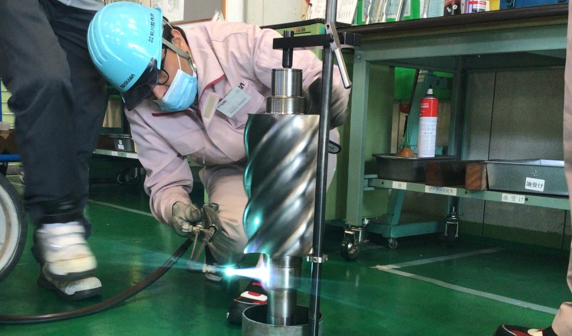
Some industries require temperatures of between 100 and 180 degrees. A high temperature heat pump is able to deliver this, so it has great commercial potential.
The reduction of climate gas emissions is a global challenge for todays and future generations to minimize the impact of global warming. In fact, the discussion is no longer IF there is a global warming effect rather than HOW MUCH global warming will occur. The energy demand of the industry stands for around 1/3 of the world’s climate gas emissions and for a successful decarbonization of this sector, new technologies need to be phased in.
Today’s industry moves towards an electrified energy system based on wind, solar and other renewable sources, and more frequent recovery of industrial waste heat. This enables the integration of high-temperature heat pumps for processing heat supply hereby reducing the demand for fossil fuels significantly.
Heat pump research to overcome challenges
Utilizing the potential of industrial heat pumps is highly attractive since it allows the industry to operate with significantly reduced emission of climate gases. However, there are challenges connected with implementing heat pump technology, especially in high-temperature applications such as industrial processes and district heating. There is a need for technical innovations to achieve lower specific investment costs and increased energy efficiency while maintaining technical feasibility and stable operation.
My research focuses on experimental analysis of high temperature heat pumps which can deliver temperature 100-180 °C using natural refrigerants for various industrial applications.
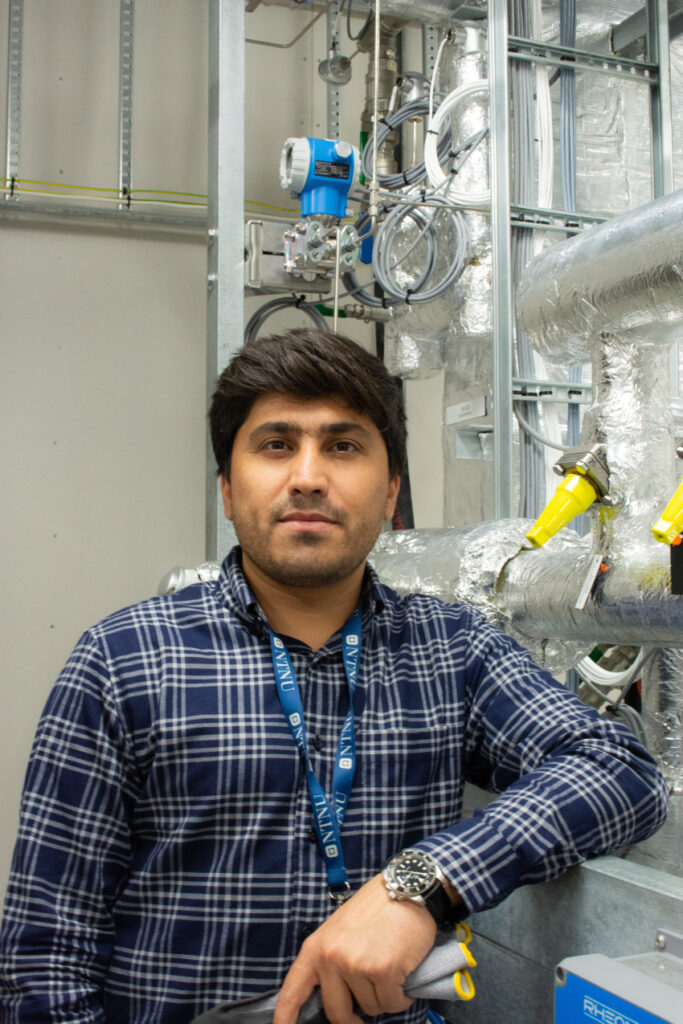
My research: Experimental evaluation of a prototype
The main objective of my PhD is to evaluate a novel oil-free absorption-compression heat pump. Here I will use an ammonia-water mixture as refrigerant to demonstrate the system performance and to test new solutions. The goal is to increase the achievable temperature level while improving system efficiency and potentially reducing costs.
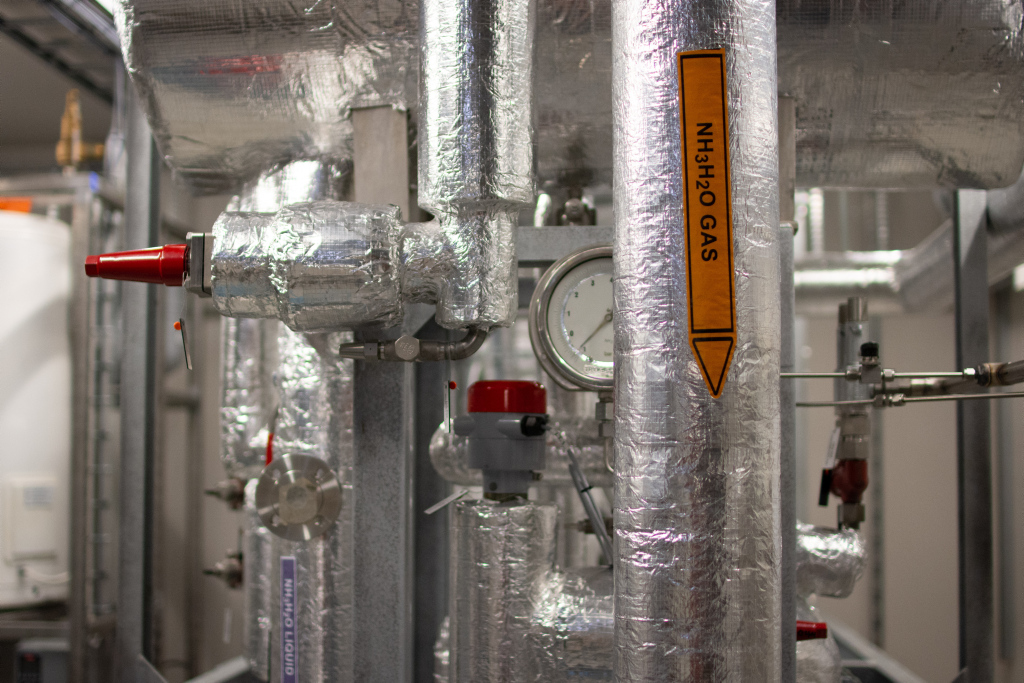
The main barriers to a wider deployment of heat pumps in industrial sectors are insufficient knowledge of integration in industrial processes among potential users, and the lack of available solutions with environmentally- friendly refrigerants in the high temperature range. The development of the new prototype helps to test different solutions and experimentally validate the results for cases of use. This will help to increase the acceptance for transition and application in the industry.
When we start using oil-free heat pumps there are some compressor challenges
The current challenges involve large temperature lifts, which limit thermodynamic performance. Specific components, such as the compressor, need to be designed to operate at higher temperatures. In addition, high investment costs can result in limited economic performance. During the application of oil free compression, lubrication is very important for de-superheating which is a necessary part of the process.
However, the oil-free screw compressor has some major challenges:
- more maintenance requirements
- shorter lifespan (bearing issue)
- not quite suited for heavy-duty use.
Knowledge exchange with Japan
To understand these challenges more deeply a team from EPT (NTNU) visited Mayekawa Japan in October.
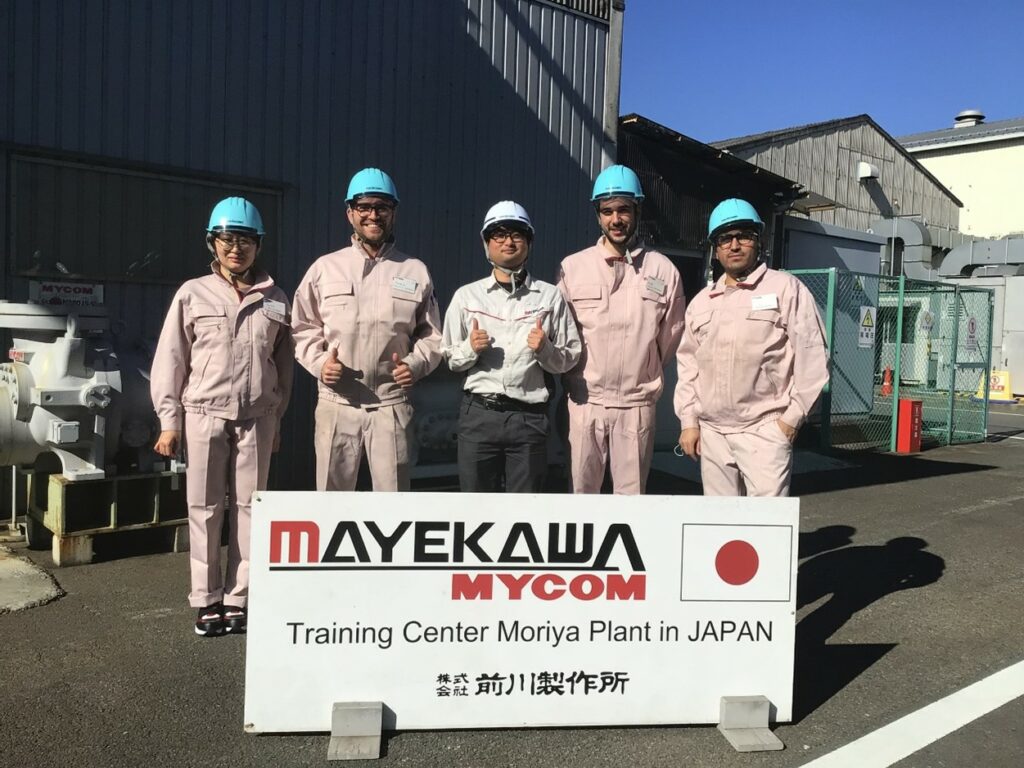
One of the purposes of our training was to know how to assemble and dissemble the compressor in our test rig, in case there is a problem.
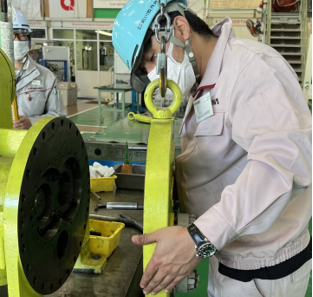
The training in Japan taught us a lot, and we are looking forward to making use of the experiences back at NTNU.
Hopefully our work will contribute to a Decarbonization of the industrial sector.
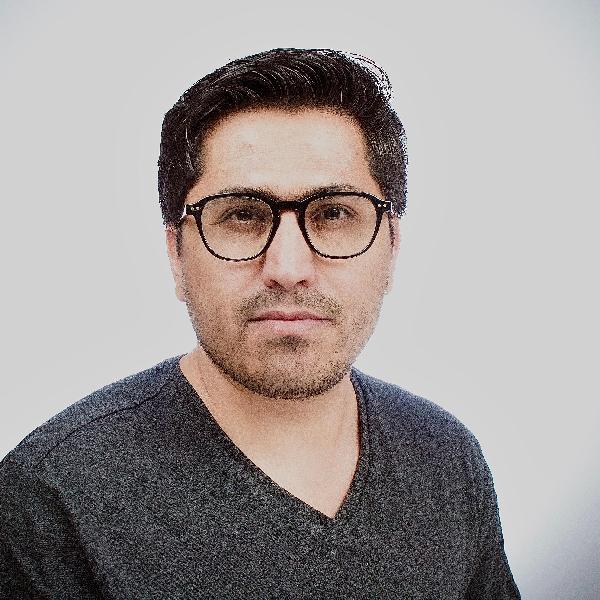
About
Khalid Hamid is a PhD Candidate at NTNU – Department of Energy and Process Engineering (EPT). His PhD is funded by NTNU Energy, and he is affiliated with the research centre FME HighEFF and the test facility and infrastructure are funded by both the HighEFF Lab and NTNU EPT. For his research, he collaborates with a variety of partners from HighEFF (SINTEF, Mayekawa, Alfa Laval). His supervisor is Trygve M. Eikevik and co-supervisor is Ignat Tolstorebrov.
Khalid Hamid
Search
Søk
Categories
- Arctic Research
- Arkitektur
- Bærekraft
- Bioingeniørfag
- Biologi
- Biology
- Biomedical Laboratory Science
- Biotechnology
- Bioteknologi
- Chemical Engineering
- Chemistry
- Climate
- Computer Science
- Datateknologi
- Digital
- Elektronikk
- Energi
- Energi
- Energy
- Engineering
- Engineering
- Environment
- Food Science
- Forskning
- Fysikk
- Fysikk
- Havbruk
- Informasjonsteknologi
- Informasjonsteknologi
- Ingeniørvitenskap
- Kjemi
- Kjemisk prosessteknologi
- Kjemisk prosessteknologi
- Kreftbehandling
- Kybernetikk
- Marine Technology
- Materialer
- Materials Science
- Materialteknologi
- Matvitenskap
- Meninger
- Miljø
- Min ph.d.
- My PhD
- My PhD
- My postdoc
- Nanotechnology
- Nanoteknologi
- Ocean
- Oil and gas
- Physics
- Research
- Simulering og visualisering
- Spør en forsker
- Studentliv
- Sustainability
- Ukategorisert
- Universitetsliv
- University Life
Kategorier
- Arctic Research
- Arkitektur
- Bærekraft
- Bioingeniørfag
- Biologi
- Biology
- Biomedical Laboratory Science
- Biotechnology
- Bioteknologi
- Chemical Engineering
- Chemistry
- Climate
- Computer Science
- Datateknologi
- Digital
- Elektronikk
- Energi
- Energi
- Energy
- Engineering
- Engineering
- Environment
- Food Science
- Forskning
- Fysikk
- Fysikk
- Havbruk
- Informasjonsteknologi
- Informasjonsteknologi
- Ingeniørvitenskap
- Kjemi
- Kjemisk prosessteknologi
- Kjemisk prosessteknologi
- Kreftbehandling
- Kybernetikk
- Marine Technology
- Materialer
- Materials Science
- Materialteknologi
- Matvitenskap
- Meninger
- Miljø
- Min ph.d.
- My PhD
- My PhD
- My postdoc
- Nanotechnology
- Nanoteknologi
- Ocean
- Oil and gas
- Physics
- Research
- Simulering og visualisering
- Spør en forsker
- Studentliv
- Sustainability
- Ukategorisert
- Universitetsliv
- University Life