The lab-created colours inspired by feathers and soap bubbles
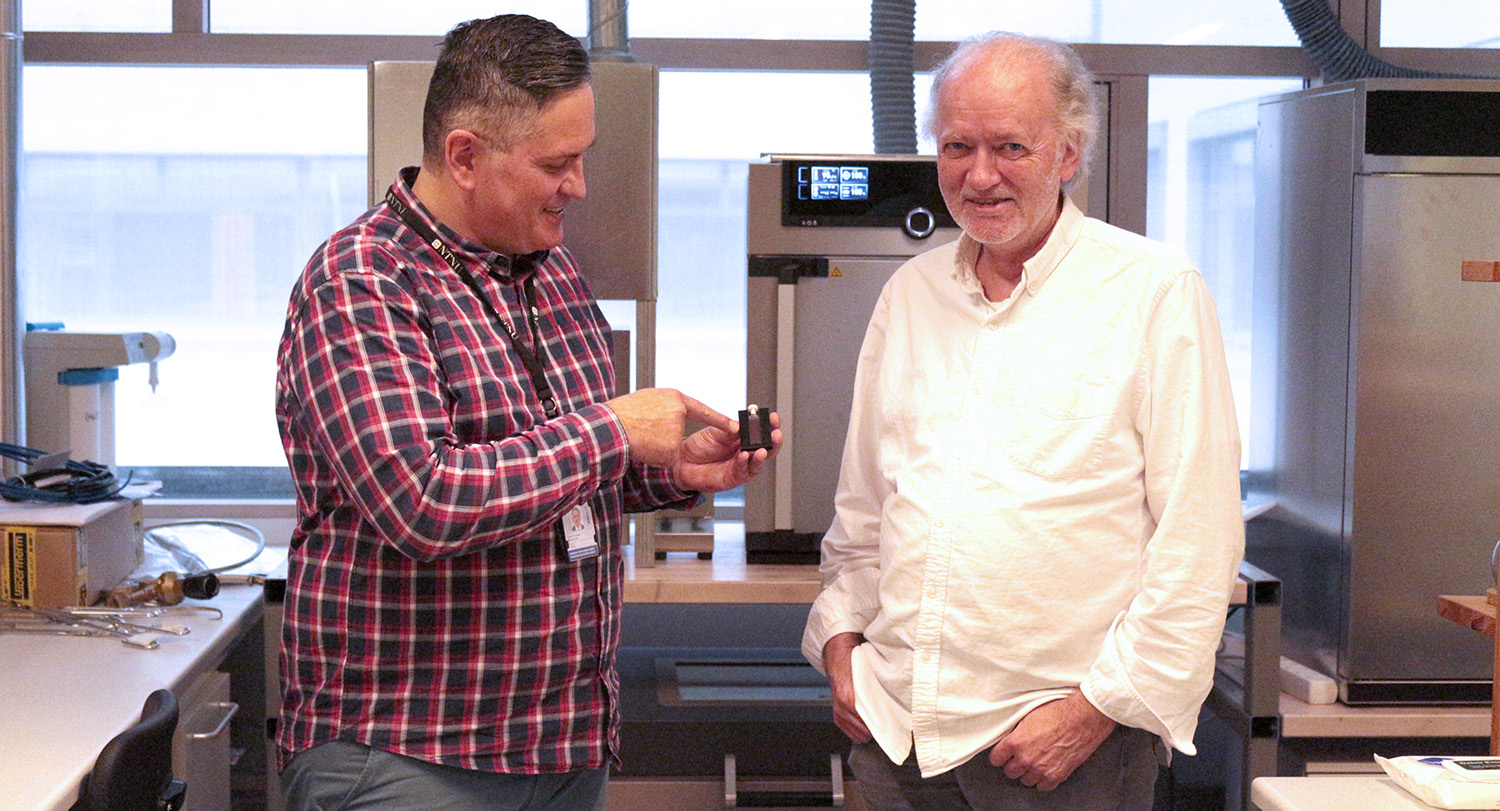
Birds, butterflies, and many other natural objects get their bright colours from intricate structures on their surfaces. Now researchers at NTNU have used the same principle to create colours with clay nanostructures.
When choosing paint for a wall, or tiles to decorate a bathroom, we might take inspiration from nature. But there’s a good reason why, right now, our walls don’t truly live up to the bright blue of a peacock’s feather or the deep orange of a butterfly’s wing.
Colours can be produced in two fundamentally different ways: chemically or physically. Our existing paints, plastics and cosmetics contain chemical pigments that absorb all wavelengths of light except for one, which is reflected, giving them a corresponding colour. Physical or structural colours, on the other hand, are produced not by light-absorbing chemical pigments but by the way the light interacts with a nano-sized structure. “This is what we find in nature,” says Jon Otto Fossum, a professor in the Soft and Complex Matter Lab at the Department of Physics, NTNU.
The nanostructures themselves – found on a bird’s feather, the wing of a butterfly, or even the berries of some plants – are almost transparent. “You shine white light on it, and what actually happens is that most of the light goes straight through, but some light is reflected from each interior interface,” says Fossum. It is the interaction between these reflected rays, known as constructive interference, that creates the colour. Rainbows and soap bubbles get their colours the same way.
Mimicking soap bubbles
Now, in work funded by NTNU and by the Research Council of Norway, Prof. Fossum, together with other researchers at NTNU and at the University of Bayreuth in Germany, have found a way to create structural colours using very thin sheets of clay suspended in water. If these clay suspensions can be solidified and then ground into pigments, they could replace the toxic chemical pigments currently used in paints, textiles, and even cosmetics, creating long-lasting colours that don’t fade over time.
There are two different approaches to making structural colours in the lab. Some researchers try to mimic structures found in nature. Lexus, for example, sells cars in a structural blue that mimics a butterfly’s wing. “Those are very intricate structures,” says Fossum. “It’s not a simple stacking of sheets, it’s like a small Christmas tree on the nanoscale.”
But that is a laborious and time-consuming task – Lexus says it takes eight months to produce enough structural blue pigments for 300 cars. With their clay structures, Fossum and his colleagues have used the same underlying principle but implemented it in a simpler way. “They don’t mimic the exact structure, they mimic the principle,” he says. “It’s more like mimicking soap bubbles than mimicking birds.”
Self-assembly
The clay structures, made by NTNU postdoctoral researcher Paulo Michels-Brito, are formed in distinct self-assembly steps. The clay arrives from the University of Bayreuth as a powder, where the powder grains are nano-sized stacks with sodium ions in between each clay layer.

First the clay powder is suspended in water containing caesium salt, and caesium ions insert themselves in between every second layer, with sodium ions remaining in the other interlayers. In a second spontaneous process, the clay stacks are “cleaved” apart at the sodium interlayers, producing a suspension of double layered nanosheets. Finally, in a third spontaneous self-assembly process, the distances between the double-layered nanosheets are tuned either by varying the clay concentration or by varying the amount of salt in the water. The researchers initially used NTNU’s NanoLab to study the fundamental properties of the clays used for creating the nanostructures.
The idea to make each sheet a double layer came during discussions with collaborators at the University of Bayreuth. The double layers are less transparent than the single clay nanolayers, so they produce much brighter colours than in the single clay layer case. “The most important hurdle that we already passed is to make the double layers,” says Fossum. “That is not straightforward.”
Another hurdle that we have overcome with our way of making structural colours is that we can produce structural red as easily as can we produce the whole visible spectrum. It has been well explained and demonstrated by several groups worldwide why structural red production is notoriously difficult both in natural cases and by using artificial nanostructures. Our solution to the “red problem” is still another factor that makes our concept interesting for industrial upscaling.
As in nature, the separation between one double layer and another is what determines the colour the clay produces. “What happens with the chameleon is that it stretches the skin and changes distances, and that changes its colour,” says Fossum. Chameleons also have dark skin below their colour producing nanostructure to absorb the light that passes through the structure, a strategy Fossum and colleagues also adopted.
Many structural colours found in nature are iridescent, meaning they change when viewed from a different angle. But having a colour that is fixed no matter the viewing angle is more useful for many human applications – and it requires a relatively small amount of disorder in the structure. “We get that automatically in our system because the clay platelets buckle, they are not stiff,” says Fossum.

Next steps
Having made structural colours with synthetic clays, the researchers are now extending this concept to natural clays, which come with more defects and impurities that make the process trickier. But natural clays have the advantage of being widely available. “If you want to, let’s say, paint all the houses in the world with such new structural pigments, we have to go over to natural clays,” says Fossum.
As well as paints, the clay structures could be added to textiles and cosmetics, says Fossum. But first the researchers need to find a solid, transparent carrier matrix to replace the water, so that the distances between the double layers are maintained when the structures are ground into pigments. That matrix will make up the vast majority of the material, so getting it right is vital. “That’s why we’d like to develop a matrix that is a recyclable, sustainable material, so they don’t contribute to more microplastics in the oceans,” he says.
Reference
Bright, noniridescent structural coloration from clay mineral nanosheet suspensions, Paulo H. Michels-Brito, Volodymyr Dudko, Daniel Wagner, Paul Markus, Georg Papastavrou, Leander Michels, Josef Breu, Jon Otto Fossum, Science Advances 8(4), DOI: 10.1126/sciadv.abl8147 (2022)
Grant acknowledgements
These studies were performed under NTNU Ph.D. grant project number 81771176, supported by Research Council of Norway project numbers: 250619 (Nano2021) and 272919 M-ERA-NET2/0007/2016-CellColor. Initial studies were performed under project NTNU Nanolab and the Norwegian Micro- and Nano-Fabrication Facility, project number 295864
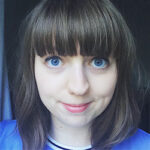
Kelly Oakes
Kelly Oakes is writing science articles for NTNU Nano. She is a freelance writer and editor living in London.
Search
Søk
Categories
- Arctic Research
- Arkitektur
- Bærekraft
- Bioingeniørfag
- Biologi
- Biology
- Biomedical Laboratory Science
- Biotechnology
- Bioteknologi
- Chemical Engineering
- Chemistry
- Climate
- Computer Science
- Datateknologi
- Digital
- Elektronikk
- Energi
- Energi
- Energy
- Engineering
- Engineering
- Environment
- Food Science
- Forskning
- Fysikk
- Fysikk
- Havbruk
- Informasjonsteknologi
- Informasjonsteknologi
- Ingeniørvitenskap
- Kjemi
- Kjemisk prosessteknologi
- Kjemisk prosessteknologi
- Kreftbehandling
- Kybernetikk
- Marine Technology
- Materialer
- Materials Science
- Materialteknologi
- Matvitenskap
- Meninger
- Miljø
- Min ph.d.
- My PhD
- My PhD
- My postdoc
- Nanotechnology
- Nanoteknologi
- Ocean
- Oil and gas
- Physics
- Research
- Simulering og visualisering
- Spør en forsker
- Studentliv
- Sustainability
- Ukategorisert
- Universitetsliv
- University Life
Kategorier
- Arctic Research
- Arkitektur
- Bærekraft
- Bioingeniørfag
- Biologi
- Biology
- Biomedical Laboratory Science
- Biotechnology
- Bioteknologi
- Chemical Engineering
- Chemistry
- Climate
- Computer Science
- Datateknologi
- Digital
- Elektronikk
- Energi
- Energi
- Energy
- Engineering
- Engineering
- Environment
- Food Science
- Forskning
- Fysikk
- Fysikk
- Havbruk
- Informasjonsteknologi
- Informasjonsteknologi
- Ingeniørvitenskap
- Kjemi
- Kjemisk prosessteknologi
- Kjemisk prosessteknologi
- Kreftbehandling
- Kybernetikk
- Marine Technology
- Materialer
- Materials Science
- Materialteknologi
- Matvitenskap
- Meninger
- Miljø
- Min ph.d.
- My PhD
- My PhD
- My postdoc
- Nanotechnology
- Nanoteknologi
- Ocean
- Oil and gas
- Physics
- Research
- Simulering og visualisering
- Spør en forsker
- Studentliv
- Sustainability
- Ukategorisert
- Universitetsliv
- University Life