The heat is on – transducer design
To inspect and test oil pipelines is crucial – both for health and safety, and for the environment. But the harsh conditions mean specialised equipment is imperative. When using ultrasound to perform non-destructive testing, this translates into a need for transducers that can withstand extremely high temperatures.
CIUS partner Sensorlink, which offers non-intrusive topside and subsea erosion and corrosion monitoring, needs to solve the challenge of producing transducers that can withstand even greater temperatures than those now available on the market. They have therefore teamed up with CIUS and the University of South-Eastern Norway (USN) on a PhD.

Josh Hoi Yi Siu, with a background from physics at the Hong Kong University of Science and Technology, and a master’s thesis on fabrication and characterisation of piezocomposites from USN, is now working on solving the problem.
He has visited Sensorlink’s plant and seen the current NDT equipment for onshore and subsea applications: “It was incredibly fascinating to see transducers used on such a massive scale while silently maintaining the health of the infrastructure,” Siu says.
Taking the heat
To design and later produce transducers that can withstand temperatures of several hundred degrees, is challenging and labour-intensive: “Due to de-poling (when high heat destroys the transducer), most typical transducer probe materials are incompatible with the temperature specifications,” Siu says. Furthermore, the improved transducers also have to be compatible with Sensorlink’s systems.
“For the transducer to withstand the heat and harsh environment, the crystal itself has to be able to withstand the heat while the other passive materials (matching, backing, housing), have to be thermally stable, having similar thermal expansion and not melting,” he explains.
Despite only being one year into his PhD, Siu is starting to see results: “I have managed to characterise the crystals, and they fit with simulation results, and are now getting ready for high-temperature testing. I am hoping to assemble the transducer and test it under heat for my first publication.”
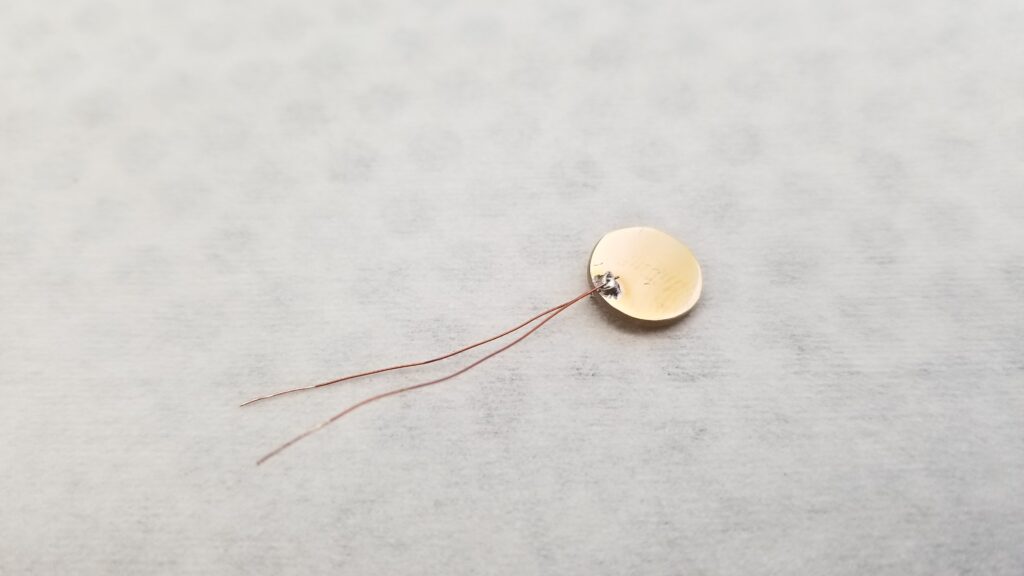
The secret nature of industrial competition
Academia although not a complete stranger to competition and certain levels of secrecy about research and development, is generally about being open and enabling reproducibility – at least after publication. But in industry, some types of secrecy are vital to stay in business. This can pose a challenge when doing a PhD.
One thing is all the details about this project that cannot yet be revealed – another problem is getting information about other transducers already on the market:
“Challenges are the secretive nature of these types of transducers as the manufacturers usually hide their recipes as well as their publications, and thus it takes more experience from supervisors, PhD colleagues, Sensorlink, etc., to make things viable,” Siu says.
However, as CIUS is funded by the Norwegian Research Council, part of the consortium agreement deals with these challenges to ensure the ability to publish PhD-articles – although sometimes with a slight delay to secure patents and intellectual property rights.
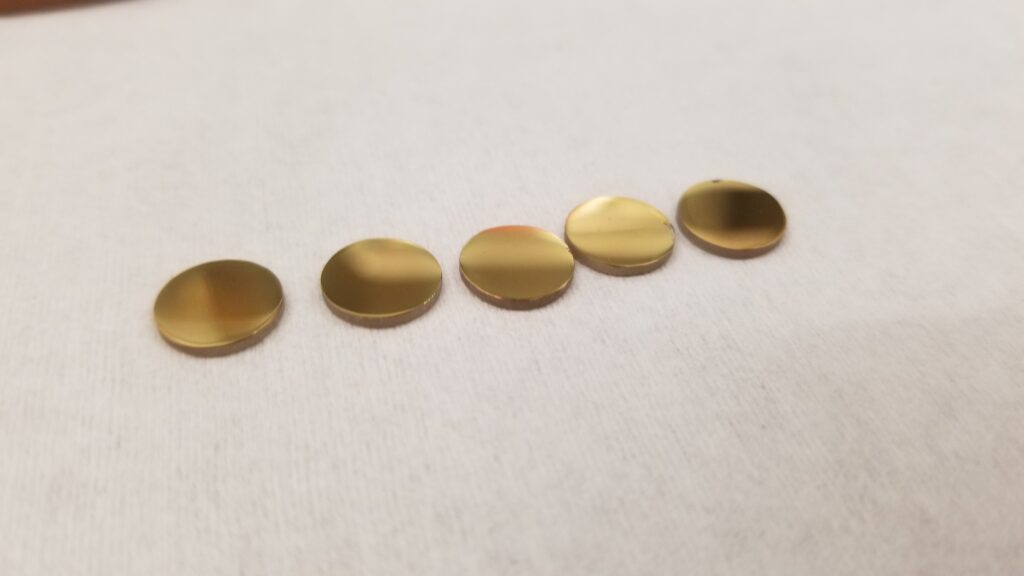
Multidisciplinary benefits
The broad range of topics and disciplines involved in transducer design, and the wider ultrasound subject field, poses its challenges, but also its benefits:
“Academically, I see myself benefiting from knowing the actual industrial setting for the transducers – also gained from attending CIUS events about cardiac imaging, sonars, etc. – as well as the interdisciplinary nature of ultrasound – from physics and electronics, to signal processing, product development, customer service, and so on.
“The synergy and networking opportunities I’ve had with other seasoned engineers, technicians, and management in the ultrasound sector in Norway have been invaluable to my professional development. Being a part of this field has been a fantastic learning experience for me.”
The collaboration is also seen as beneficial for the industry partner: «The collaboration with CIUS has made it possible for Sensorlink to connect with the ultrasound research community in Norway. This is a very valuable opportunity for Sensorlink to benefit from the knowledge and experience of both professors and researchers in the field,” Siu’s co-supervisor Ali Fatemi at Sensorlink says.
What next
If all challenges of making the different layers in a transducer and the electrodes to withstand higher temperatures than the industry standards are overcome, the possibilities extend beyond oil pipelines:
“Upon successful manufacturing, we want to broaden the applications in the future to downhole inspection in geothermal wells, a renewable energy source of increasing interest, inspection of aluminium furnaces and more,” Siu says.
Piezocomposites
Piezocomposites are materials made up of piezoelectric materials and so-called ‘passive’ polymers or epoxy compounds.
Piezoelectric materials are found in for example loud- speakers and microphones, where they ‘translate’ electric signals into sound waves, and vice versa.
This article first appeared in the 2022 CIUS Annual Report.
- Kari Williamsonhttps://www.ntnu.no/blogger/cius/author/kari_williamson/
- Kari Williamsonhttps://www.ntnu.no/blogger/cius/author/kari_williamson/
- Kari Williamsonhttps://www.ntnu.no/blogger/cius/author/kari_williamson/
- Kari Williamsonhttps://www.ntnu.no/blogger/cius/author/kari_williamson/