Higher resolution with new ultrasound probe design
Commercial ultrasound probe designs have their pros and cons, but what if we combine the pros of two designs to create a new type of transducer? One that can acquire more information and producer higher resolution images for improved cardiovascular diagnosis?
This is what I am working on in my PhD at USN with CIUS partners GE Vingmed Ultrasound (Horten, Norway) and GE Parallel Design (Nice France). What we have come up with is the DHUT, by combining piezoelectric transducers with capacitive micromachined ultrasound transducers (CMUTs).
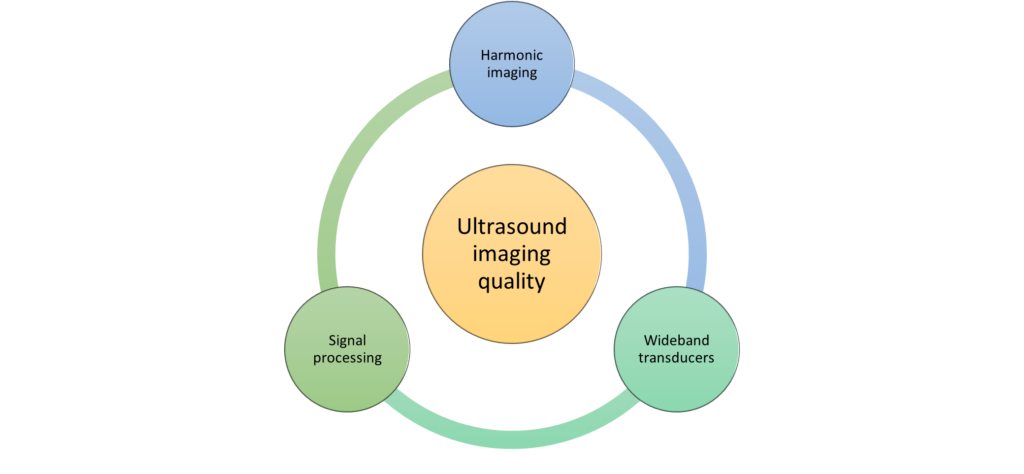
Piezoelectric transducers vs CMUTs
Conventional ultrasound probes rely on piezoelectric transducers, where the same piezoelectric component functions as both transmitter and receiver for sound waves – like a combined loudspeaker and microphone. However, the piezoelectric transducers have bandwidth limitations. Furthermore, acoustic properties of piezoelectric materials differ significantly from those of tissues, resulting in ineffective sound transmission between the piezoelectric material and the tissues. To overcome the mismatch in the acoustic properties, it is necessary to employ acoustic matching layers between the piezoelectric layer and the tissues.
As an alternative to piezoelectric transducers, capacitive micromachined ultrasound transducers (CMUTs) have gained interest because of their potential advantages over the conventional transducers. The CMUTs offer the possibility of broad bandwidth and high sensitivity, and they can be integrated directly with the electronic system. Therefore, CMUTs can create compact sensing devices for ultrasound imaging. The CMUTs are made by standard lithography processes, which can be suitable for mass production at high volume and low cost. Nevertheless, CMUTs possess some drawbacks, such as requiring a high DC bias voltage (some hundreds of volts), low transmit power and inherent nonlinearity.
Best of two worlds – DHUT
We combine a piezoelectric transducer and a CMUT into a single acoustic stack, called a dual frequency hybrid ultrasound transducer – DHUT. The DHUT uses a piezoelectric material for sending waves and a CMUT for receiving reflected waves. With this unique structure, the DHUT possesses the strong transmit power of the piezoelectric material, and the broad receiving bandwidth of the CMUT. These features make the DHUT promising for improving the quality of ultrasound images.
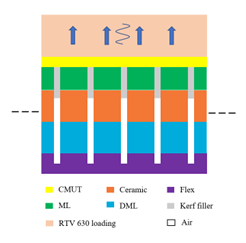
How to make and test DHUTs?
A DHUT contains a piezoelectric array and a CMUT, and the fabrication of a DHUT involves simultaneous fabrication of the piezoelectric array and the CMUT array. The piezoelectric array is constructed at USN while the CMUT is produced at Aculab, Roma Tre University, Italy. The piezoelectric arrays are sent to Aculab for lamination with the CMUT.
Several prototypes of the piezoelectric array have been dispatched to Aculab and are presently waiting for CMUT attachment. The completed prototypes will be returned to USN for testing. GE Ultrasound Vingmed are developing an electronic system for integrating the DHUT probe into GE’s ultrasound systems. When finished, this will give us an exciting opportunity to evaluate the imaging capabilities of our new technology, and to compare this with a traditional ultrasound imaging probe.
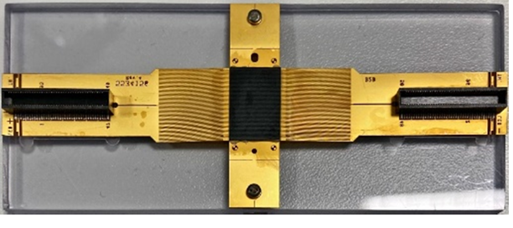
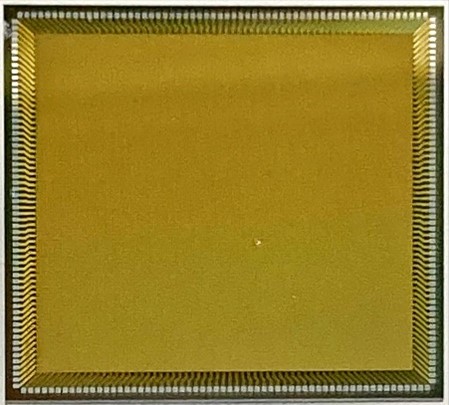
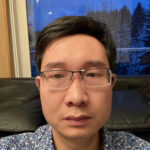
Duy Hoang Le
- This author does not have any more posts.